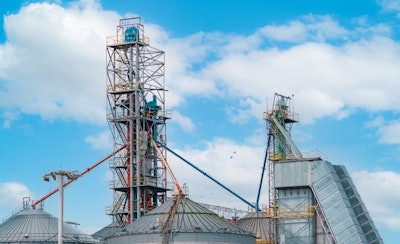
Gary Huddleston, director of feed manufacturing and regulatory affairs at the American Feed Industry Association, discusses the regulatory issues he’s watching for 2023 and how they might affect the feed industry.
PODCAST: What to expect in the feed regulatory space in 2023 (14:04)
Ann Reus: Hello and welcome to the Feed Strategy podcast. I’m your host, Feed Strategy senior reporter Ann Reus.
Gary Huddleston is director of feed manufacturing and regulatory affairs at the American Feed Industry Association, or AFIA. I recently spoke with him about the regulatory issues he’s watching for 2023 and how they might affect the feed industry.
Hi Gary, thanks for joining me today.
Gary Huddleston: It’s good to be here. Good to be with you, Ann.
Reus: What are you watching in the regulatory space for 2023 that will affect the animal feed industry, and how do you think the outcome of the midterm elections will affect these topics?
Huddleston: Well, I don’t see the midterm election results having any real effect on the issues that we’re watching in the regulatory space for our feed industry partners, but we do continue to keep our eye on FSMA (Food Safety Modernization Act) inspections at our facilities and to try to keep a good understanding of FDA’s (U.S. Food and Drug Administration) expectations around animal food safety.
We’re watching several issues with the EPA (Environmental Protection Agency) including formaldehyde and PFAS (per- and polyfluoroalkyl substances) chemicals and urging the agency to follow good science when they’re thinking through setting any limits that could eventually affect future regulations.
We would love to see the Federal Motor Carrier Safety Administration continue to explore ideas and options to encourage folks to explore opportunities for employing those truck drivers. We’ve got an extreme shortage of truck drivers in our industry, and we would love to see them do things to encourage more folks getting into that industry, especially in that 18- to 21-year-old age bracket. A lot of young folks are graduating high school and looking to be a truck driver, but in most states, they can’t get their CDL (commercial drivers license) and travel, do deliveries interstate unless they’re 21 years old, and so we lose a lot of those young drivers because of that age bracket, that skip in time before they can actually get a CDL.
With OSHA (Occupational Safety and Health Administration), were watching several priorities, including a potential infectious disease standard. Their work on the forthcoming heat illness and injury standard, as well as their new proposed rule to require certain employers to electronically submit more injury and illness data than they already are to OSHA. So those are just some of the things that we’re kind of keeping an eye on within my job description, things that I look at.
Reus: And you mentioned some of those topics at the Liquid Feed Symposium in September in New Orleans. And I wanted to talk a little bit more about those. There, you said that feed mills should have a pandemic plan. What should be covered in that plan, and can you describe the actions and procedures that should be written out?
Huddleston: Yeah, I would encourage any employers to think through what they did in response to the COVID-19 pandemic. Think through what worked well, what didn’t work so well, what you’ve already got in place as a written program. If you don’t have a written program around infectious disease and preparedness, you should definitely do so. Whether we have a standard coming down the pike or not, it’s just a good business plan to have those things written out. And what would you do differently if something like this happens again? We’ve got an opportunity to sit down and think about how we responded over the last couple of years. Basic elements of a good written infectious disease preparedness and response plan are things like, what would trigger the implementation of this plan? Some of the things that you’re going to have written out as far as your company or facility response practices and procedures that you might put in place to mitigate the risk of your employee exposure, things like social distancing, personal protective equipment, cleaning and additional cleaning, personal hygiene, stuff like that. How am I going to communicate with my employees? How are we going to communicate potential changes in our operational schedule as the result of this, what’s going on? What kind of training that we would need to provide our employees for any kind of new workplace environment or requirements that you might have to put in place in response to a pandemic. You need to think through what kind of recordkeeping that you’re going to do and then how you’re going to keep up with that as far as records that you would need within your own business as well as required records from OSHA. You may probably need to think through a company vaccination policy if applicable. We’ve seen this administration tried to go with a requirement for COVID-19 vaccinations. It didn’t make it all the way through the Supreme Court, but your company probably needs to think through what’s going to be our policy around that. And any other kind of relevant policies and procedures that would affect doing business in this kind of environment, such as your sick leave policy and things like that. But I highly recommend developing a thorough written plan, but then leave enough flexibility in that plan to respond as appropriate.
Reus: You mentioned the potential heat illness prevention standard that the Occupational Safety and Health Administration, or OSHA, may be working on. Can you give some background on that and what you would like to see included in that standard?
Huddleston: Yeah, if I had my way, I’d rather not even see a heat illness or injury standard. We don’t look for additional standards in our industry to comply with, but it does seem like the agency is headed in that direction. Last April, in April 2022, OSHA launched a National Emphasis Program to protect workers from heat illness and injuries. A part of this program was a lot more targeted inspections that OSHA was doing, was going to do, and what they determined as high-risk industries. I haven’t seen a large uptick in citations issued as a result of this National Emphasis Program, though. If we do see a standard in this area on heat illness and injury, AFIA is going to watch it and we want to make sure that it doesn’t include any overly burdensome requirements for our manufacturers to deal with.
