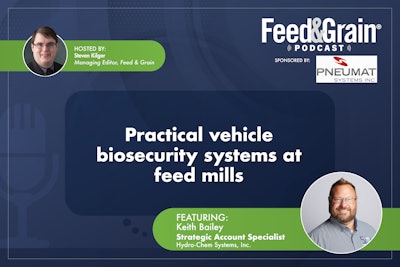
Join Steven Kilger, host of the Feed Grain Podcast, as he welcomes Keith Bailey, a veteran in automated systems design from Hydro-Chem Systems, to delve into the crucial topic of biosecurity in the feed manufacturing. Amidst rising concerns over diseases like H1N1 and avian influenza, Bailey shares his extensive experience in developing advanced biosecurity systems, including the latest innovations in truck washes and sanitation processes that help prevent disease spread in agricultural settings. Learn about the challenges and technological solutions that are shaping the future of farm and feed mill sanitation.
Podcast sponsored by Pneumat Systems.
Steven Kilger - 00:00
Hi Everyone! My name is Steven Kilger, I’m the Managing Editor for Feed & Grain Magazine and the host of the Feed Grain Podcast. Thank you so much for joining me today as we dive deep into the issues affecting the Feed Manufacturing, Grain Handling, and allied industries.
Today’s episode is brought to you by The BinWhip from Pneumat Systems. The powerful Dual Impact BinWhip removes the toughest buildup and blockages in industrial storage silos – without hazardous silo entry. Learn more today at binwhip.com
My guest today is Keith Bailey, Strategic Account Specialist at Hydro-chem Systems. With all the H1N1 news out there, Keith stopped by to talk about biosecurity systems. We discussed how these systems work, what installation and maintenance look like, and the benefits they can offer to a feed mill and its customers. I hope you enjoy the interview.
If you want to help out the podcast and are listening to this in a podcasting app, please rate us and subscribe. If you're listening online, sign up for the Feed & Grain newsletter, Industry Watch, to stay up to date with all the latest podcasts and learn about all the new news happening around the industry. Now, onto the show.
Kilger - 01:04
Hi Keith, thank you so much for joining me today. Well, for anyone who might not know who you are, can you tell me a little bit more about yourself and what you do in the industry?
Keith Bailey - 01:10
Sure, absolutely. I'm the automated sales manager for Hydro-chem Systems. I've been with Hydro-chem for a little more than 12 years now. Previous to designing truck washes, I worked as an environmental consultant for 10 years, so I did have a little bit of Industry knowledge with regulators and things like that within the environment. Since then I started here and I've pretty much been designing truck washes which are also used in the biosecurity industry. So I've designed a little more than like 200 washes and a ton of biosecurity ones.
Kilger - 01:46
Yeah well because in the US especially it's like the biosecurity part of the feed mail and stuff kind of logged behind like you'll go to some and you'll get the foot wipes and stuff like that but that's usually pretty much as far as we go I've seen a few truck wash systems out there. And what's interesting to me personally is as all this, they don't want you to call it bird flu anymore. It's something else now that it's in cattle.
But as all these kinds of diseases kind of make their way through the US and we have more and more caution about them, things like the systems that you guys make, which can be set up after it seems like a female is built and you can, so you don't necessarily have to, you know, Redesign everything for a system that's already in place but maybe hasn't concentrated so much on these biosecurity systems. Can you tell me a little bit more about the systems you design how they kind of work and what they contribute to the biosecurity of a facility?
Bailey - 02:42
Yeah, absolutely. I think a big thing is yes, we can work with a farm that's established because that's the thing that a lot of these farms have been there for a long time. There are a couple of new feed mills that are being designed and brought into the industry. And if we're brought in quickly with that, I can assist with the layout of the biosecurity setup because there's more that goes into the actual layout of the system, where it's placed on the property, where you've got clean entrances or clean exits, dirty entrances, where the green and the red zones are green being clean and red being contaminated. And we like to assume that everything coming off the road is contaminated. So there is a benefit to being on the forefront of it as it's being built.
