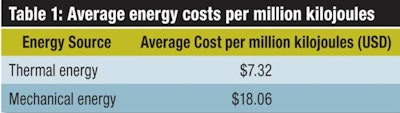
Higher energy costs continue to head the list of top challenges for the feed processing industry. Only food safety, raw material costs and labor issues consistently outrank these concerns. Energy requirements vary for the many aspects of feed processing, but within each unit operation, the total energy requirement and the energy source can significantly impact energy costs.
Energy source
Feed processing steps consume a certain amount of energy to accomplish the work required. The major sources of energy used in feed processing are either thermal or mechanical energy. In most regions of the world, mechanical energy will cost two to three times more than thermal energy when compared on a “per unit of energy” basis (Table 1).
To further illustrate the impact of energy sources on feed processing, steam-conditioning and extrusion-cooking, steps were chosen as example unit operations where the energy source and efficient utilization of that energy can significantly alter energy costs.
Steam conditioning
As the name implies, steam conditioning a feed material largely involves the use of steam as a thermal energy source. Steam conditioning in feed and food processing plants is often referred to as a “pre-conditioning” step as it is used as a preparatory or conditioning step to further processing steps such as pelleting or extrusion. The objectives of steam conditioning are to heat, hydrate and mix a feed material. How well each of these variables is accomplished is a measurement of the efficiency of the steam conditioner hardware being used. Table 2 lists four different steam conditioner designs utilized in the feed industry and the impact of each design on the uniformity of hydration and cook (level of starch gelatinization) for a feedstuff when processed through each design with the same operating parameters including steam consumption.
Note that the high-intensity pre-conditioner design had less product moisture variation (an indication of uniform hydration and excellent mixing) and higher product starch gelatinization levels (more efficient utilization of steam energy supplied) when compared with the other designs all operated at the same processing conditions — that is, consuming the same amount of energy.
Extrusion cooking and energy consumption
Aquatic feeds, pet foods and livestock feeds are often extrusion-cooked to pasteurize and shape the formulated recipe into a unique form for optimal feeding. The extrusion cooking process (Figure 1) will also destroy growth inhibitors and improve digestibility and palatability of the feedstuff. Every application of extrusion cooking requires a certain level of energy inputs to achieve the desired technical qualities in the final product. Thermal and mechanical energy are the major sources of energy in the extrusion process.
A review of current extrusion processes in the industry indicates that the common ratio of consumed thermal to mechanical energy ranges from 1:1 to 2:1. The thermal-to-mechanical energy ratio not only influences product characteristics, but also determines utility costs, maintenance costs (costs to replace worn product contact points) and the carbon footprint of the process. The ability to vary this energy-source ratio and shift to the most favorable energy sources from a cost standpoint brings flexibility to the cost of operating an extrusion processing line.
New extrusion technologies are designed to allow a shift in the consumed thermal/mechanical energy ratio from 1:1 to as much as 14:1.
Benefits of shifting energy sources
There are secondary benefits when an extrusion process has the flexibility to shift from one energy source to another beyond just taking advantage of lower energy cost inputs. Preliminary studies indicate there is less protein degradation and lower fat rancidity levels when thermal energy inputs are emphasized over mechanical energy inputs during extrusion. Recent studies in Brazil and the United States also indicate significant higher retention rates of important minor ingredients when thermal energy inputs are emphasized.
Recent developments in steam conditioners and extrusion technology have the potential to move a process to a more favorable energy source to reduce energy costs and to reduce associated maintenance costs. As energy costs continue to increase and more emphasis is placed on the carbon footprint of a process, innovative technologies will evolve to help the feed processor improve the efficiencies of the feed mill.