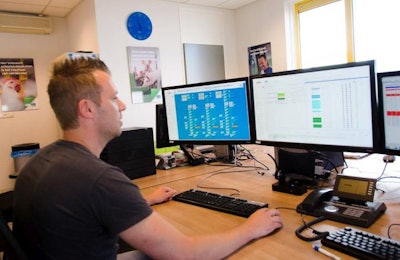
Dutch poultry and pig feed manufacturer Coppens Diervoeding recently celebrated its 90th anniversary. During this time, the company has seen a lot of changes – for one, its recent growth. In the past year, the company grew by 15 percent. As more orders came in, the company began running more batches per hour and quickly realized it needed to find better ways to handle the increased volume.
Michiel Wasmus | Coppens Diervoeding feed mill
Growing pains
Scheduling and delivery was one area of the company that needed to be brought up to speed in order to keep up with added production.
When a client orders animal feed at Coppens Diervoeding, their order is entered into the transport schedule. Client orders have to be delivered on time; however, it can be difficult to predict at what time the order is ready and can be sent out for delivery.
Until recently, the exact delivery time of the product was hard to predict, while the buyer wanted to know at what time he could expect to see the bulk truck arrive at his farm. Due to Coppens' growth, the need for an insight into the schedule increased.
Michiel Wasmus | Bulk outloading system at the Coppens Diervoeding feed mill
Coppens Diervoeding sought out a solution to this problem. The company chose to implement the new Production Insight modules of PROMAS ST, KSE’s feed mill process control system.The module makes it possible to predict exactly at what time a client order is finished.
Coppens manager Bob Pritchard explains the old setup: "Until recently, there was no link between the logistics and production schedules. There was a lot of calling going on between the two departments. And if there was an urgent job, we had little insight into how it would affect the rest of our schedule.The schedule was inside the heads of the schedulers, but not in a system.”
In contrast, using the new module, Coppens employees can see how a particular batch will affect the rest of the production process.
Tessa Nederhoff | Coppens Diervoeding scheduler operates the Production Insight module.
Rush jobs "create a lot less unrest now,” explains Pritchard.“Also, we have a better insight into what is scheduled on the production lines and where there are gaps. Those gaps can be filled with stock production,which makes the production process a lot more efficient. The difference in efficiency between a good and a bad schedule can be as much as 20 percent. Production Insight reduces that difference considerably."
System makes growth easier
In 2015, Coppens installed a fourth pressing line, by upgrading the grinding/mixing line with a new hammer mill and an additional roller mill. As a result, production has risen from 35 to 50 tons per hour, making it possible to produce more on-site.
Coppens Diervoeding aims to realize a production of 350,000 tons per year.
"The production and logistics department are not constantly on the phone anymore, I have to use a lot less screens now, I have a better idea of what goes on, and I work less overtime,” explains Sjef Lemmens, Coppens scheduler. “In the schedule, I drag client orders from the grinding/mixing line.The program's interface gives you a graphic overview of the production progress of a certain order, which part is already in stock and which part still has to be produced, what time the order will be completed, and if the transport schedule corresponds with the production schedule."
The system has also reduced the number of mouse clicks to access the information from 21 to three, a requirement of Coppens that has been incorporated in the module.
"We developed the module together with clients," explains KSE’s Erik Tenbült. "During the development stages, we and our clients looked at how we can change and improve things. Clients were able to provide feedback about the beta version. We want to continue working like this. By working together, our products are more in line with the clients' wishes and are supported more by the clients."
Future upgrades
The program is set to undergo several other developments, such as the ability to provide insight into the bins where the finished product ends up.
"The module shows which products belong together so they can be scheduled on a single out loading line," says Tenbült. “In addition, the interface will be optimized, giving a better idea of stocks. Also, KSE wants to be able to schedule maintenance stops, so that they can also be taken into account in the schedule.”
This is vital, as Coppens uses two out loading lines. Insight into the final cells enables the scheduler to load one order in one loading line, while the bulk operator knows when the preloading bin can be loaded.
At the end of this year, Coppens hopes to be able to make the next step,when the fourth pressing line should be ready and production levels can rise.
About Production Insight
Feed mill planning system Production Insight provides detailed, real-time insight into the expected end time for production and occupation of feed production lines.
KSE | Production Insight interface
For example, it displays when customer orders are ready, the raw material stock is topped up, or when a truck can be loaded. It makes optimum use of available silos and allows logistics planning to be seamlessly integrated without intensive discussion.