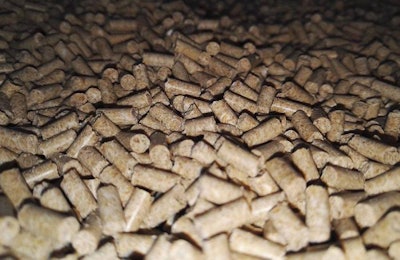
Power consumption is a key parameter when monitoring feed mill performance. Up to 60 percent of electricity is used for pelletizing. By working at maximum capabilities and reducing the friction between the mash particles and the die walls, the mechanical energy needed is reduced and the energy consumption diminished. This is even more true when dealing with high production volumes.
Pelletizing and friction
Pellets are formed by extruding mash through the die holes. It is generally accepted that increased friction has a detrimental effect on energy efficiency and production rates. This force depends on the coefficient of friction between the mash and the die walls.
Among other parameters, the diet ingredient composition is considered highly influential on the amount of friction. For example, while added fats or moisture lubricate the mash-die interface and reduce power consumption, the addition of minerals may increase friction and limit the cohesion and compression capacity of the feed, resulting in reduced production efficacy. Similarly, it is believed that the physical form (powder or liquid) of some additives, like methionine, may influence the energy consumption. Trials were performed to explore this potential effect in formulations with or without added water and/or oil.
Methionine source can bring unexpected benefits
The effect of the methionine sources on energy consumption was evaluated using a Kahl flat-die pilot pellet mill. The same diet was used throughout the study. Powder (D,L-Met) and liquid methionine (DL-2-hydroxy-4-(methylthio)-butanoic acid or D,L-HMTBA) were used as the methionine sources.
To compare the formulations, the specific energy consumption (SEC) (kWh/t) was calculated by measuring the instantaneous power absorbed (kW) by the motor of the press each second then dividing it by the real output rate (t/h) when all the process parameters were stable.
In Figure 1, the effect of the use of powder or liquid methionine on SEC is observed. Overall, a significant increase in energy consumption was measured compared with the positive control and to liquid methionine when powder methionine was used. The addition of oil alone flattened these differences, leaving only tendency for lower power usage in favor of liquid methionine. The savings ranged from 2.5 percent when the feed was dry to 4.4 percent when the feed contained additional free oil and water.
The differences were less evident when adding water alone. However, lower consumption trends were observed whenever liquid methionine was used compared with formulations with powder methionine.
The trials were repeated with oil alone, and different levels of liquid methionine were used (Figure 2). Implementing typical doses (0.23 percent) showed savings of up to 7 percent when no oil was added. The addition of oil reduced the overall energy consumption. When 3 percent was added, the savings when using liquid methionine instead of powder methionine equaled 4 percent. No significant differences were observed when small amounts of oil were added.
Overdosing the liquid methionine to 0.67 percent diminished the power consumption in all cases.
The general mechanisms that cause these energy differences are still unknown. However, it is possible that the powder methionine effect originates from an increase in the frictional force as it represents the major mechanical power drain in the pellet mill. The apparent balancing effect of added water leads us to believe that the phenomenon may be caused by hydrophilic particle interactions between the die walls and among themselves. Because liquid methionine is a water-soluble liquid, these interactions may not take place, which could justify the power savings observed. This is a common trend overall but tends to vary.
Indeed, one must be aware that the coefficient of friction, which affects energy usage, is affected by an important number of parameters, namely the mash’s physical-chemical composition, the conditioner residence time, the moisture content, the mash’s compressibility, the die parameters, the die temperature, the die-to-roller gap, and the machinery’s wear state. Even though stable numbers are difficult to obtain, the trials showed that the use of liquid methionine could be a means to reduce the power consumption of pellet formulations without moisture addition.
Additionally, a Eurotest Sabe and a Schleuniger machine were used to test pellet quality as it affects energy consumption. Regardless of the formulation, pellet quality was maintained. A durability of 91 percent, 104 ± 0.8%, and a hardness of 34 N/pellet, ± 3.3 N/pellet, for the feed without oil was obtained. The addition of oil resulted in 84.5%, ± 0.7%, and 23.5 N/pellet, ± 1.4 N/pellet, for durability and hardness respectively.
Benefits for the feed miller
These potential energy savings may be reflected in feed production costs. For example, if a 20-ton/hour pellet press absorbs 250 kW with a SEC 12.5 kWh/ton runs in plant producing 100,000 tons annually, the use of liquid methionine could result in $4,000 to $12,000 in savings each year. This, with prices provided by the International Energy Agency, equals 1 kWh = $0.13.
To correctly apply and realize all the benefits of liquid methionine, properly designed and calibrated installations, good practices for liquid application and proper monitoring are key.
References available upon request.