Bailey - 03:25
However, as you said, there is a ton that is existing and these feed mills have been there for 50-plus years and we, they need a solution now. They needed one. Usually, it started in 2015 when the first outbreak of AI was. And then, uh, but now that it's kind of continuing, they've realized that yes, we still have to, to do that. So what we do is depending upon their needs, and facilities needs, some of them get what we call like full truck washes with a Sanitizing application as the vehicle is leaving the truck wash. So with that being said, the EPA method that they want people doing is a thorough undercarriage and wheel wash with high pressure, high volume water to try to remove any of the mud, things like that, that might have the virus in it. And then following that, an application of some type of sanitizer.
Bailey - 04:16
The industry standard is quaternary and that quaternary ammonia, gets applied to the vehicle until it dries, kind of like Lysol. You spray it on something, and as it dries, it kills the virus. So that's typically your application method. It isn't an instantaneous kill of the virus, but if you apply it correctly at the right concentrations, it will kill it. We've got a lot right now that we've been helping out the industry with, which are just sanitizer arches. And what that is at some facilities, they'll put one at the entrance and one at the exit of let's say a feed mill or even some large farms. And they drive in, a photo eye sees that they're coming in.
Bailey - 04:56
It turns on, it sprays the undercarriage. The wheels, the sides, the top of the vehicle, and as they then go onto the farm, it dries. They then are considered clean. As they exit the feed mill or the farm, they then get sanitized again because that commingling in the middle is always where the cross-contamination occurs. So when the virus can jump off of a vehicle, fall off in mud form, and then get slung back under another vehicle or into the tires of another vehicle and get The name of the meeting is. In that case, some of the larger farms, put in the same setup where they just drive through a sanitizer on the way in and the sanitizer on the way out to ensure that the feed truck that's going to the next farm isn't going to be sending a virus to the next farm.
Kilger - 05:57
Yeah like you said picking it up on the road only so much we can do about that and it's really about controlling like the areas where it's most likely that you could pick up something right it's more of these diseases and you know we work in this kind of global economy so you know They've been talking about the African swine fever virus for years now and it will eventually make it to the U.S. I mean it just will. It's a matter of time and the better our system can handle that kind of thing the better we all are.
So for me, it seems like a really good time to invest in something like this especially because you know you can always sell it to your customers We have a biosecurity system, which the feed mill down the road does not have. So if you're worried about any of these diseases, like where are the people to go to? But what are some of the bigger challenges that you guys are finding when implementing these things in existing properties or facilities?
Bailey - 06:52
I would say the biggest challenge is trying to create a traffic flow that we can mitigate cross-contamination so that we can try to keep dirty vehicles in dirty locations, and clean vehicles in clean locations. And when I say dirty and clean, it means that it's been through a sanitizing application and it hasn't. So if a property can, a lot of the times they have one entrance and one exit, it's the same one and you kind of come in and you leave.
If the property can be kind of redesigned a little bit, So that there is a dirty entrance and then a clean exit. It usually lends itself to the best application because then you can be assured that as soon as the vehicle didn't drive through there, there wasn't a dirty truck that drove up that road at the exact time or that entrance under the property at that same point. So really that is probably our biggest obstacle. Getting people to use it usually isn't a tough thing because to do a full-size feed truck, You're probably talking around 30 seconds, a completely sanitized one, so it doesn't slow them down to the point at which it's an obstacle, they can hit it running.
Bailey - 07:58
The bigger challenge is just trying to keep people so that they have to drive through it, whether it be pickup trucks or anything like that is coming on the property, you have to get sanitized. Usually, when it's applied correctly and the farmers use it, it works incredibly well.
Kilger - 08:16
Well, luckily it's at least something that we're familiar with, right? It's not a technology that's coming out of the blue. We've all been through car washes. I don't know exactly how that part works.
Bailey - 08:27
The only difference is, is with a carwash, you get pulled through. And with these types, those large trucks, they can't be pulled through. So they're not on conveyor systems.
So we have to rely upon the driver to kind of go the right speed. So they typically will just slow down and we'd like them going around between one foot per second and one mile per hour, which doesn't sound like a lot, but a mile per hour is about 50% faster than a foot per second. But it's still, it's so slow that it's kind of like when you're going through a carwash that speed. And that's where we try to let the guys or gals.
Bailey - 08:57
Determine, okay pretend you're going getting pulled through a car wash, and go that speed which is usually just riding the clutch or putting it in a very low gear.
Kilger - 09:04
Yeah, well it's a good reference point at least for everyone to have and also I assume makes the system a lot cheaper when you know you have someone drive through.
