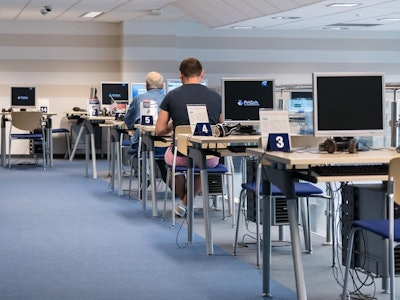
The U.S. feed manufacturing industry is no stranger to challenges, from labor shortages to evolving technologies, but Dr. Ryan Walker, entrepreneur and associate professor, Mississippi State University, said artificial intelligence (AI) promises to transform many present-day challenges into minor barriers in the future.
Walker delivered an engaging presentation on innovative ideas for the future of workforce development in the feed manufacturing industry at the American Feed Industry Association (AFIA)’s 2024 Equipment Manufacturers Conference (EMC) in Bonita Springs, Florida. His key message: Industry and education must work together to address skills gaps, embrace AI and prepare a future-ready workforce.
Rethinking higher education with micro-credentials
Walker’s presentation acknowledged the limitations of traditional degree programs in meeting modern workforce needs. He said institutions of higher learning (IHLs) often struggle to adapt quickly to industry demands, leaving graduates underprepared for challenges.Dr. Ryan Walker, associate professor, Mississippi State UniversityCourtesy Mississippi State University
“We have a shortage of engineers, and industry is struggling to find qualified people,” Walker said. “But universities are like container ships — they don’t pivot easily. Some degree programs haven’t changed since the 1970s.”
Mississippi State University's College of Professional and Continuing Studies, where Walker is a tenured associate professor, is challenging this paradigm to overcome problems in the traditional education-to-workforce pipeline, and has pioneered a new model focused on micro-credentials — short, targeted training clusters that integrate seamlessly into any career path.
“They’re designed to prepare graduates for sustainable, well-paying jobs,” Walker said. “Think about it like this: You can take two courses and walk away with a certificate in applied AI. It’s not about re-enrolling in a rigid degree plan anymore.”
The program was strategically designed to change the perception of alumni. Walker said he wants graduates from Mississippi State University to become lifelong learners, with the ability to come and leave for micro-credential courses as they please.
Walker highlighted the potential of micro-credentials to bridge skill gaps, enhance productivity and address the evolving needs of modern industries. For feed manufacturers, this approach could be revolutionary — allowing employees to upskill in emerging areas such as generative AI, predictive analytics or virtual reality (VR) applications without committing to years-long degree programs. Walker said such credentials could even be tailored for industry-specific needs, such as using AI to improve feed quality or VR to train technicians on new equipment.
AI in feed milling operations
AI’s potential to streamline processes and boost productivity is immense. Walker described how AI is already reshaping the feed manufacturing industry, particularly through predictive maintenance using real-time sensor data analysis.
“Anyone who uses sensors in their mills is already using machine learning,” Walker said. “Your sensors flag issues before they become problems.”
In feed mills, temperature and moisture sensors can predict equipment failures and optimize production conditions. These technologies reduce downtime, ensure consistent product quality and make operations more efficient.
Extending beyond operational use cases for AI, Walker pointed to generative AI tools, such as ChatGPT, as valuable office tools for feed manufacturers. From automating routine tasks like drafting reports to analyzing purchasing trends, AI can empower office staff to focus on strategic decisions.
For example, using AI in Excel can automate revenue projections or analyze purchasing patterns, saving time and improving accuracy.
In an industry reliant on precision and safety, VR training could also become a game changer. Walker pointed to examples from sectors like the automobile with BMW’s VR headset training for technicians, describing how feed manufacturers could adopt similar strategies.
“If you’re building a new feed mill, why not use VR to train your team?” Walker said. “It’s safer, faster and cheaper.”
Easing workforce transition challenges
One of the most pressing issues in the feed industry is the retirement of experienced workers. With decades of expertise leaving the workforce, it faces a skills gap that AI and training can bridge.
“We’re under pressure to do more with less, and this technology is how we’re going to get there,” Walker said.
He said AI-powered models can enable less experienced technicians to achieve results comparable to seasoned professionals. Sensors, real-time data and AI-guided adjustments reduce the dependency on decades of human experience while ensuring consistent performance.
AI for overcoming obstacles
Walker’s presentation also touched on the importance of neurodiversity in teams and shared how his personal experience sparked his enthusiasm for AI. As a self-described neurodiverse academic with dyslexia, he recounted how technology enabled his success.
“I dictated all 327 pages of my dissertation using early AI tools like speech-to-text," Walker said. "When ChatGPT hit the scene, it leveled the playing field for me. AI doesn’t just help — it transforms. Modern neuroscience shows us that diverse teams — whether that’s dyslexics, OCD thinkers or neurotypical individuals — are better at solving problems. AI is just another tool to amplify those strengths.”
By fostering inclusive workplaces and leveraging tools like AI to level the playing field, the feed manufacturing industry can tap into diverse talent pools and drive innovation.
A vision for the future
The future of feed manufacturing depends on how effectively we integrate emerging technologies, collaborate with educational institutions and adapt to workforce changes. By taking proactive steps today, the industry can ensure sustainable growth and innovation for years to come.
As industries like feed manufacturing face increasing pressures, professionals must learn to embrace technology and not fear change. Walker’s message was clear: adaptation is non-negotiable.
Referencing common misconceptions about new technology, Walker said: “Generative AI isn’t The Terminator. It’s a tool, just like a nail gun. It won’t take over your job, but it will make you more efficient.”
AI-driven training tools like VR simulations provide hands-on learning without risks or downtime, while micro-credentialing programs offer a pathway to upskill employees. Walker closed his presentation with a call to equipment manufacturers and feed millers to collaborate with educational institutions.
“Develop micro-credential programs that meet your needs,” Walker said. “Embrace AI — not just on the factory floor, but in your offices. The machine learning is already here, and together we can get better with it.”
By embracing his recommendations, the feed manufacturing industry can meet its challenges and position itself for a future of innovation and growth.