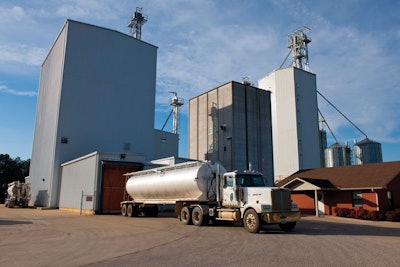
Expert shares his tips for reducing pathogens and improving products
The keys to good feed mill biosecurity are keeping things dry, restricting movement and eliminating dust, according to Richard Obermeyer, director of feed production for Aviagen North America.
He spoke January 28 during the American Feed Industry Association’s Feed Production Education Program held as part of the 2021 Virtual International Production & Processing Expo.
“It’s always about controlling what you can control,” he said. “These are things you can control.”
And, he added, continually improving your biosecurity program will continually reduce pathogen risk, improving the product you deliver.
Obermeyer said there are three main areas where the risk of pathogens can be reduced: water, all other vectors, and cleaning and disinfection.
Water
The facility must be kept dry, and standing water should not occur.
“Standing water: absolutely a no-no around any facility. These are literally bacterial reservoirs. They’re major vectors for both viruses and Salmonella,” he said.
If there is standing water, vehicles drive through it, people walk through it, and birds and animals drink from it, and then viruses spread.
“This is one of the things you just have to do if you want to run a biosecure facility, is you have to get rid of any possible water spots or standing water. It’s just a must,” Obermeyer said.
Vehicle disinfecting stations are useful if they’re done properly, he said, but water shouldn’t be allowed to collect around them. Disinfectants dissipate within two to three hours, so with inadequate drainage, you just have another bacterial reservoir.
“If these are done properly, there’s adequate drainage and there’s no standing water and things are done exactly right, they’re useful, but the last thing you want to do is make the problem worse,” he said, adding that any disinfection method should be validated with sampling that confirms it works.
Next, the receiving area and pit must be kept dry at all times. Nothing should be able to drop from the vehicle into the pit. Obermeyer said the pit should be small enough to fit between a truck’s wheels, and a funnel should be used during unloading to minimize spillage.
“If you spill product on both sides of the pit and you’ve got wheel paths on those sides and you sweep that product back into the pit, you’ve just swept the wheel path and all that debris into your pit, so you’ve just contaminated your product flow,” he said.
Finally, check to make sure processing and storage areas are designed to keep rain and moisture from entering the material handling and storage equipment.
Other vectors
Organic materials, dust, rodents, wild birds, and vehicle and foot traffic are all vectors for bacteria and virus spread.
“Salmonella loves dust,” Obermeyer said, because it provides food and an effective means for movement.
Rodents, insects and birds take advantage of organic material provided by feed mills.
“They are hosts. They are going to ingest these bacteria and these viruses and then they’re going to spread them all over the place,” he said. “Once they take up residence … it’s nearly impossible to get completely rid of them. So, the issue is never to allow them to get there to begin with.”
Vehicle traffic and people movement can also spread pathogens, so it is especially important to separate raw material receiving traffic from all other facility traffic to reduce contamination risk. The facility should display signs and use gates, locked doors and fencing to indicate where raw materials should go.
“The key is keeping the raw material delivery drivers from wandering around the facility,” Obermeyer said. This includes providing them a separate waiting area and restrooms.
Cleaning and disinfecting
The first step to cleaning any area of the feed mill is to remove all clutter.
Second, remove large debris and dust. Obermeyer said this has to be done by hand with brushes, scrapers, shovels and brooms.
“We don’t want to use (compressed) air, we don’t want water, so this has to be done the old-fashioned way,” he said. “The more often you do it, the less there is to clean.”
Third, entire area needs to be vacuumed to remove the dust particles you can’t see.
Once everything is clean and dry, it’s ready to be disinfected. Disinfectant must contact all surfaces, otherwise it’s not effective. Obermeyer said fumigation is probably the best method, but it requires specialized chemicals and training.
Finally, he said, a kill step is necessary.
“A true biosecurity plan really requires a kill step. You have to have some point in your facility where you are knowingly eliminating all pathogens in your feed before you ship it out,” he said.