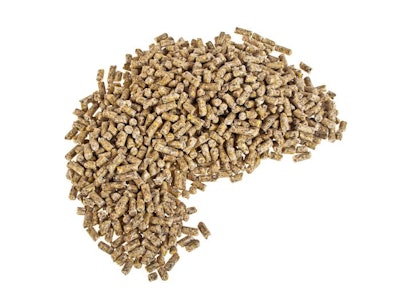
Taking a meal feed formula to pellet takes some formulation revision, good machinery and even better operators.
Taking any feed formula initially designed to be fed in meal form through the pelleting machine usually ends up in failure.
If the pellets come out, they are either too hard or too soft. If they are too hard, some animals might find them difficult to chew. If they are too soft, fines become a problem at the feeder. In either case, feed intake and/or feed conversion rate suffer and profitability decreases.
So, when we review a meal feed formula in order to pellet it, or when we build from scratch a new one for pelleting, the following list has been useful to my consulting business.
-
Milk products
If the feed already contains any milk products, pelleting will be difficult. This has to do with the presence of milk protein that hardens the conditioned mass, ending in a bullet-strong pellet. Whey protein concentrate should never be included in formulas that are to be pelleted, unless it is used at low levels as a pelleting aid – negating the use of other agents that help create stronger pellets.
-
Feed-grade amino acids and reducing sugars
The Maillard reaction begins as soon a reducing sugar (for example glucose from sucrose or lactose hydrolyzed during conditioning) with a free amino acid. This process renders the amino acid (and the sugar) unavailable to the animal (but available to the gut microbes) and thus reduces useful nutrients for the animal.
When gone too far, the pellets come out looking scorched, but the Maillard reaction begins – and nutrients become unavailable – even before coloration occurs. Some “browning” is unavoidable and might even be beneficial, but overcooking should be avoided when ingredients that promote the Maillard reaction are used heavily in pelleted feed formulas.
-
Heat-sensitive additives
There is a range of heat-sensitive ingredients that should never be pelleted. These include but are not limited to phytases, lactic acid-producing probiotics and some vitamins. Heat-stable alternatives exist, and these should be used instead.
Or, one may increase the inclusion level of heat-labile ingredients while reducing pelleting temperature, but this is an expensive and always successful solution. On the other hand, heat-stable ingredients tend to be more expensive. Thus, it might be better to use a different source for an additive or nutrient, if available.
-
Flow and anti-caking agents
Fine grinding of corn and wheat results in feeds that flow with difficulty, especially when handled in bulk at the farm level. Sticky ingredients like milk products, glucose, and fats/oils tend to cause the feed to cake, either inside the farm bin or even inside the bags. For this reason, we add flowing and/or anti-caking agents that help solve either or both problems.
When pelleting such feed formula, these agents might not be needed, unless the feed mill has similar problems transposing the mixed feed from one piece of machinery to the other. If not, then some considerable savings can be obtained by removing these agents.
-
Pelleting agents
Some feeds do not pellet well (soft and friable pellets). For this, we can add a specific additive called a pelleting aid. Some ingredients such as wheat and whey protein concentrate (harden pellets), oils and molasses (makes feed pass with less friction through the dies), fiber sources (at the right levels provide rigidity to the pellet) can also be used instead of chemical agents.
-
Uniform particle size
Feeds with non-uniform particle size are more difficult to pellet, especially as pellet size (diameter) is reduced. Any large particle is liable to cause a break in the pellet structure upon applying the least amount of pressure during handling. This can cause an excessive amount of fines, which may be detrimental to animal feed intake. In some mills, the whole mixed formula is ground together to a minimum particle size to ensure pellet durability.
7. Liquids
The amount of oil/fat and molasses that can be absorbed in a meal versus a pelleted feed is slightly different. Some feed mills have the ability to apply part of the liquids post-pelleting but this increases production cost. On the other hand, liquids in pellets do not leak so easily when placed in bags without a plastic lining.
8. Cereals and pellet durability
Finely ground corn produces a satisfactory pellet, but normally ground corn (around 600-800 microns) combined with coarsely ground (normal) soybean meal (above 900 microns) produces a rather poor (soft) pellet. This is often deemed undesirable, especially for commercial feeds (although some animals may not mind, or even prefer these poor pellets.) On the other hand, wheat is known to produce hard pellets, due to its concentration of gluten.
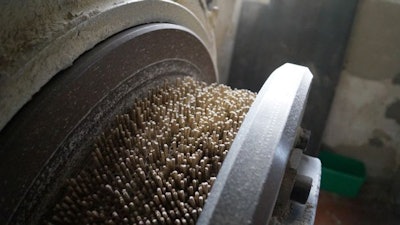
Of course, all of the above can vary considerably due to different machines being used to condition and pellet the feeds. Modern machinery is supposed to make pelleting of difficult formulas easier, but it tends to be more sophisticated and expensive.
A knowledgeable pellet operator can help a nutritionist with limited experience on the above issues (lamentably not many universities, such as Kansas State University, offer such courses). Also, an experienced old hand knowing the feed plant’s machinery can pellet almost any feed formula – at least according to my experience, but such people-assets are hard to come by.
Pelleting is not as easy as it sounds. It takes some formulation revision, good machinery and even better operators. And then, not all feeds can produce good quality pellets.
How does pelleting affect specific feed additives?: https://bit.ly/3vdr5E3