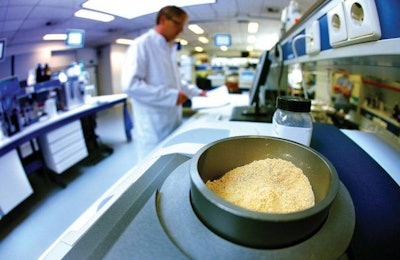
Advances in NIR technology and feed formulation software can deliver a lower carbon footprint, produce less waste
The animal feed industry can improve its sustainability by optimizing feed formulations, according to experts who spoke during the Feed Mill of the Future Conference at the International Production & Processing Expo in Atlanta on January 24.
By utilizing near-infrared (NIR) spectroscopy to determine variability in feed ingredients, producers can save on costs and formulation, according to Vinicius Chiappetta, global commercial director at Cargill Digital Solutions.
Feed ingredients have a natural variability and, if that is not considered, feed can be over- or underformulated, which can affect cost and animal performance.
“If it’s overformulation, you could be saving costs because you’re putting more nutrients in the feed than is really required,” he said. “Or, if you put in more nutrients, this can also impact the digestibility of the animals, because there is a precise level of nutrients that they can absorb. So even overformulating doesn’t mean that you are going to have a better performance at the farms. Or you can underformulate; if the nutrients come with a lower level of protein, for example, the feed is going to have lower levels of protein, and this is also going to impact the productivity at the farm.”
NIR measures how near-infrared light is reflected by a certain material and can detect the vibration of the organic molecules. Depending on how the vibration takes place, it can identify, for example, the protein, the fat and the water levels of a certain feed ingredient. NIR technology used alongside data management, automatic formulation and process automation can create a precision nutrition system.
Nutritionists include a safety factor of 0.5% in formulations to mitigate natural nutrient variation risks. The estimated impact of this practice is US$1.50 per metric ton of feed produced; that represents US$864,000 per year for a medium-size broiler integrator.
“There is a lot of money on the table by better understanding this variability and how to act on the diets and on the feed production at the feed mills,” Chiappetta said.
These costs could be mitigated with better nutritional uniformity of feed, increased management capacity at the feed mill, optimized usage of ingredients in formulation, the opportunity to improve supplier selection, feed costs savings and greater uniformity at the farm level.
“This is a big challenge in the poultry production to reduce the variability of the broilers, because at the end of the day, they all go to the processing plant and the productivity and the efficiency of the processing plant of the broilers is directly dependent on the uniformity of the chickens that arrive there, and many processing facilities cannot automate the production process because broilers are not uniform arriving there,” he said.
In-line NIR can work to minimize ingredient waste and, along with carbon management and measurement reporting and verification, can lead to more sustainable production.
“The industry has been working to produce more with less for years. So, I see a strong connection of this kind of technology on helping the world to be more and more sustainable and our contribution to the sustainability,” Chiappetta said.
Using software to reduce carbon footprint
Karel Vervaet, senior product specialist for nutrition at BESTMIX, explained how feed formulation software can figure in the carbon footprint of feed ingredients to determine a feed’s environmental impact.
Feed is animal production’s biggest contributor to climate change. Carbon footprint is one of the parameters that determines environmental impact of feed. By setting up carbon footprint as a nutrient in feed formulation software, the environmental impact from feed can be reduced.
“You just put constraints on the nutrients’ carbon footprint, and you’re able to reduce the emission of the feed itself,” he said.
For every ingredient, define the carbon footprint of that ingredient using any globally recognized standard.
“Once you have set it up as a nutrient, it’s pretty easy to visualize it in a recipe, to display it, to put it on labels, to print it on reports, to have it on tags,” he said.
Some advantages of this approach include its simple implementation, availability and ease of sharing with partners. However, Vervaet said, this method does not consider the origin of the ingredients, carbon footprint figures are not available for all raw materials, no other environmental figures such as land or water usage are included, and it focuses on feed only instead of the entire value chain.
A more complex analysis of the environmental impact of feed – a full life-cycle analysis (LCA) – looks at many more factors.
“When you’re doing a full life-cycle assessment of the entire value chain, you’re going to investigate way more than the feed alone. And therefore then, of course, the model becomes way more complex,” Vervaet said.
LCA provides information on acidification, climate change, eutrophication, land use, particulate matter and water footprint, among others.
“You consider 11 different parameters in the calculation. Not only do you get the information of 11 different parameters, but you’re also considering an independent index, the single-score impact, which is in fact a value that is trying to make an objective summary of all the different parameters that you have because climate change, eutrophication, acidification – they’re all measured with different units, and making sure that you have a unified index also allows you to see whether the entire environmental footprint of your feed goes up or down,” he said.
These parameters are much more important when analyzing the complete environmental impact of meat production.
“When you want to take this one step further, also working with these figures in feed formulation software will make the solution way more complex,” he said.
However, this method allows producers to zero in on each phase of production over the entire life cycle of the animal to understand the environmental impact along the supply chain.
“Once you have the software and once you’ve made the feeding programs, and you send the information to the software, you have the ability to really drill down and really look at the impact per category,” he said. “When you’re examining the climate change, you can really see which components of the feed and which components of the meat processing and which components of the livestock production are now important because, if I want to inform the farmer on how he can do better on manure management to get the environmental footprint of his feed or of his pig production down, I need to be able to do that.”
Formulation software and LCA allow producers to more easily take steps to improve sustainability and lower the environmental impact of feed production.
“You have everything you need to fulfill your own goal as a feed company to have more sustainable feed,” Vervaet said. “In the end, you’re doing your little piece of the puzzle solving, making sure that what you’re doing is less harmful for the environment.”
Feed Mill of the Future Conference was presented by Feed Strategy and Feed & Grain magazines.