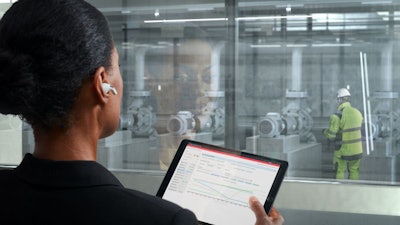
High-efficiency electric motors will power the feed industry into a greener future
Power is a critical, yet often overlooked, component of feed manufacturing. Powertrains convert electrical energy into motion for myriad feed manufacturing processes such as milling, grinding, mixing and pelleting.
However, as the energy crisis continues in Europe and climate change mitigation requires industries to consume less energy, now is the time to seek greener solutions for powering these processes.
Electric motors are the world’s leading power source, accounting for more than 45% of total electricity. That figure is expected to double to 90% by 2040 unless industries worldwide begin taking steps toward energy efficiency by conducting energy efficiency audits, employing digital energy monitoring and sensors, and using artificial intelligence to analyze building use patterns and adjust temperatures.
Below are three actions feed millers can take to improve energy efficiency and lower carbon emissions.
- Invest in high-efficiency motors with variable speed drives (VSDs)
Replacing outdated motors on feed processing equipment with high-efficiency motors and variable speed drives (VSD), which match input power to the operational requirements, holds vast potential for feed millers.
“Too many of the world’s electric motor-driven systems still use outdated and inefficient technology, and waste energy as a result,” said Mari E. Haapala, digital lead for ABB Motion, a provider of electrification and industrial automation technology. “Adopting high-efficiency electric motors with VSDs can make a major contribution to the success of the feed industry’s net-zero journey. Experts estimate around half of all industrial motors could be paired with a drive for greater efficiency, but the current rate of adoption across all industries is just 23%.”
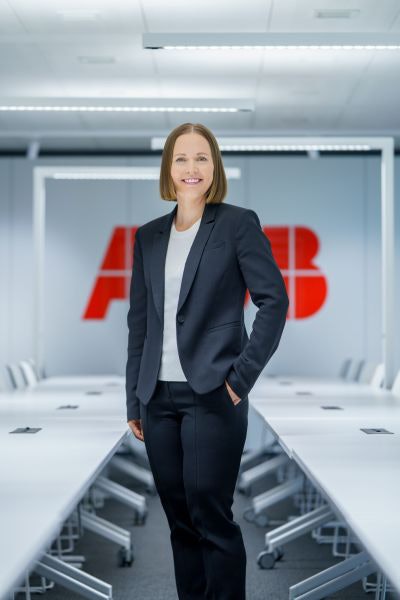
Motors used in feed milling applications may operate at low efficiency for many reasons: They may be older motors designed to a lower efficiency standard, they may be oversized and therefore underutilized, or they may be working at fixed speed without the efficiency advantages offered by a VSD.
While upgrading to higher efficiency models requires capital investment (there can be up to a 40% price differential), even marginal efficiency improvements can build up to significant energy savings.
“Independent research reveals that replacing the world’s 300 million-plus industrial electric motor drive systems with optimized, high-efficiency equipment could reduce global electricity consumption by 10%,” Haapala said. “To highlight what is possible, in 2020 alone, ABB’s installed base of high-efficiency motors and drives produced savings of over 198 terawatt hours — over three times the total annual electricity consumption of Switzerland.”
- Adapt to the industrial internet of things (IoT) and artificial intelligence
Recent developments in digitalization have made it possible to connect physical assets using the industrial internet of things (IoT). This enables a site’s operational team to gather data across all their motor-driven assets to monitor data such as vibration and operating temperature.
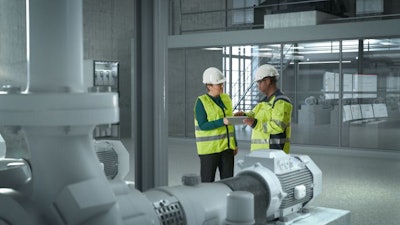
Analyzing this data not only shows when components are approaching failure, but it also provides plant managers at feed manufacturing facilities with insight to save budgets and reduce waste by switching to condition-based maintenance. This allows managers to schedule repairs and replace spare parts only when and where they’re needed.
“An expert in energy efficiency can take optimization to the next level by analyzing power and energy data from the same sources to identify how efficiently individual motors are running,” Haapala said. “They can pinpoint the biggest and best opportunities to save energy and CO2 emissions and cut utility bills, on a constant basis.
“The next step after identifying potential energy efficiency gains is to recommend remedial actions. These could include changing the operating schedule, upgrading to a modern high-efficiency motor, or installing a VSD. By costing these recommendations, it’s possible to calculate and compare the return on investment. Ultimately, the data provides the operator with confidence that they’re taking the right decision.”
Artificial intelligence (AI) increasingly supports this type of analysis. Using data gathered from a fleet of motors, sophisticated algorithms can identify key trends, indicating where energy experts should focus their attention.
“Ultimately, this may evolve into a full AI process, but at the moment, success relies on the combination of rich data and interpretation by human experts,” Haapala said.
- Electrify industrial vehicle fleets
The momentum behind electric vehicles is growing, thus bringing down the cost of batteries and electric drivetrains. Factors like prolonged high oil prices also make electric powertrains increasingly attractive for industrial vehicles like forklifts and delivery trucks.
Electric motors can reach more than 95% efficiency, while diesel engines only reach 45% efficiency at their optimum load range. For example, replacing the diesel engine in a 24-ton excavator with an electric powertrain, which combines battery power with a high-efficiency electric motor and drive, can eliminate 48 tons of CO2 emissions per year, according to ABB.
Vehicle electrification can immediately contribute to efficiency gains, even though financial gains in the short term will be minimal. Today, it’s more expensive to use electric vehicles for the transportation of goods than with traditional models, making the business case for switching less appealing on financial grounds alone. However, an electric vehicles’ average operating costs are as much as 60% lower than equivalent diesel engine-powered vehicles, due to improved efficiency, reduced fuel consumption, reduced maintenance needs and the ability to optimize charging schedules.
These are only three recommendations for speeding up the transition away from fossil fuels in feed manufacturing, but Haapala said others include carrying out energy audits, right-sizing industrial machines that are too big for the job at hand, switching gas boilers to heat pumps and using well-maintained heat exchangers.
“Through innovation, sharing knowledge and insight, investment and the right regulations and incentives, we can optimize energy efficiency and accelerate progress toward a decarbonized future for all,” Haapala said.
Feed Mill of the Future digital supplement
WATT’s feed brands Feed Strategy and Feed & Grain magazines join forces to launch the monthly Feed Mill of the Future digital supplement. Each edition aims to provide animal feed industry stakeholders with forward-looking content, market insights and a spotlight on the leading-edge technologies shaping the global feed industry of tomorrow.
Subscribe today! https://bit.ly/3dWzow7