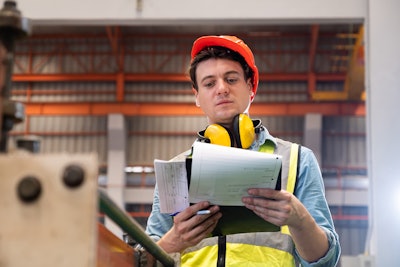
How does the feed industry’s safety record stack up? (07:32)
Ann Reus: Hello and welcome to the Feed Strategy podcast. I’m your host, Feed Strategy senior reporter Ann Reus.
Today I’m speaking once again with Gary Huddleston, director of feed manufacturing and regulatory affairs for the American Feed Industry Association. He’s here to talk about recently released data from the Occupational Safety and Health Administration about worker safety in the animal feed manufacturing industry.
Hi, Gary, thanks for coming back to be on the podcast again.
Gary Huddleston: Thanks for having me.
Reus: You recently wrote an article explaining how you analyzed data from the Occupational Safety and Health Administration, or OSHA, on worker safety in the feed industry. What were the key indicators you analyzed?
Huddleston: So, the average size of animal food manufacturing facilities that reported in 2022 was only 55.6 employees compared to the average size of all facilities, which was 765.5 employees. So, since there was such a vast difference between the size of the facilities, we needed to look at most of the data on a per employee basis to get a more true comparison. The main key indicators that we looked at were total injuries and illnesses per employee, total days away from work cases per employee, and total days away from work for employee. We also looked at total days away from work per case reported, as well as total deaths reported.
Reus: What were some of your findings in those categories?
Huddleston: Well, when I reviewed the data, the most positive item, that I found, that there were no deaths and animal food manufacturing facilities in 2022, compared to 853 in all facilities, so that was a good positive note. I also found that the total days away from work per case reported stood at slightly more than six days less for animal food manufacturing facilities when compared to the average for all facilities. And so when you put these two data points together, seems to point out that the animal food manufacturing facilities, their injuries and illnesses reported may not be quite as serious on average as for all the other facilities.
Reus: So, you found a lot of positive statistics on animal feed facilities, but you also found a couple of negatives. What were those and how can the industry do better in those areas?
Huddleston: So animal food facilities reported more injuries and illnesses per employee than the average of all facilities reporting. The average number of injuries and illnesses per employee for animal food manufacturing facilities was 24.2 for every 1,000 employees, while the average for all facilities reported was only 1.8 injuries per 1,000 employees. So that’s a pretty substantial difference of more than 22 injuries and illnesses for every 1,000 employees. So, while our injuries may not be as serious, we did report more of them. We also reported 10 more days-away-from-work cases for every 1,000 employees. And that’s a substantial difference. And the bad news is since we reported more days-away-from-work cases for employee as well as more injuries and illnesses, that resulted in 220 total more days away from work for every 1,000 employees in our industry compared to all the other industries, which again is a pretty substantial difference and leads me to the conclusion that we’ve got some room for improvement in our safety programs and animal food manufacturing facilities.
Reus: What are some weak points you’ve seen in facility safety programs that could always be improved?
Huddleston: Well, it seems clear that we’ve got some work to do in worker safety in our industry. I don’t really see any consistent weaknesses across our industry though. Many animal food manufacturing facilities really do an excellent job with their safety program. But every facility is different. Employee safety is improved when facilities focus on improving their safety culture. And so I encourage managers and supervisors, they should take time to review their safety logs, I highly recommend facilities have fully functioning safety committees, and that include both regular members of the workforce as well as managers and supervisors on that committee. Then regularly reviewing and discussing those safety logs in those committee meetings is a really good exercise for the committee and What type of injuries are you experiencing? Do you see any patterns or regularly reoccurring injuries? So your safety logs could point out some weaknesses in your facility safety programs and point out areas where maybe your employees need more training if you’re having more frequent injuries in certain areas of the plant.
Reus: What kind of training programs should feed mill employees and managers be taking part in on a regular basis to ensure worker safety?
Huddleston: So my recommendation would be to follow the applicable OSHA standards covered in 29 CFR 1910. And the basic list of recommended topics that most feed mills should be training employees on should include things like fall protection, emergency action plans, hearing protection and noise exposure, hazardous materials and the hazard communication standard, required personal protective equipment that you have at the facility, your confined space program at the facility, lockout/tagout procedures, fire protection equipment and procedures, powered industrial truck safety if you’ve got forklifts and other types of industrial trucks at the facility, machinery and guarding, hand and portable power tools is another good topic, hot work permits and requirements. Then housekeeping requirements that’s included in the grain handling facility standard, and then electrical safety. And all these items are covered in individual standards in CFR 1910, so that’s a good place to start. But you may want to include other topics like working in cold conditions, working in hot conditions, back injury prevention – back injuries are a fairly frequent type of injury in our industry – or other job, or site-specific topics that are relevant for your facility. Again, one of the best methods to determine whether your facility is training on all the needed topics is to review those safety logs and those accident reports and also recommend reviewing your facility and job hazard analysis; that gives you a good clue on items that you need to train employees on.
Reus: Well, thank you so much, Gary. This is good reminders on some really important information.
Huddleston: Thank you for having me.
Reus: You can learn more about OSHA’s Injury Tracking Application data, as well as the safety standards that Gary mentioned, at osha.gov.
Thanks for listening. I’m Ann Reus for Feed Strategy.