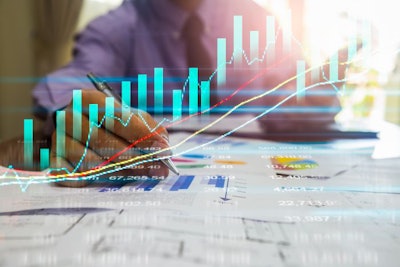
Evaluate how your company can leverage the internet of things (IoT) and data for better decision making in feed production
While the use of the term “Industry 4.0” has become commonplace, it is not always obvious what it means in animal feed production. During his “Industry 4.0 and Smart Data Analytics” TECHTalk in the 2021 IPPE Marketplace, Pete Ensch, president and CEO of WEM Automation, outlined how Industry 4.0 and the internet of things (IoT) can be implemented in animal feed production for maximum returns.
“Imagine your feed mill as an interconnected smart factory, where all of your processes are connected from receiving through batching, pelleting and load out — and even all the way to the delivery of the feed to its final destination, the farm,” Ensch said. “Data from each process, coming back to a central location where operators and management can quickly see what is going on so that they can make database decisions that will directly impact safety, quality, delivery and cost (SQCD).”
Currently, Industry 4.0 in the feed mill involves the use of inexpensive sensors, computers and data storage, combined with advancements in the network to capture real-time data from the “cyber physical system,” he said, but that utilizes various technologies at all levels of the plant, and integrates the systems into its production plant controls, creating a smarter factory, which seamlessly interconnects the mechanical with humans, as part of a continuous improvement philosophy.
IoT is the combination of several cyber-physical systems, communicating with each other autonomously, generating an increased amount of data and using that data to improve “Operational Excellence” business strategy, which is usually measured by improvements to SQCD.
“Continuous improvement is all about using data to drive decisions,” Ensch said. “IoT does not create value. … Industry 4.0 is about making pertinent data available across the entire facility, but data or information is only part of the story. The data needs to drive action, action that directly impacts SQCD.”
He went on to explore the different implementation cyber-physical systems throughout animal feed production, including traceability and improvements to feed safety by eliminating human error.
6-step process to implement IoT at the feed mill
As Ensch explained it, IoT is about creating an internet within your factory to connect all processes. While the implementation may be a departure for how production has always operated, he proposed a high-level, six-step process for companies planning to introduce Industry 4.0 to their feed operations.
- Develop a plan
Identify clearly defined goals and make sure the entire organization understands the problem(s) you are trying to solve and/or which metrics you are trying to improve.
“It is extremely easy to generate gigabytes of data using IoT,” Ensch said. “The challenge is knowing what decisions you want to make with the data upfront.” - Select the right team
Assemble a multi-discipline team from across the business that includes process experts from operations to quality and finance. For example, Ensch said, use a project manager who has a track record of introducing new technology and managing change with people. - Be honest about the people side of change
Change management is equally important and even more challenging than the technology itself, he said. - Select the best technology for your business
Ensch stress that companies do not have to make every change all at once, and suggested companies “look for technology that can easily install on top of what you have, prove that you can do it, and then scale up from there.” - Deployment and implementation
He suggested companies make sure the initial scope of program is realistic in size and timing.
“Implementing a solution and proving to the team and management it can be done will build confidence over time by using continuous improvement techniques to measure your results and make incremental improvements,” he said. - Execution
“Execution is about three things: follow up, follow up and more follow up,” Ensch said, noting this ensures the technology and people are working as the plan intended.
“It takes weeks to create good habits and to fully understand the data being produced,” he said. “Build time and hard schedule follow up points in your action plan to verify the new process and technology are working.”
Read more from IPPE 2021 Marketplace.