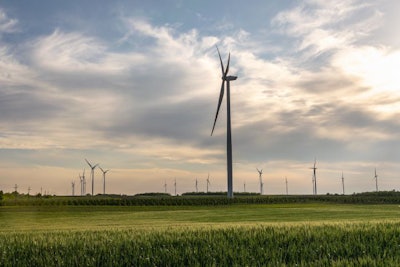
Rising costs are raising the profile of energy efficiency in feed mill design and future investments
Amid commodity and labor shortages, it can be easy to take energy for granted. But last February, massive demand for natural gas put such a strain on the system that Kent Nutrition Group was unable to maintain the gas pressure necessary to operate equipment at some of its mills.
“Honestly, we don’t put a lot of focus on energy because, yes, there are some rising costs,” but those don’t compare to recent swings in grain and labor costs, Jason Lents, senior director of operations for Kent Nutrition Group, said. But having access to reliable energy in the future, he said, is an area of concern.
Shifts in energy markets around the world have forced many industries — including feed manufacturing — to reconsider not just the amount of energy they use, but when and how they use it. With a growing number of utilities adopting steeper time-of-use rates and implementing curtailment periods, energy is an increasingly costly input to the feed milling process, according to Charles Stark, the Jim and Carol Brown professor in feed technology at Kansas State University. Fortunately, he said, several simple measures can help feed mills keep energy costs in check — and advances in technology may bring even greater benefits in the future.
“I think the industry as a whole is seriously looking at energy efficiency because of the cost,” Gary Huddleston, director of feed manufacturing and regulatory affairs for the American Feed Industry Association (AFIA), agreed. “The cost of energy is such a big part of the overall cost of feed and the manufacturing process, and the industry is forced to look at it to be competitive.”
Investing in the future
Feed mills are, generally speaking, designed to maximize energy when they’re first constructed, Huddleston said. But a lot of feed mills are between 30 to 60 years old, he said, which poses a significant challenge to the industry.
“Older facilities lend themselves to outdated systems and outdated equipment,” Huddleston said. “My gut feeling is there is quite a bit of improvement we can make in our industry, and a lot of low-hanging fruit.”
Most companies are good at upgrading their equipment when it comes time to buy a replacement, Huddleston said. Routine maintenance with an eye toward energy concerns can go a long way toward cutting energy costs.
One of the simplest and most effective exercises, he said, is for mill managers to organize a walk-through of the facility when production is down for the weekend to check for air and steam leaks.
“Back when I was a plant manager, I would walk through the facility looking and listening for steam leaks, air leaks, and documenting things about our energy bill and demand. It wasn’t something I did alone; I used the entire crew,” Huddleston said. “It’s hard to hear when you’re running at full production, but when you walk through the facility when everything is shut down, it’s amazing how many air leaks you will hear. As you repair these leaks, over time, it will save you quite a bit of money.”
Preventative maintenance like cleaning and inspecting boilers at least once per year can also go a long way toward keeping energy costs in check, Huddleston said. Other simple fixes like ensuring equipment only runs when needed can also go a long way toward reducing energy use, Stark said.
“For me, personally, energy conservation is like safety culture,” Stark said. “You have to talk about it constantly, because you have to be thinking about it. It’s as simple as, if I leave my office and the light is on, what message does that send to employees. It’s not that much money, but what’s the energy culture I’m trying to create.”
Enlisting employees in efforts to combat energy use can be especially effective, Stark said, because the people on the floor tend to have a good sense for what equipment is not running optimally.
Kent Nutrition Group, Lents said, has installed timers on equipment throughout its mills to take remove some human error from the equation and ensure equipment isn’t running all day long. Other simple upgrades such as replacing light fixtures with LEDs have further enhanced the company’s energy culture.
In some cases, Lents said, Kent Nutrition Group was able to secure grants and partner with local suppliers to reduce the cost of replacing lights and installing motion sensors. Energy providers looking to manage demand may offer programs in their area to help fund upgrades, and may even subsidize the cost of bringing in an expert for a full energy audit, Stark said.
But for the most part, Lents said, Kent Nutrition Group hasn’t been hit by rising energy costs — yet. Negotiating to buy power and natural gas via advance, bulk contracts has played a major role in maintaining predictable energy costs.
“It’s less negotiating as contracting and locking in prices at a more opportune time,” he said. “They offer contract and bid prices all throughout the year — it’s just a matter of doing a strategic job at that.”
Securing energy sources
Communicating and negotiating with energy providers may increase in importance for feed mills as the utility sector continues to adjust to shortages of its own.
Renewable energy resources such as wind and solar are significantly cheaper than conventional energy sources when the sun shines and the wind blows, leading utilities to adjust their rates with a growing number of time-of-use measures that discourage the use of electricity when these cheaper resources are not available. In some areas when the demand for heating or cooling has exceeded energy supplies, utilities have called on businesses to temporarily reduce their energy use to prevent blackouts.
“We do get energy company calls for curtailment in the summer, and as best we can we” try to accommodate that, Lents said.
While demand management is increasingly an area of emphasis for utilities, demand charges — fees that are based on the largest amount of power an energy user draws at a single point during the billing period— are nothing new. Before his time at AFIA, Huddleston said, the demand charge at the feed mill he managed could easily account for half of the monthly electric bill. Reducing production at peak operating hours could result in significant savings for the company, Huddleston said.
“We could manage our demand and save a tremendous amount of money by scheduling our various production processes throughout the day rather than coming in at 7 o’clock and firing it all up at the same time,” Huddleston said.
Managing energy demands
Installing a demand meter to assist with this process, Huddleston said, is simple, inexpensive and effective.
Similar considerations can be made when designing new feed mills, Huddleston said, by matching the designed capacity with the expected capacity and not overbuilding.
Managing demand at the mill level, he said, not only “saves a tremendous amount of money for the plant, but also helps the electric company with peak demand. If we work together, the electric company doesn’t have to spend as much money on infrastructure,” which keeps overall energy prices low in the long run.
Feed mills may even become partners in the electrical generation process in the not-too-distant future. Kent Nutrition Group, Lents said, has looked into partnering with some solar farms to potentially offset some of the company’s energy costs. It considered putting up a solar array on its property, Lents said, but investing in a larger off-site solar farm in exchange for some of the energy credits appears to have more potential.
Future research in unrelated areas such as feed formulation stand to further improve the industry’s energy efficiency, Stark said. Significant energy is dedicated to grinding and pelleting, for example, and some of that energy may be unnecessary, Stark said — research on ideal physical properties of animal feed is still ongoing.
“I think there’s money on the table,” Stark said. “I just don’t think we’ve got to the point where we know what that money is, because we haven’t looked at it.”
Announcing the Feed Mill of the Future digital supplement
WATT’s feed brands Feed Strategy and Feed & Grain magazines join forces to launch the monthly Feed Mill of the Future digital supplement. Each edition aims to provide animal feed industry stakeholders with forward-looking content, market insights and a spotlight on the leading-edge technologies shaping the global feed industry of tomorrow.
Subscribe today! https://bit.ly/3dWzow7