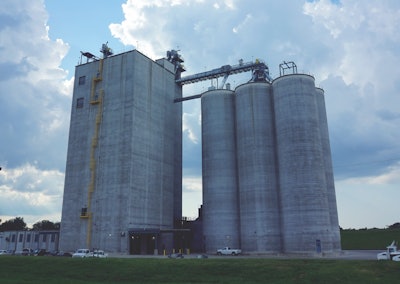
New Spruce Pine, Alabama, feed facility supports Mar-Jac Poultry LLC’s growth today; designed to double its capacity in the future.
Fully integrated poultry processor Mar-Jac Poultry has made strides to grow its production in Alabama with the recent construction of a greenfield, slip-form concrete feed mill, located in Spruce Pine.
The plans for the facility began shortly after Mar-Jac Poultry Inc., based in Gainesville, Georgia, purchased the assets of poultry integrator Marshall Durbin Companies in 2014. The sale included Durbin’s two poultry processing plants (Jasper, Alabama, and Hattiesburg, Mississippi); two hatcheries (Moulton, Alabama, and Waynesboro, Mississippi); and two feed mills (Haleyville, Alabama, and Waynesboro, Mississippi). These acquired assets now operate as Mar-Jac Poultry LLC, but as Keith Martin, Mar-Jac Poultry LLC’s live production manager, explains, “Geography is the primary distinction.”
2019 poultry outlook: 5 issues influencing feed production
According to WATT Poultry USA’s 2019 Top Poultry Companies report, Mar-Jac Poultry is the 15th largest broiler company in the United States.
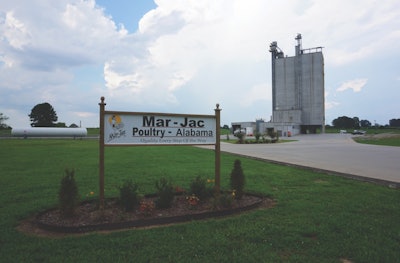
Mar-Jac invests in Alabama
From the very beginning, Mar-Jac planned to expand the Jasper, Alabama, processing facility’s output from 1.1 million head/day to 1.68 million. Mar-Jac leadership knew the decades-old Haleyville feed mill would not be able to handle any production increased, as it was operating beyond its capacity, so they began looking for property to build a new feed plant.
Through the economic development efforts of Franklin County, located in Northwestern Alabama, the Spruce Pine lot was scouted and purchased by Mar-Jac in 2016. The company hired design-build firm Younglove Construction, LLC, to head up the project.
After just over a year of construction, the $33 million feed mill came online in December of 2017, with the Haleyville mill completely shuddering the following month.
Today, the Spruce Pine complex serves 107 contract broiler growers, delivering 6,500 tons of feed within a 50-mile radius of the mill every week.
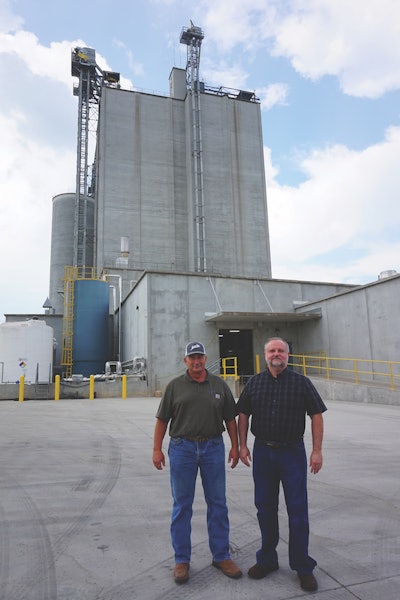
Built for growth
Mar-Jac Poultry built its new feed mill with the future in mind.
“[Mar-Jac] wasn’t looking just to meet our needs today, they went in considering what we’re going to need 15 or 20 years down the road,” says Martin. “Every aspect of this mill, from the loadout bay to the pellet floor, to the grinding room — everything’s built for growth.”
Currently, the feed mill’s production total production capacity is 10,000 tons per week; however, if the company decides to grow either by expanding an existing processing facility or by acquiring a new one, the Spruce Pine feed mill’s footprint was designed with space to accommodate an additional pellet line and hammer mill to double its capacity.
