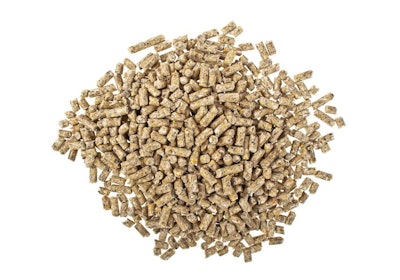
Following proper conditioning principles can achieve several benefits, according to Tony Osmundson of Andritz, who spoke at IPPE
Conditioning, or adding heat and moisture in the feed mill during the pelleting process, is a way to optimize pellet quality, but proper methods must be used to achieve the best results, according to Tony Osmundson, territory manager – capital equipment, dies and rolls, Midwest U.S. for Andritz Inc.
Osmundson spoke January 25 during a TECHTalk at the International Production & Processing Expo in Atlanta.
“We want to make more pellets and we want to make better pellets. Conditioning is a gateway to help you get there,” he said.
Conditioning mash prior to pelleting can achieve several benefits, including better throughput, better pellet quality, improved energy consumption, higher feed conversion and reduction of microbial growth.
“When we talk about conditioning, the first thing we need to understand is that conditioning only plays a part in the ability to pellet something and pellet quality,” Osmundson said. “So, when we look at conditioning, 60% of the ability of pellet something and pellet quality happens before it ever gets to the conditioner. That 60% is made up of formulation and particle size.”
The right ingredients must be present in the formulation in order for it to be properly conditioned and pelleted, and ingredients must be ground to the proper size for it to handle well and be pelleted.
Heat treating ingredients results in better feed conversion for poultry and swine.
“We’re almost pre-digesting that product when we get it heat treated like that. The animal doesn’t have to spend as much energy digesting the heat-treated product,” he said. “By properly conditioning, we’re going to increase the pellet quality. If we break those starches down, we can bind them back together when we cool the product and we’re going to make a harder pellet, a better pellet,” which will result in higher feed conversion and less selective feeding.
Be aware of ‘moisture threshold’ and steam quality
Typically, the highest moisture content that can run through a pellet mill is 16% to 17%. It can go a little higher in some cases, Osmundson said, but there is a “moisture threshold.”
“For any given formula in any given pellet mill on any given day with the ingredients you’re running, there’s a moisture threshold at which that pellet mill is going to slip a roll,” he said. “Normally, that is a moisture slip and it’s because we reach that moisture threshold where the pellet mill just physically can’t take any more moisture. And so what we want to do is be able to achieve the texture we’re trying to reach before we hit that moisture threshold where we’re going to slip rolls.”
The quality of the steam is also crucial to achieving good pellet quality.
“Part of conditioning is steam. We have to add steam, and proper steam is a huge key to conditioning,” Osmundson said. “You can put in the best equipment in the world, have formulation under control, and if you have terrible steam, you’re going to end up with a wet mess in your conditioner which is going to end up in your die and you’re going to struggle with it.”
He said achieving good quality steam is partly due to the sizing and maintenance of the boiler, but also proper pressure.
“We want to see about 100 psi in your boiler, and that needs to be a consistent pressure. We don’t want to see that boiler go down to 80 before it kicks into high fire and then go up to 100, because the temperature of that steam changes a lot when you do that. You want to try to close that window down,” he said.
The pellet mill should be running at between 20 and 40 psi, depending on steam quality, the products running through the mill and weather conditions.
“You want to feed the beast. The beast is the pellet mill; find out what it wants to eat,” he said. “If you can get control of the whole process, you can have some success. But if your boiler is running erratic or things aren’t running quite right from a formulation standpoint, or all different things are going on, it’s pretty difficult to make a proper pellet.”
Another thing to keep in mind, Osmundson said, is that heat treating can cause some ingredients to break down.
“The one thing with any conditioning today that we do have to be aware of … is what are we doing to enzymes, vitamins, those kinds of things. We have to be aware that once we reach a certain point, we start to degrade some of these things in our formulation. So then we either have to try to control temperature and not hit those temperatures that start breaking those enzymes and vitamins down or we have to overformulate so that, in the pellet, we have what we want,” he said.