Bailey - 09:14
It removes a lot of the maintenance because if you talk to anybody with a car wash their biggest maintenance headache Is that conveyor system that and brushes typically and since there is no way to use brushes on feed trucks there's such an irregularly shaped vehicle that a brush just wouldn't work so all of those have to be touchlessly cleaned anyways so you remove the two biggest maintenance items. This biosecurity system then can keep running for years and years and years. Nothing is moving. Moving parts are what wears down. And since we're able to station it all in one place and let the truck move, it's got really good bearings, you know, they're designed to roll.
And let them go through it. It virtually eliminates the maintenance, which is, our biggest concern when we're selling one of these automated systems because there's one thing about if a car wash goes down and it's down for a day or two, you might have a dirty car for a couple of days.
Bailey - 10:12
If a biosecurity wash goes down for a day or two, it could be potentially millions of birds.
What kind of maintenance do these systems have? I'm guessing you have to swap out chemicals and stuff like that, refills. But what else is kind of involved with that?
There's not a whole lot. Okay. Primarily what we've tried to do with at least our basic sanitizing system, is that these are just a sanitizer arch, and with them, we've got a 110-volt booster pump.
Bailey - 10:58
We try to design it so that it can be used with any basic power. And it's a 110 booster pump. So far, knock on wood, they last close to 10 plus years and that's doing anywhere from 50 to 100 applications a day and they'll still go 10 plus years. There's very little maintenance with that and that's about it. The photo eyes, you have to clean them off, but that's, it's wiping them down. We've eliminated. So much of the maintenance and so much of the moving parts that it virtually takes care of itself.
Bailey - 11:29
The other thing that we like to do, at least with Hydro-Chem, we've devoted account managers that will stop out at their facilities every month and do 30-point inspections of the system just to make sure that if it is starting, something's starting to go, we're on it ahead of time. That's usually the easiest way to prevent it. Any downtime is to catch it before it breaks and kind of get your eyes on it, make sure that all the nozzles are open and clear, and spraying correctly. So with that being said, there's very, very little maintenance. We also eliminated all of the proprietary parts. So everything could be purchased typically at a local plumbing supply. A list of keywords relevant to topics that may occur during the meeting.
Bailey - 12:26
Are more than qualified to be able to do any of the fixes because they're some of the most ingenious people in the industry. So when they fix stuff, they always fix it, and they usually do it right the first time. So they're able to usually keep them up and running. We've never had any instances where it's been dire red flags go up and people are being sent out around the country because farmers are, they can figure it out.
Kilger - 12:49
Well that's great because you always want to do maintenance on your schedule, right? You never want to do it when a machine is broken. But if something does happen it's nice to know that you can get parts and things immediately without having to wait for stuff to be shipped to you and all that stuff.
Bailey - 13:04
Right. With the sale of anything, give a parts list, fair parts list, and say these are what we suggest you and these are the minimum quantities that you should have on hand.
Now it's not big, but it would usually just fit into a toolbox that they can have directly right at the facility to swap out any of the nozzles, any diaphragms, and things like that. They can get it back up and running immediately and then kind of have a minimum quantity in that box where when it falls below, all right, we need to add two more nozzles to it. It's always kept up and if that's there, there's no reason that system should be down.
Kilger - 13:39
You mentioned this kind of optical eyes, which I'm guessing are just cameras that watch the truck as it goes through. Is a lot of the system pretty automated then? Do people just kind of pull up, it sees a vehicle come and then it starts up by itself?
Bailey - 13:54
Correct, so you said it's kind of their cameras they're not cameras they're more just like on your garage door when it detects something there the garage door goes back up and says don't go down a kid is standing there that's what we use they're a little bit the ones on your garage door are very basic these are designed so that they can see through water and a lot of things like that the only thing they can't see through is. Something solid like a piece of steel. And it's pretty simple. We use a micro PLC, which is a programming logic controller. So there, what it is you can program different things in there. Now, depending upon, cause we can design them to meet anybody's needs. Okay.
Bailey - 14:31
So some people just want them set at the entrance of a facility and they just more or less put an awning over the top of it to keep it from getting wet. And with that being said, there's a photo eye as they pull up to it, it turns on. They drive through it, it turns off fairly simply. In other places, as we start to get more advanced, they'll pull up and there's access control on a small building where they might put your RFID badge. So they'll scan an RFID badge or it scans an RFID on the vehicle, which then tells an access control system, okay, this vehicle is here, open the doors to the facility. So it'll automatically open the entrance door and the exit door, and the vehicle then drives through. And as they're through, it automatically closes the door on the facility.