Grain receiving and storage
At the mill, raw materials are delivered by truck and rail. The mill utilizes its 250-ton/hour truck receiving system for grains brought in from Northern Alabama, Western Tennessee and Northern Mississippi. At least half of its ingredients are sourced locally.
By train, the mill boasts 40,000 bushels/hour of rail receiving, bringing in two to three Norfolk Southern deliveries per month, or about one train every 10 days, reports Jimmy Potter, the Spruce Pine feed mill manager.
Once unloaded, ingredients are then conveyed by one of three legs: soft stock, whole grain or ground grains. Whole grains are conveyed to the six 35-foot-diameter concrete silos, which consist of 505,000 bushels of grain storage as well as a 2,400-ton soybean meal bin. Soft stock and minerals move to the 23 ingredient bins, totaling 2,450-tons of storage above the batching system.
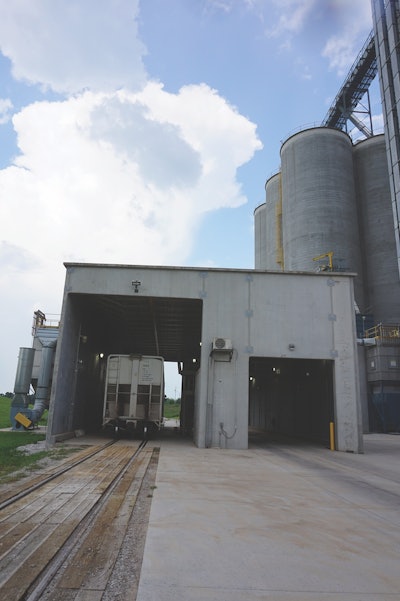
The mill operations are controlled by a Beta Raven automation control system.
The Spruce Pine feed mill manufactures three broiler and six breeder formulations. The company contracts its nutrition program with Devenish Nutrition Services, working closely with two nutrition consultants, Dr. Paul Twining and Dr. Mike Blair.
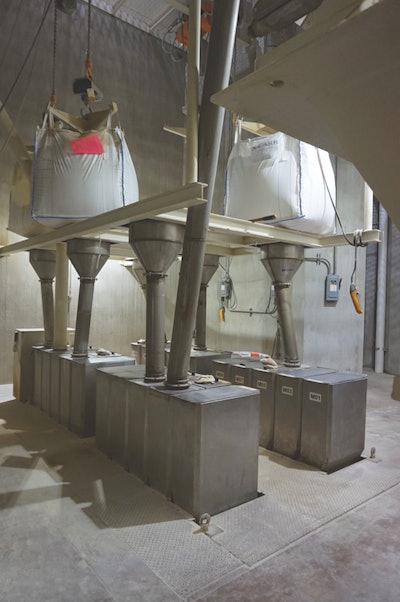
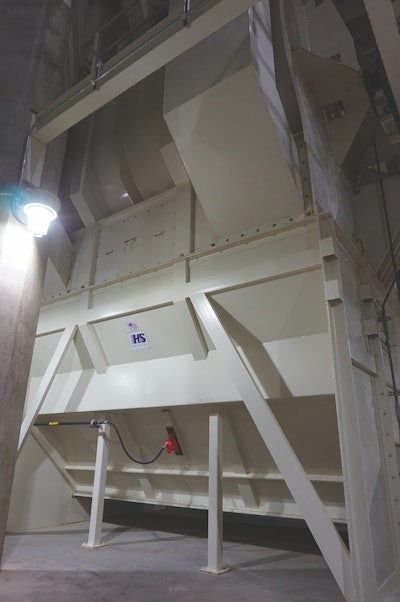
Inside the mill
The grinding system is housed in a separate concrete grinding building, featuring one 70-ton/hour Roskamp Champion HM44-56 hammermill, with space for the addition of a second hammermill. Processed grains are then conveyed to the ground and coarse grain ingredient bins.
The batching and mixing system utilizes two 6-ton major scales, a minor scale and a 20-bin Beta Raven micro system with dual scales, feeding into a Hayes & Stolz 12-ton mixer.
