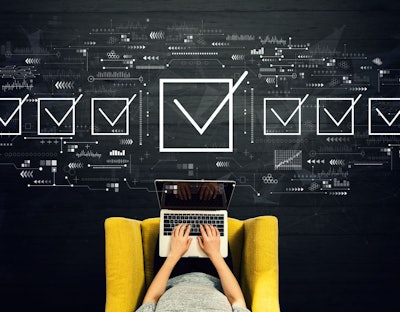
Even though a formula may appear feasible, a reality check should be performed.
By this time, the feed formulation system should be ready to produce its first formula. In the past five issues, we established all necessary steps to reach this point with success. Let us then click on the “solve” button to receive the first formula.
The least cost formulation concept relies on a multitude of possible solutions (often in the hundreds or thousands), from which it picks the least expensive to present to us. And this is the first reality check, because if something was not set up right, the result will be “unfeasible,” to use the formulation terminology. It means something prevented a solution that would meet all criteria imposed. So, first, let us check what may have gone wrong.
A. Infeasible solutions and their remedies
Most software programs will highlight in red the parameters that caused the program to reach a feasible solution. In most cases, this is because a nutrient specification was not able to be covered sufficiently because there was no such supply ingredient provided, all ingredients contained less than required or there was not enough formulation space to include more of that nutrient (this is the least possible cause). For example, if sodium is set to 0.3% and no salt or other sodium-providing ingredient is offered, then most conventional ingredients will not contain enough sodium to cover this specification. One solution would be to lower the specification and another would be to provide the right ingredient. In some cases, where everything appears in order, it might be that some nutrient has been entered incorrectly in the nutrient matrix, so double checking the numbers behind the scene might be the last step to resolve this problem.
Another cause of an infeasible solution might be that not enough ingredients are provided to meet all required nutrients and cover 100% of the required formulation space. For example, if only soybean meal and salt are provided, and there are minimum and maximum specifications set on critical nutrients for these two ingredients, then it is unlikely the energy or most other nutrients will be met. A final reason for an infeasible solution could be that we set such a high inclusion rate for an ingredient that it leaves little room for other ingredients to enter at sufficient levels to meet the nutrient specifications. In general, the fewer constraints we place on the software program, the fewer chances we have to encounter an infeasible solution.
B. Feasible solutions that are unrealistic
If we use the full possible range of ingredients and set a minimum on energy and sodium, the program will pull just enough corn (or any other cereal or energy source) to meet the energy requirement, and then it will fill up with salt (which happens to be the least expensive ingredient available). This may be a feasible solution, but it is not a realistic one as we cannot feed such feed to animals. In this case, experience tells us that we must place a maximum at such points (here it would be sodium) to prevent such unrealistic solutions.
The best remedy to avoid unrealistic solutions is to have at hand an example formula that is complete and correct. Then, we can compare the basics (energy, protein, fiber, minerals, etc.) and ensure that we are heading toward the right direction. To this end, the set of formulas presented in Feed Strategy’s Animal Feed Formulations Library can become a reference guide, but not the golden rule. Another solution is to have a list of items to be checked, for example:
- Are all ingredient minimum and maximum constraints met within reasonable ranges?
- Are nutrient specifications close to their required levels?
- Does the proposed solution look like a normal diet?
- Have I included all nutrients/ingredients that I need to check?
The latter is often a reason why some formulas may be feasible but not realistic. For example, many times we forget a nutrient (such as potassium), but we use an ingredient quite low in it. The formula may be solved, but the final feed will be deficient in potassium. Or, by simple human error, we might forget to include a fixed ingredient such as an additive or a vitamin premix. Having a list of nutrients and ingredients that need to be checked always helps.
C. A second checkup is essential
I often encounter clients who depend on the computer to formulate feeds for them. They do not use a nutritionist to check the formulas. In many cases, this is fine because the formulas contain simple ingredients, such as corn and soybean, and the feed professional handling the computer formulation system is knowledgeable enough to run the necessary checks as described above. In some more professional firms, however, a Ph.D. nutritionist is required to check the final formula. In my first job, the policy was that, after the nutrition assistant (usually a master of science graduate) formulated the feed I ordered, then I had to check it (and sign it) with a second signature required by another Ph.D. nutritionist before releasing it to production. This has become a habit for me now, and I always require a second set of eyes to double-check my work, even though I now work as a consultant.
In brief
First, ensure the formula is feasible and check anything that prevents it from becoming so. When the formula appears feasible, run a reality check, and when fully satisfied, have another experienced person double-check it.