Bailey - 15:16
So that's as it starts to get a little bit more advanced, not, they're not all like that. And then, they go all the way up to what we say is our, our fully automated, where we've got, we're putting detergent on the vehicle, undercarriage and extensive undercarriage wash, and then the sanitizer application. And with those, typically there's an access control or a touch button panel out front. Where the driver can just press what type of wash they want. So they might want a full wash and sanitize, or they might want just an undercarriage to rinse and sanitize, or they might just want to sanitize.
So they can select those different options as they're doing it. The one thing that's always typically done at those facilities is sanitize no matter what, you're going to get sanitized.
Bailey - 16:01
We've got some very large customers and they will have their trucks go through and get washed once a week. But that same truck might be sanitized five times a day. So they'll go through and get an undercarriage blast and sanitize, or they might just drive through and get sanitized, but they'll only get washed once.
Just to make sure their fleet looks good, but then they get the rest of the different applications. So there are countless ways that it can be automated. To meet the client's needs and what they're looking for.
Kilger - 16:34
Yeah. And that's a little side benefit of having your fleet look a lot, lot nicer. Companies spend a lot of money to get decals and stuff on the side of those feed trucks. It's nice that people could see them on the road.
Bailey - 16:46
Well, that's huge. And the maintenance benefits of it, I think outweigh a lot of the other parts, especially since we're located up here in Michigan. But I know that Iowa, I mean, a lot of the Midwest is in areas where there's a lot of salt. Grosses on the road in the winter and those just eat up expensive vehicles so just rinsing the undercarriages of them off extends the life and the maintenance costs go way down when you do that. So it's kind of a two-fold and we always kind of say if you're putting in something automated already you might as well add a couple other things to it and then you can use it for a lot more purposes than just sanitizing. You can keep your fleet looking great as well.
Kilger - 17:24
Yeah and cheaper than bringing it to some kind of truck washing place and stuff if you want to keep your vehicles clean. Well, I'm a Wisconsin boy myself so well aware of the salty roads in the winter.
Bailey - 17:40
A lot of the time when they do take them to these truck washes, it's usually a minimum of 45 minutes I've heard up to two hours waiting. And then it usually takes around half an hour when you're in there. So to have to pay a driver that amount of time to sit there, or if they own their own, it usually takes around three minutes to pull through a full-size truck wash. Usually, it costs somewhere in the range of $10 or so for them to have it washed, and the undercarriage rinsed effectively. Which doesn't get done at a truck wash because they can't really do it by hand and then sanitize for 10 bucks, they're looking at probably close to $150 to have somebody do it for you. So it can create a return on the investment pretty quickly to automate that process.
Kilger - 18:25
Yeah, and you're not afraid to do it more often. Finding time and cash for that kind of stuff on a busy schedule is never easy. People like examples, so do you have any facilities you've worked on recently that you've put in a new system for that has a good story?
Bailey - 18:39
Yeah, I mean we've got a lot of them and it's public information out there. We work with Cooper Farms over in Ohio, and we've got four different facilities out there. And two of them, they've got two large full-size truck washes with the sanitizer application. And then they've got at their feed mills, at a couple of the small satellite feed mills, they've got the, just the sanitizer applications. So that no matter where that truck is moving, they can make sure that it's being sanitized in inappropriate kind of appropriate timeframes so that they're real big. JFS Milling has got a couple of them down in Southern Indiana there. That one was interesting.
Bailey - 19:16
There was a large outbreak in 2015 and it was all around our property. So that was a kind of, we knew that we were doing something right when the farms around, I mean within the same county got hit, but the ones that had a biosecurity wash there, which was JFS, did not have it impact theirs. So we knew we were on the right track. They've got one now that's going on 20 years and they're going to be replacing it shortly. And that's probably the life cycle of most of our washes is going to be about that 20-year point at which you're going to end up needing to replace it, which is good because a lot of technology changes in 20 years.
