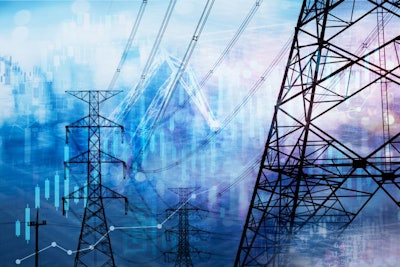
6 ways to use less energy in feed manufacturing
The war in Ukraine, along with other global events, has resulted in an unprecedented increase in energy cost across the collective Western world. All forms of energy that are used to power feed plants have been affected equally, as only very few such feed plants are energy self-sufficient. In some cases, governments are forced to subsidize energy costs, but funds are being rapidly exhausted. In fact, several countries in the EU have already alerted their heavy industry players to be ready for a winter scenario where electricity will be rationed. Some industries have made plans to move to other regions where energy cost remains acceptable for business.
It is inevitable that the feed industry will be equally affected. Most feeds need at least some degree of grinding, weighing, mixing, bagging and transporting across the mill – all requiring considerable amounts of energy, in most cases that being electricity. Feed mill managers across affected regions already have made plans to reduce energy consumption. One such measure is to schedule feed production during low-demand hours to avoid overloading the national network. In other cases, processes have been simplified, and low-volume products have been dropped (where possible) from their portfolio.
The animal nutritionist, who formulates feeds and decides on the type and number of ingredients to be used in each formula, can also be of use in reducing electricity usage at the plant. First, the nutritionist must have a sound knowledge on how feeds are made, and for that, it is unfortunate most universities do not offer more courses on feed production. For example, at Kansas State University, there is a whole department (grain sciences) where feed production is studied and taught to animal nutrition graduate students. I was fortunate enough to have been a student there and this knowledge has helped me tremendously in translating basic animal nutrition into practical, applied animal feeds and feeding practices.
With all that in mind and based on personal experiences and discussions across my network, I offer the following six topics that can be discussed with interested parties as a means of reducing electricity usage. In most cases, there is going to be a decision regarding profitability as it balances between sacrifices in animal performance and cost of feed – but that has always been the role of any Ph.D. field nutritionist for as long as I have been working in this industry.
- Pellet size. Sometimes we pellet certain feeds only to make a difference in the market as not all can afford a pelleting machine, especially home mixers. Some feeds benefit from being pelleted. Such is the case of piglet and broiler feeds that may improve feed efficiency by up to 15% when pelleted correctly. But, again, to make a difference in the market we often make pellets super thin or extra hard, something that is not necessarily needed by the animals. A qualified nutritionist with knowledge on applied animal nutrition can distinguish between marketing and animal benefits and discuss this issue with management and clients. In other cases, feeds are erroneously being pelleted and animals can do equally well with meal-type feeds, if ground at the proper particle size.
- Grind size. The finer the grind size, the better the feed efficiency, but the more electricity it takes to reduce particle size. But, only certain species benefit from a finer particle size, as for other species the opposite is true. This is the case of pigs versus poultry. However, a coarse grind makes for a more friable pellet, which is not always detrimental to animal performance. In contrast, animals prefer soft pellets, but such is not the case from a marketing point of view as pellet fines/dust have received a very bad reputation due to erroneously interpreted research. In addition, in certain cases, poultry producers ought to reconsider whole-wheat feeding, whereas powder-style piglet feeds ought to be replaced by more practical feeds by adding different ingredients (molasses, for example) that can offer similar results.
- Mixing time. Mixers are needed to bring all ingredients together into what we call a complete feed, concentrate, or premix. How long we run a mixer to achieve a uniform distribution of all ingredients is highly variable and depends mainly – but not only – on particle size uniformity. Grinding cereals close to the particle size of soybean or rapeseed meal will ensure a more rapid mixing time. Research has shown that overmixing can cause some ingredients to unmix, whereas complete distribution is not essential to all species and all ages.
- Ingredients. A formula can be very simple or very complicated, but the number of ingredients being used does not have to be immense. For example, a least-cost feed formulation software may pull in 3% wheat in a corn-soy-based complete feed, just only because wheat is available. But, running the auger for 3% wheat only increases energy consumption. In such a case, the nutritionist ought to intervene and force wheat out manually. Feed cost will increase slightly, but this can be balanced out easily if electricity is now 10 times higher than during normal times.
- Additives. Again, some additives are needed and indeed can help increase feed efficiency, gut health, and a host of other benefits. Some others are just for a smoke screen against competition, marketing or just because they were there when the new nutritionist took over. The fewer additives we use, the less time/labor/energy we will have to spend at the feed mill, thus reducing the final cost of the feed. Given the tremendous amount of marketing research and advertisement additives have received during the past 30 years, I can understand why some nutritionists may not want to be responsible for this exercise, but in my experience at least half of existing additives can be removed with impunity. The secret is which ones, of course.
- Number of feeds. This is a far more complicated procedure. It requires the cooperation and understanding of the animal farm for which feed is made. In most cases, it is only possible when feed is made internally and not bought from a local feed mill. It implies reducing the number of feeds being fed per animal phase. For example, in broilers we feed three feeds as per tradition. But, that was the case also 20 years ago when broilers were marketed at 56 days. When broilers are marketed at 35 days now, I question seriously the need for three feeds. The same is true for piglet feeds post-weaning. Do we still need six or seven feeds, or would two, or even one for small farms, can be equally profitable? Here, experience and a case-by-case testing is required to find the optimal solution.
In brief, there are many ways to reduce electricity consumption at the feed mill, but there might be some negative reactions from marketing and even from animals. So, here is where the nutritionist can help close the gap by deciding how far one can go with each measure, taking into account the tremendous cost of electricity, which is unlikely to go down anytime soon. And as always, desperate times call for desperate measures.