The mix is then either doled out to the mash feeder from the grader bins or moved to the pelleting tower, which features a CPM 9042 90-ton/hour pellet mill and, again, room for a second line in the future. Pellets are cooled in a Bliss 20-798-6A counterflow cooler before receiving a final fat coat in the APEC system housed in the mill headhouse.
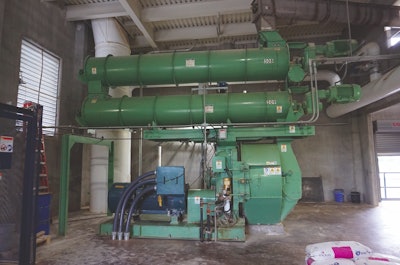
The mill features two finished feed loadout driveways with 4,400 tons of finished feed storage, held in 30 loadout bins.
“With the finished feed storage, it came down to do we put in one bay or two bays, and by putting in two bays, we have a large amount of bay feed storage,” Potter adds. “We have almost three days’ worth of feed in storage at any given time, but as we go up in tonnage, then we’ll need that storage unit.”
The mill loads roughly 50 feed trucks per day, 240 per week. It staffs an additional 10 full-time drivers, driving its eight-truck fleet.
Thirteen employees work in the Spruce Pine feed mill. It runs two shifts, five days of the week, and produces around 6,500 tons/week.
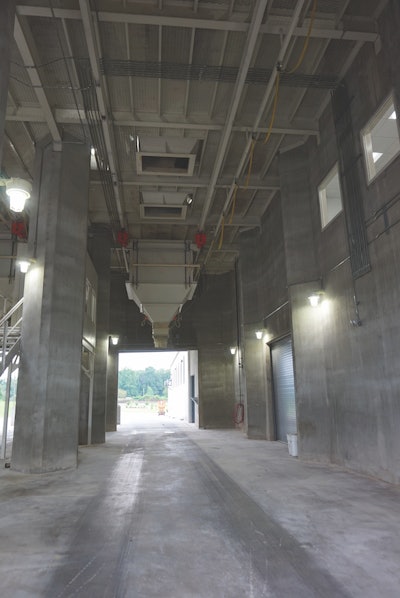
Opportunity to expand
Given its positive experience getting the Spruce Pine feed mill off the ground, Mar-Jac constructed a new hatchery a half-mile from the mill, which also began operation in 2018. The new state-of-the-art, fully automated, $23 million hatchery hatches 1.8 million chicks a week, using single-stage incubation and with the integration of energy-conserving technologies.
“The feed mill is the centerpiece of Mar-Jac’s presence in Franklin County, and this mill drove the existence of the new hatchery,” Martin explains. “We believe in doing business the old-fashioned way, and we’re committed to Franklin Country.”
Mar-Jac is currently exploring growth opportunities, but as Martin sees it, a lot of added demand will be found on the local level. In addition to servicing the large national fast food chains and wholesale distributors, Mar-Jac’s “sweet spot” lies with its small- and medium-sized regional customers.
“We do fast food, cut up and small bird deboning — that is our market,” he explains, “but as one of our former leaders once said, Mar-Jac made its name by hitting all of our customers regardless of the size of the order. If they only want five cases of chicken, Mar-Jac gets it on a truck and delivers it. We’re out there reaching the customer’s needs that maybe the larger integrators might not be paying that much attention to.”
Meanwhile, Mar-Jac also nurtures a robust international presence, exporting nearly 40% of its total production.
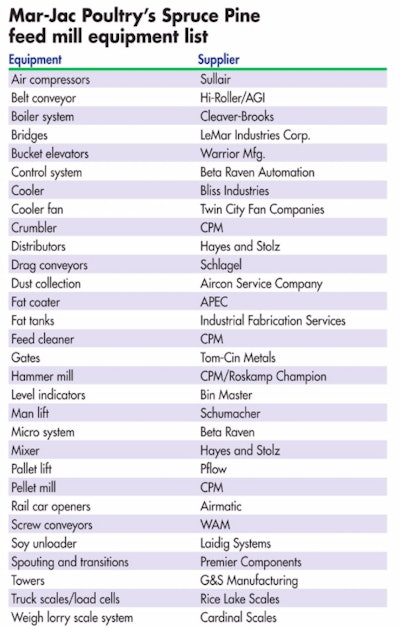