Reus: What can feed mills do now to prepare for a standard like this, and just to ensure the safety of their employees when it comes to the heat?
Huddleston: Well, most big mills probably already have a written policy around heat illness and injury. And if you don’t, I highly recommend you go ahead and do. That’s going to be one of the first requirements that we would see out of a standard is that you have a written policy, and a written programming around these types of injuries and illnesses. The basic elements of that program is going to be employee and supervisor training on recognizing the symptoms of heat illness, and then training your employees on how to protect themselves from heat injury and illness and climatization of new employees, especially if you hire employees in the hotter months, they may not be used to working in a in a non-air conditioned, climate-controlled environment. So you may have to do some acclimatation procedures for those new employees. Policies covering breaks and availability of hydration, you may need to consider that, and then are there going to be changes to those breaks as the temperature changes. And you need to think about temperature triggers that could initiate changes in your work schedule, you may have at certain temperature triggers, you may temporarily change your work schedule to put in more breaks. Even things like alternative clothing for the hotter months. A lot of employers will look at allowing T-shirts and shorts and things that are a little more comfortable to work in, if that type of uniform or clothing doesn’t put pose any additional dangers to the employees. But with any safety-related programs, the purpose is to think through the hazards of the mitigation, think through those hazards and any kind of mitigation steps for those hazards, and then document effective policies and procedures to protect your employees. Training, training, training. Training is going to be the heart of any kind of heat illness and injury written program because symptom awareness is probably your most important mitigation strategy and making sure supervisors as well as all your employees understand what those symptoms are, and look out for each other in the workplace.
Reus: You also brought up a potential emergency response preparedness rule update. What might you expect to see there and what types of situations would that cover?
Huddleston: Well, this potential updates of the emergency response and preparedness rule has been on OSHA’s regulatory calendar for a while now. It mainly applies to the emergency responder community, not necessarily industry. OSHA currently regulates certain aspects of emergency response and preparedness. Some of these standards were promulgated decades ago and none of them were really designed as a as a comprehensive emergency response standard. And so, we may see OSHA bringing all that together under one comprehensive standard. Maybe they won’t, but that’s one possibility.
Consequently, they don’t really address the full range of hazards or concerns facing these emergency responders or workers that provide that skilled support during emergencies, nor do they reflect major changes in performance specifications for clothing and equipment that we’ve seen develop over the last few years. And so, it’s mainly going to be an updating of this kind of information, updating and taking into account all the recent developments in safety and health practices that’s been developed by the emergency response community over the last few years. And, and so we may just see all that come together in a more comprehensive standard.
And it’s probably needed to give to better protect their emergency responders. We don’t really think it will affect general industry that much, but we will make sure and monitor it to see if there’s any kind of new requirements that might be placed on facilities that they may have to include in their facility emergency response plans.
Reus: You often provide updates to the industry on FSMA inspection numbers and how they’re going. Are you still seeing feed mills getting advanced notice of inspections like they were during the height of the pandemic and are they still keeping the same pace of inspections these days?
Huddleston: That’s a good question. They have begun to ramp it up their inspections now and then getting out to see more facilities. So far, we are seeing most all these inspections are being announced, just a few days ahead of time. I had a recent committee meeting with my production and compliance committee and that’s one of the things that we talk about is inspectional activity and all the folks in the room that have had recent inspections said they were all announced beforehand, but they’re just giving it a day or two notice. And I think FDA has kind of realized that, for an effective inspection, making sure the right folks are at the plant – because we operate our feed manufacturing facilities with a pretty skeleton crew a lot of times, it is the small number of employees compared to other industries – and if the right employees are not at the facility, it makes a big difference on how that inspection goes. And so, FDA is beginning to realize, ‘If we’re going to drive a long way and send inspectors out to go to these facilities, it behoove us to make sure the right people are going to be there.’ And so hopefully that that practice will continue. But so far, it seems to be.
Reus: Yeah, make it easier for everyone all around. Well, did you have anything else that you wanted to update our listeners on?
Huddleston: Just encourage any listeners, we’ll do a little more comprehensive update on regulatory for feed manufacturers at IPPE (the International Production & Processing Expo). We’ve got a regulatory program that we do every year on the Wednesday of IPPE week. It’ll start at eight o’clock and be two hours and we’ll cover all the agencies and so if you’ve got folks that are going to be at IPPE in Atlanta in January, make sure to show up at our regulatory feed manufacturing education program. It’s free, and so it’s a good opportunity to get the latest updates on what all of our agencies are doing and what they mean for our industry.
Reus: Okay, great. Well, thanks Gary. I will see you at IPPE as well as any of our listeners who are planning to attend.
Huddleston: Thanks a lot, Ann.
Reus: You can find out more about the International Production & Processing Expo at ippexpo.org. It will be held at the Georgia World Congress Center in Atlanta on January 24 through 26, 2023.
I’d like to thank the listeners for tuning in. I’m Ann Reus for Feed Strategy.