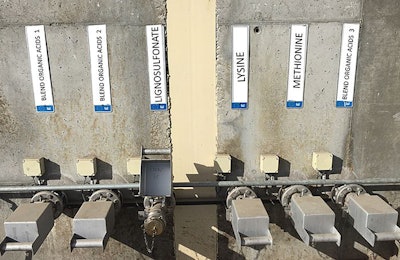
From the spraying of organic acids on raw materials to multiple ingredients in the mixer, the use of liquids in feed manufacturing is common at many stages in processing.
Since its launch more than 30 years ago, for example, liquid methionine is used in more than 50% of production in some markets, i.e. in the United States and Mexico. In the Middle East and Southeast Asia, the use of liquid methionine is growing due to market concentration and increased automatization.
Liquid methionine penetration often reaches as much as 80% to 90% for integrators and large feed millers.
This article highlights the experiences feed industry stakeholders have had with liquid methionine and other liquid products.
Advantages and limits of liquid raw materials and additives. (Adisseo)
Cooperative utilizes liquid raw material, additives in its new plant
COBADU, a Zamora, Spain-based cooperative with 10,000 members, produces feed for ruminants, swine and poultry in one plant in split into four separate units.
COBADU team (left to right): Eduardo Bueno Salvador, technical director; Fernando Antunez Garcia, deputy general manager and financial director; and Diego Bernal Garcia, nutritionist. (Courtesy Adisseo)
In 2016, COBADU built a new unit that utilizes many liquid ingredients, which are stored in tanks, including soybean oil, palm oil, olive oil, animal fat, molasses, lignosulfonate, blends of organic acids, methionine, lysine, xylanases and phytases.
COBADU partnered with Mangra, a Spanish company specialist of liquid products application, to work on this project.
Fernando Antunez Garcia, COBADU’s deputy general manager and financial director and president of the Spanish Association of Feed Manufacturers (CESFAC), explains that the cooperative chose to include mainly liquids in this new unit because “they are efficient and cost effective.”
The equipment investment is higher at first than for powder additives, he says, but becomes cheaper over time due to labor savings offered by automated systems.
“Liquid additives is way of the future and a way to increase competitiveness,” Antunez Garcia says.
COBADU Technical Director Eduardo Bueno Salvador sees the advantage of having no dust, which decreases explosion risk in the plant and the breathing of fine particles by workers.
“An automatic system for a same quality of feed than with the powder forms,” Salvador says.
The COBADU team feels liquid products make the daily routine easier, e.g. trucks unload quickly and no manual labor as required when transporting bagged product to storage and production. With liquid ingredients, all product is stored in tanks and ready to use.
COBADU produces more than 600,000 tons of feed annually.
All liquid products used in COBADU are dosed automatically by flowmeters. (Courtesy Adisseo)
Additive supplier shares benefits of liquid lysine
Liquid lysine is a competitive source of lysine available in the European market, says Ajinomoto Animal Nutrition Europe’s deputy sales director-EMEA, Pierre Tillé.
With its production facility in France, it has very much developed in Western Europe where liquid lysine represents between 20% and 50% of the market depending on the country. Customers use liquid lysine because it provides easy handling, accurate dosing and homogenous inclusion.
The technological advantages for liquids, as seen by COBADU, are matching the perceived advantages of Ajinomoto customers for liquid lysine on handling or absence of dust emission.
For such key additives, one should ensure a visibility on the availability of products in the future, e.g. additive authorization regulations.
Customers must feel confident in the stability of the supply, which is the case for liquid lysine, Tillé says.
In the context of the lysine re-authorization process in Europe, European Food Safety Administration (EFSA) has published five positive opinions on different liquid lysine products.
Liquid product usage increasing in new feed production lines
Engineering company EDEIS sees more feed producers adding liquid applications to new production plants. EDEIS’ managing director Albert Selosse notes that as new organization standards for plants are aimed at maximizing feed quality and safety. In terms of building and equipment organization, this means sectorization, go-forward principle, special building design with smooth walls, cleanability, etc.
Formulation is also an evolving field. According to Selosse, liquid additives and ingredients are being used more for several reasons:
- No handling for liquid allows a higher automatization level of dosage and better efficiency.
- Liquids are easier to transfer. (Powders need to go through a gravitational system, which affects plant organization.)
- Liquids offer better flexibility and contribute to better plant ergonomics, with possible longer distances between storage and addition place.
France Mélasses quality manager Simon Nicaud and sales director Benjamin Waldhoff. (Courtesy France Mélasses)
Liquid raw materials deliver value for customers
France Mélasses, part of the holding United Molasses, produces only liquid products including protein concentrates and molasses, which were the first liquids applied in feed.
France Mélasses quality manager Simon Nicaud and sales director Benjamin Waldhoff feel liquid products have economic and technological benefits: protein concentrate replaces a part of protein from raw material in a cheaper way and molasses enhance pellet durability and hardness.
Lignosulfonates in liquid are preferred by some customers as the powder form is hygroscopic and may cause caking.
Molasses are also known to enhance the craving for ruminant feed.
In addition, a liquid can be a vector for other additives, for example, aroma added in molasses.
From this perspective, liquids allow an improved working environment and show satisfying performance in feed.
Liquid’s popularity grows
Liquid feed ingredients and additives are a major and standard part of the daily organization of a feed mill. They provide an improved working and production environment and show satisfying performance in feed.
Depending on feed mill and the type of feed, their inclusion rate in feed formulation varies from a minimum of 3%, up to about 8%, and sometimes more in specific formula, e.g. formulations with high levels of molasses or oils.
Therefore, feed formulators, in close partnership with production managers, must regularly assess the economic and technical benefits of liquid solutions. Product suppliers, equipment companies and engineering firms are here to support them.