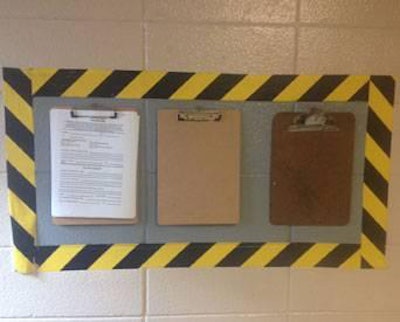
Feed mills with top safety records — in terms of both employee safety and feed quality – say it starts with a clear commitment from management. In other words, you have to walk the walk and talk the talk.
According to Mark Teel, North American safety director at Hi-Pro Feeds, there are two key goals at the root of every feed mill safety program: protecting employees and the food supply.
Rich Sladic, plant manager, Southern States Cooperative, agrees and notes how he assumes an aggressive stance on safety enforcement in his Winchester, Ky., feed mill.
“I’d rather have [an employee] madder than fire at me because I had to reprimand them or give them time off without pay than to make ‘that call’ to a wife or girlfriend,” he says, defining “that call” as being the one informing a significant other their loved one has been injured.
How do safety managers know when their employees have taken the safety message to heart?
According to Sladic, he knew when his staff started reporting near-misses incidents that occurred in their own homes. But how do managers foster this level of employee buy-in on the job?
Safety first
To help increase safety awareness, Southern States uses a Near Miss Program, which includes documentation of “near miss” incidents that could have potentially resulted in an accident. Such documentation and subsequent internal evaluation provides an opportunity for management to address the issue before the result is an accident or loss in the future.
The cooperative has installed reporting stations, i.e. clipboards and reporting forms fixed to the wall, throughout its facilities. This easy access prompts employees to jot down any incidents near their work area.
“It’s all part and parcel of safety,” Sladic says. “If you see something, document it. This starts the whole process of addressing the concern.”
The Winchester mill gets an average of five to seven near-miss reports each month. Each report is reviewed with employees at the monthly safety meeting. Management then follows through and corrects any potential hazards. When a manager acts on the reports, it shows the employees that their concerns are being heard and safety is a high priority to the company.
“If we act as a one team and look out for each other, everybody goes home at the end of the day and has safe food to eat,” notes Teel. “We are accountable for ourselves and others as well.”
Different mills, different issue
When Wenger Feeds began revamping its safety program, it developed a safety committee, which included a representative from each mill. However, soon after Rebecca Ranck was brought onboard as the company’s safety manager, she realized each of the company’s facilities faced vastly different issues.
In response to these unique needs, each facility now has its own safety committee. Each committee includes a supervisor and at least one person from each of its three shifts. Prior to each quarterly meeting, the teams inspect the plants for both safety and housekeeping concerns. If problems are noted during the inspection, supervisors provide her with an update within one month regarding their progress in rectifying the problem.
“Follow up is critical,” Ranck says. “If it’s not addressed in a month, we ask, ‘Why not?’”
Jamie Rowley, chief administrative officer for Wenger Feeds, doesn’t feel safety programs can properly be run from a corporate office, so a hand-on approach is required for the best results.
“Rebecca visits the sites on a regular basis,” Rowley says. As a result of her level of involvement, employees are more willing to approach Ranck with their safety concerns.
Should a company offer safety incentives?
Ranck revisited the company’s long-standing safety incentive program. She reworked the criteria to evaluate employees based on their individual safety performances and how the teams worked together. Proactive safety measures were rewarded through several bonus programs.
“In a perfect world, having individuals go home safe and sound at the end of the day would be enough,” Rowley says, noting that a little impetus to be safe can be a real plus. Wenger Feeds tries to recognize employee efforts throughout the year and at the annual safety and service banquet.
Hi-Pro Feeds, on the other hand, has worked to simplify its safety program by emphasizing what it costs not to be safe. Teel explains: “It’s about choices. If I can make the reality about the risks of the choices made, hopefully I can change the behavior.”
Securing employee buy-in
No matter how carefully an employee safety program or preventive control program is crafted, it is only effective when it is followed. Clearly explaining to employees why the new procedure is important and exactly what employees need to do works as well as offering incentives.
Wenger Feeds revamped its training programs by make them more interactive and as applicable as possible. It holds short, frequent training sessions focusing on one topic or new procedure.
Oftentimes, employees working too close to a problem fail to see it. To combat this, Sladic uses employees from different parts of the company to walk through the plant with him. For example, the administrative staff or salespeople may point things out that others more familiar with the mill may overlook. A fresh set of eyes looking at the facility offers a new perspective and is one of the cheapest ways to improve a safety plan.
When employees come up to Sladic and tell him they can’t thank him enough for creating safe work conditions, he knows the approach is working.
“That tells me a lot,” says Sladic. “He gets it. He understands the importance of working in safe conditions.”