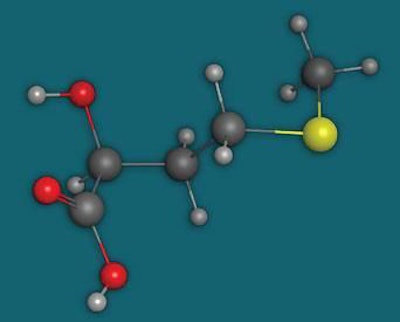
Methionine is the first limiting amino acid used in poultry feed formulation. If methionine is not supplemented in proper volumes, for example, the bird’s performance and growth are hindered. As an additive, methionine increases poultry yield, provides a cost-effective feed solution, and increases production efficiency.The additive itself is available on the world market in liquid and dry form. Globally, some regions, such as the United States and South America, dominate the demand for the liquid product; however, other parts of the world have been slower on the uptake. The reason can be attributed to several – equipment, product knowledge and logistics – but, perhaps, many feed mills are simply accustomed to working with tangible dry product in their daily operations and may not have explored the benefits of the liquid micro ingredient. “Millers are familiar with the macro liquids, such as fat and molasses, which make up 2 to 5 percent of the diet; however, they tend to be less familiar with the micro liquids – amino acids, lysine, methionine – because it is dosed in very small quantities,” said Jérôme Lamoine, feed technologist with Adisseo. “They are even less familiar with the nano liquids, like enzymes.” Naturally, dry and liquid methionine products produce the means to the same end; however, the key differences lie in the handling and equipment considerations taken with each material. From a feed manufacturer’s standpoint, the following article explores the benefits of liquid methionine, what feed mills should consider when installing a liquid system, and an overview of its potential downside.The benefits of liquid methionine Given the volume of methionine required in feed formulation, liquid methionine application is best suited for medium to large operations. Here is an overview of the production benefits liquid methionine can deliver to feed mills:1. Flexible equipment installation The installation of liquid tanks provides a flexible solution for mills looking to retrofit equipment within an existing footprint. For example, liquid methionine tanks can be installed inside or outside of the facility, and only minor adjustments are required to work a system into an existing footprint. According to Lamoine, the cost of investment for liquid dosing systems is less expensive than a dry dosing system with the same accuracy. However, this is not to say dry methionine silos do not also offer configurable installations. 2. Produces a homogenous mixture With the proper technology, liquid methionine mixes as homogenously as the dry product.3. Simple equipment, easy maintenance The liquid equipment tends to be reliable, and requires little maintenance and limited energy costs because it operates with fewer components than dry ingredient dosing systems, which are far more complicated. Liquid methionine dosing systems are easy to maintain, easy to install and easy to operate, says Lamoine. As with all machinery, adherence to a strict maintenance schedule is important to guarantee the equipment remains in working order.4. Inventory control The nature of liquids makes it easy for companies to track of liquid levels using inventory monitoring systems. “Liquid applications don’t experience the valleys and peaks on the tops of the silos like the dry ingredients do,” says Jeff Klopfenstein, president of Novus International’s methionine business unit, who also notes that tank storage also frees up space in the warehouse.5. Reduced labor costs Bagged dry methionine requires more handling – dumping bags and overall housekeeping – than its bulk counterpart. However, the liquid product requires very little handling and cleanup. According to Klopfenstein, virtually zero labor is required to administer liquid methionine because the feed mill’s batching system manages its application into the feed.6. Energy savings According to Klopfenstein, Novus’ new liquid methionine customers have experienced energy savings up to 12 percent in the pellet mill. “We’ve had customers take a year’s worth of electrical bills on dry methionine and compare it to a year’s worth of electrical bills on liquid methionine, and they’ve seen the energy reduction they attribute to making the switch,” he says. “We just have had such high acceptance of liquid that this is just a benefit that our customers take for granted, and they’re happy to pocket the savings.”The potential downside of liquid methionine While there are many benefits to liquid methionine, complications may present themselves once a system is implemented in the mill. “When looking at the total operation of the business – and not strictly in the convenience at the feed mill – I think [liquid methionine’s] downside is greater than the upside,” says John Thomson, director of nutrition and technical sales, Evonik Industries, the largest global supplier of methionine. “There are a lot of things to be considered, which are often not being taken into account because they’re just looking at liquids in isolation.” Thomson leans toward the dry product for the following reasons:1. Difficulties with uniformity “It’s certainly not impossible to get good uniformity with a liquid – it’s just more difficult,” Thomson says, noting that volumetric dosing is not as accurate as gravimetric dosing. “Liquids can be mixed just as well as dry products, but the effort involved is a lot greater. Liquids are typically sprayed into the mixer, but if your spray bar is not distributing the liquids evenly during the mixing process, the liquid will not disperse properly.” Achieving uniformity with liquid methionine sources has not been an issue, claims Klopfenstein.2. Increased mixing time According to Thomson, use of the liquid product increases the mixing time and “extends the period to batch feeds and reduces the output of your mill over time.” For example, an Evonik case study suggests the company was able to reduce mix time and increase its client’s feed ouput by nearly 15 percent when it transitioned from the liquid product to dry methionine. According to Novus, which offers dry and liquid methionine sources, feed mills have been using liquid methionine sources for decades and that precise dosing simplifies the production process while helping to efficiently manage costs.3. Equipment wear Accumulation in the mixer or on the spray nozzles may cause long-term deterioration and may increase the amount of maintenance, Thomson says.Is the demand for liquid methionine growing? Whether liquid or dry methionine is the best option depends on the feed mill and its specific needs. However, Adisseo and Novus cite increasing interest and potential for the liquid product. “We’re seeing a lot of growth in liquid methionine with the world’s fastest growing integrators and feed producers,” Klopfenstein says. “They want these benefits. They’re looking for every last thing they can do to shave a penny off the cost or dime off the cost of feed production. We’ve seen a lot of growth of our business simply through the growth of our customers.” Acceptance of liquid methionine continues to grow with feed manufacturers and integrators around the globe. Adisseo, for example, plans to will expand its liquid sales in the Asian Pacific and China to capitalize on this momentum.
Editor’s note: For the purposes of this article, “liquid methionine” is used as a general term and does not aim to distinguish the differences in the chemical compositions of the supplier’s individual products.