Kilger - 19:55
It's pretty universal for most equipment. After 20 years, they're almost always a different beast entirely. I mean, you need to. It's something that The industry seems, at least here in the US, I know it's a lot more over in Europe and things are a lot more stringent about this stuff, but here I visit a lot of feed mills. I think I've been to one with a truck washing system and that's just. At this point, it's something that the industry needs to start investing in. And like I said, it's like just the advantages to tell your customers, Hey, it's an avian, you know, avian influenza out there, but we're good.
Kilger - 20:32
We're, we're sanitized over here. Buy from us. It just seems like a good, good idea to me.
Bailey - 20:40
Right. And then, and we've also been working with Daybreak on a lot of theirs and primarily what we've been helping them out with. Was with the smaller sanitizer application systems and it's kind of a unique situation they ended up purchasing a bunch of other smaller egg farms and when they ended up purchasing it they ended up purchasing one that we had sold a system to and they got to it and they were like this is perfect this is exactly we've been looking for this but we didn't know where to get it and so since that point they've used that as the standard at their facilities moving forward which is great and I'm proud to be a part of kind of Stepping up their biosecurity game and I appreciate the trust that they give to us on that because it is a big responsibility. We've been taking care of a lot of the daybreak ones and we're moving forward with other ones, Fremont Farms, and things like that. So, Tyson, Smithfield, there are a lot of large companies out there that are taking it seriously and implementing new things.
Kilger - 21:38
And as you said, it's not just poultry anymore, right? They might, integrated poultry mills might be the leader in this, but with these diseases spreading to all types of species, I mean, it's getting more and more important to just have this as a standard part of your facility. Are there any other future kind of trends, or advancements that you're seeing out there that you think might be implemented in the next couple of years, or just a way that you see this part of the industry progressing?
Bailey - 22:04
Right. And even if you owned a million, Well, Cooper Farms, for instance, they own all their feed mills and they've got pigs and turkeys and chickens. So for them, it's an all-inclusive, we're going to take care of our own. It isn't even as much about, hey, come get our feed as it is. We have to protect our flock and the pigs and things like that. And it's usually the piglets that are the most susceptible, but getting the piglets safe. And it's the young birds too.
Bailey - 22:32
I mean, those are their largest or most locked-down facilities. And to step into Cooper's because they've been at the forefront of it for a long time and they've set an industry standard that is incredible because they've been taking it seriously for close to 20 years and how they design their facilities with the green and the red zones and gray zones, which is farm dirty. And I've got most of my knowledge from working with the Cooper Farms people and how they have donated and established a routine.
There are some companies out there that are just incredible and hats off to them and everybody's playing catch up. The nice thing that I've always said about a lot of these places, but I'll tell somebody, hey, I've got somebody that's looking at implementing a similar. Do you mind if I share the drawings of your facility with them? And this is not just coopers, but them in particular for this point, they're always willing to give out and say, no, let them see what we've got.
Bailey - 23:34
If they're able to come up with something better, great, but it's great for the industry to bring up their game. So it isn't a separation. It's not, it's people working together within all of the farms, even though you might be a competitor, it's Bringing up, because if one farm down the road gets a flock that gets sick, there's a real good chance your flock's gonna get sick. And then also, if they get sick, there's kill zones and you might lose your flock when you had nothing to do with it. So for them, it's all-encompassing. Let's bring the entire industry to a point at which we no longer have to worry about it anymore. It's created camaraderie, which I just love about farmers in general. It's a Us and not a me or an I type mentality.
Kilger - 24:22
If anyone has any more questions for you or anything like that, where should they go? Where should they get more information?
Bailey - 24:27
You can always go to our website. It's Hydro-chem systems.com. We've got a spot on our webpage for biosecurity specifically. You can also email us. Our basic inbox is sales at hcsclean.com. It would end up getting to the proper person or you can contact me directly. I would say that I've got a team of sales engineers who are prepared to be able to design and work with people.
Bailey - 24:52
However, I do have the most experience and I oversee all of the designs anyway. So you can also just get ahold of me and my name is Keith. And it's [email protected] is my email address. Shoot me an email and I'd be more than happy to kind of discuss your specific situation and what might be a solution to your issue and make something that's high on your mind to something that you don't even think about anymore.
Kilger - 25:21
Yeah, that's great, and much of that information will be linked in the show description right below. Thank you so much for taking the time to talk with me and the listeners today, Keith. And for everyone out there, thank you so much for listening. Until next time, stay safe.