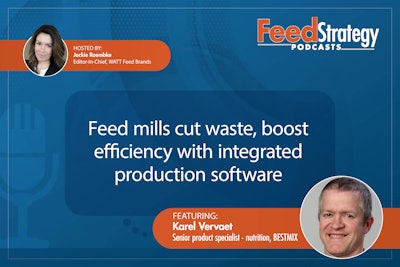
In this episode of Feed Strategy Podcast, Karel Vervaet, BESTMIX senior product specialist - nutrition, discusses how feed formulation software has evolved from a simple recipe creation tool into an integrated solution that helps feed manufacturers optimize their entire operation.
The discussion covers inventory management, real-time analytics, equipment performance, regulatory compliance and the future role of AI in feed manufacturing. Vervaet offers tips for how manufacturers can use software tools to reduce storage costs, implement just-in-time production strategies, standardize processes across facilities, and ensure consistent product quality while maintaining regulatory compliance.
Transcript of interview with Karel Vervaet, senior product specialist for nutrition, BESTMIX
JACKIE ROEMBKE, EDITOR-IN-CHIEF, WATT FEED BRANDS: Hi everyone. Welcome to Feed Strategy podcast. I'm your host Jackie Roembke, editor-in-chief of Watt's feed brands.
This edition of Feed Strategy podcast is brought to you by feedstrategy.com. Feedstrategy.com is your source for the latest news and leading-edge analysis of the global animal feed industry.
Today we're joined by Karel Vervaet, senior product specialist for nutrition at BESTMIX. He's here to examine feed mill efficiency techniques.
Hi Karel, how are you today?
VERVAET: Hi Jackie. I'm doing well, thank you.
ROEMBKE: Well, let's get right into it. Moving beyond traditional recipe creation, how can feed formulation software help manufacturers become more strategic in their overall production planning and scheduling?
VERVAET: That's quite a comprehensive question to start with. When you look at traditional recipe formulation in the past and compare it with today's software architecture at feed companies, it has become more of an integrated solution. In the past, you had separate departments –recipe formulation, purchasing, sales – all working independently. Now when we look at how software is implemented, it's a truly integrated solution that follows business processes.
The boundaries between recipe management and production have become increasingly fluid. Where, traditionally, recipe creation information was printed or sent through files to production, now factory staff can fine-tune production orders with the latest information about lots, qualities and prices. They can optimize production to fit quality requirements and strategic production plans.
ROEMBKE: You mentioned integration. How does that translate to inventory tracking and management? How are manufacturers using these tools to minimize waste, reduce storage costs and create more of a dynamic just-in-time production strategy?
VERVAET: With today's raw material market volatility, manufacturers want to optimize their purchasing timing. Storage is costly, so having software tools for accurate forecasting is essential. You need to predict what you'll sell and therefore what you need to produce.
The formulation department can now use tools to formulate the entire recipe portfolio across multiple mills simultaneously. They can predict raw material needs – from macro materials to minerals – based on sales forecasts. With the right software tools for shipping, transportation and logistics, you can get materials at the factory exactly when needed.
Many purchase department staff now use formulation software to evaluate whether to buy certain raw material lots and if they're priced appropriately. With multiple production facilities, making the right decisions can save thousands in costs. But achieving this just-in-time strategy requires formulation software working together with sales and purchasing in an integrated way.
ROEMBKE: How do the real-time analytic capabilities work when immediate decisions about ingredient substitution are required, such as during supply chain disruptions?
VERVAET: Logistics can be challenging – delayed trucks, stuck canals, geopolitical disruptions. There are multiple ways formulation software can handle this. You could do a one-to-one replacement with a similar raw material to keep the mill running, though that's not always optimal. The software allows you to remove one raw material, replace it with another, and automatically recreate products, update ERP systems, and generate new legally required labels with just a few clicks.
A better solution is to re-optimize the entire scenario in a multi-blend environment. This ensures all quality parameters are met while finding the most cost-effective way to handle the disruption. The output still needs to be processed by creating new products, labels, adding medication where needed, and making private label products.
ROEMBKE: To what extent can the software predict equipment performance and maintenance to help avoid production interruptions?
VERVAET: This is where we're starting to use artificial intelligence. Factory equipment has many sensors providing data. If we can correlate equipment setup with quality output and formulation, we can adjust formulations to achieve desired results given the equipment parameters.
For example, we're currently using AI to optimize extruder settings for optimal pellet production. By combining historical data with AI predictions, we can help achieve better pellet quality with less production interruption and rework. The formulation becomes one of many input parameters the AI uses to predict and optimize equipment settings.
ROEMBKE: Earlier, you mentioned manufacturers operating multiple production facilities. How does your software help standardize processes, ensure consistent quality and create unified operational approaches across different locations?
VERVAET: Having a centralized system with all production facility information in one database is key. This allows for analytics, comparing similar products across locations, and easier product management guidance. When everyone works in the same environment, product management can better oversee quality and raw material usage.
The system can account for regional differences in raw material quality and pricing. If you have facilities in different regions, raw materials may come from different suppliers with varying qualities. The formulation software ensures the end product meets quality standards regardless of production location. A centralized system provides consistency in operations, guidelines and regulatory compliance.
ROEMBKE: What do the cost savings or production improvements typically look like in these optimal scenarios you've mentioned, and how would you quantify the typical operational efficiencies?
VERVAET: Rather than cutting staff, it's about optimizing their work to focus on what matters most. With automated labeling, creating compliant labels becomes a one-button process instead of a time-consuming task. Integration with ERP, mill systems and quality systems eliminates manual data entry.
Studies show multi-blend optimization can save up to 1% on raw material costs – significant in the feed industry. Managing moisture loss during production can save another half percent. Combined, that's tens or hundreds of thousands in annual savings.
The software also handles regulatory compliance, partnering with industry experts for safety data sheets and carbon footprint calculations. This allows staff to focus on core tasks like feed formulation while automating administrative work.
ROEMBKE: How is the regulatory element maintained? Is it tailored by region for export markets?
VERVAET: The main focus is labeling compliance. The software incorporates regulations like the U.S. Compendium and EU declaration requirements, automatically updating warnings, cautions and drug information for medicated feeds. It validates feed formulations to prevent issues — for example, flagging if sheep feed contains harmful copper levels.
Beyond legal requirements, the system enforces product management specifications. If a raw material substitution compromises claims like GMO-free status, the software alerts users before production proceeds.
ROEMBKE: What are the most significant operational barriers feed manufacturers face when implementing advanced formulation software?
VERVAET: There are three main barriers. First, transferring a company's intellectual property from existing systems is a major decision. Second, overcoming legacy habits from long-term employees who are comfortable with existing tools. Third, implementation requires significant time investment beyond regular duties. Management needs to allocate proper resources for successful adoption.
ROEMBKE: Looking ahead, how do you see feed manufacturing software evolving to provide more comprehensive operational intelligence, particularly with AI and predictive analytics?
VERVAET: While AI might help predict formulations based on nutritional profiles, the variability of natural raw materials makes complete automation unlikely near-term. AI will more likely assist in analyzing farm performance indicators to optimize rations and improve production efficiency. But in feed formulation itself, AI will remain a support tool rather than replacing human expertise.
ROEMBKE: Thank you so much for your time today, and thanks to everybody who tuned in.
VERVAET: Thank you. Bye bye.