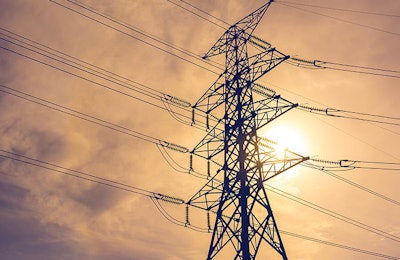
Equipment manufacturers and consultancy groups are changing the way the feed industry looks at moisture and temperature with new technology that improves energy efficiency. The new technology uses data on moisture and temperature to fine-tune processing so that it uses less energy, saves time and produces a quality end product.
“Everyone wants to produce feed the most energy-efficient way,” says Zetadec researcher Oriane Guérin. She explains that equally or more important is that feed mills can process large quantities of quality pellets that are efficient for the animal. Risking feed quality and volume for the sake of improving energy costs isn’t an option.
With this in mind, Zetadec says it is important to integrate hardware, software and data to optimize processing.
“The idea is to combine data with knowledge to make processing more optimal,” says Guérin. “If we use the same material every day, then it is fine, but we are always using different materials, so we are always fine-tuning.”
If manufacturers can cut back on time that is spent in trial and error, such as adding moisture or drying, as well as minimize the amount of energy that is spent correcting recipes, then they will have a higher pellet quality. This will also increase the capacity of the line with a process that is more accurate.
Rising interest in energy
In the past, volume and feed quality have been the largest influencers for feed mills. However, the growing pressure from the end consumer and new legislation for green production practices has piqued the industry’s interest in energy efficiency.
“We’ve seen an increase in feed manufacturers that contact us for audits because they want to be more efficient,” says Guérin. Zetadec helps feed manufacturers optimize production by performing an on-site audit of the mill. The audit helps pinpoint where a mill can optimize its process and equipment.
The first step of the audit is to see if there is a place for improvement, and then to analyze the manufacturer’s data to see where production can be optimized.
Steam quality is often a problem. Instead of bringing in heat and moisture, mills struggle with bringing in hot water — this changes the parameters and affects the quality of feed as well as slows down the process.
Optimizing thermal energy for efficiency, quality
In response to steam quality issues often seen in the field, Dutch company Van Aarsen introduced redesigned key steps in the steam systems to improve the pelleting process.
“One of the most undervalued factors, that has a huge impact on energy efficiency, is the steam conditioning process before the pelleting,” says Van Aarsen product manager Hans Boonen. “This is where you can have the most influence on both energy and pellet quality — next to the pellet mill die.”
The new system is designed to create the right quality of dry, saturated steam. This ensures the steam is free from condensate so that it has a linear relationship with the moisture that is added. This helps to control the temperature and the amount of moisture in the conditioner and results in a constant product quality that is made using the optimum amount of energy. Reducing the amount of condensate also prolongs the life of the equipment. The excess condensate is sent back to the boiler and used for new steam production.
Another key improvement to the design is the steam dosing control. This controls the amount of steam that is added to the conditioner based on the temperature of the feed exiting the conditioner and the desired temperature as specified by the operator. The high accuracy of the new system prevents inadvertently adding too much steam and damaging the nutritional quality.
With the new steam-dosing systems combined with Van Aarsen’s latest pellet mill automation software, operators are also able to add steam at production startup by a predictive calculation based on the feed rate. This speeds up the time before the meal is on temperature, enabling faster startup of the whole pelleting line, and reduces the amount of product recycle while waiting for the product to reach the correct temperature to start pelleting.
Van Aarsen has combined all three of these technologies plus a product flow regulation valve in its hot-start steam mixer.
The hot-start steam mixer takes efficiency to a new level by using data to calculate the correct amount of steam needed for processing. (Courtesy Van Aarsen)
“This new steam mixer takes efficiency to a whole new level,” Boonen explains. “Product recycle at the startup of the batch is not needed anymore to get to the right temperature for pelleting.”
The hot-start steam mixer adds steam using the predictive calculation technology while it is filled with product. This ensures that the product reaches the required temperature quickly. When the product reaches the correct temperature, the outlet valve is slowly opened to feed the pellet mill directly with guaranteed conditioned meal too ensure a stable temperature of the product within a very narrow bandwidth, even during production, as the filling degree is being kept at a high level.
“This whole hot-start procedure can be achieved in a very short time compared to existing solutions,” says Boonen.
He explains that the new hot-start steam mixer technology can reduce startup time for a pellet mill by up to 70 percent.
Better, cheaper, quicker processing
The growing demand from consumers for better energy efficiency is influencing the feed industry, but at the end of the day, the biggest influencers are still the moneymakers that help the industry cash flow, i.e. feed quality and quantity.
Moving forward, it’s important for feed manufacturers to see the connection between energy efficiency, processing time and product quality to improve their bottom line. Energy efficiency isn’t just a consumer demand, it is also a way to re-look at how the industry can produce more quality feed with less expense.