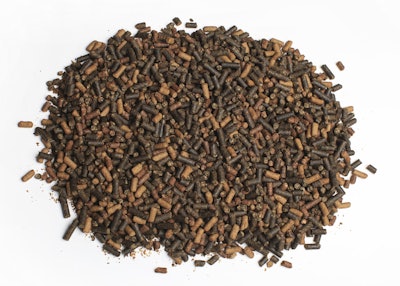
The production of safe animal food is a top priority of animal feed manufacturers. The Food Safety Modernization Act’s (FSMA) Current Good Manufacturing Practices (CGMPs) rule highlights the importance of risk management systems in the mill, including the testing of raw materials and finished products.
“Within FSMA, testing of finished products may be a tool for ‘verification of implementation and effectiveness’ of a preventive control,” says Henry Turlington, the American Feed Industry Association's former director of quality and manufacturing regulatory affairs, noting FSMA 507.49. “As an example, testing a pet food for Salmonella (hold and release) would provide verification of the implementation and effectiveness of processes to control the hazard requiring a preventive control. Such testing would only be part of your standard operating procedures. However, FSMA rules do not require product testing for animal food products.”
To discuss how testing factors into a hazard analysis and critical control points (HACCP) or similar risk management system, Feed Management spoke with Elaine Vanier, DVM, animal welfare & animal feed program lead with NSF International.
Feed Management: Describe how testing technologies are best used to support a feed mill’s HACCP program.
Elaine Vanier, DVM: Testing and sampling programs verify that the HACCP plan is being appropriately implemented and validate that the plan is effectively controlling the identified animal and human hazards.
Test results will cumulatively provide the facility with scientific data to support the requirement for regular evaluations of the effectiveness of the entire HACCP plan. This information will inform the need for any modifications to the plan.
Appropriate testing programs can detect any obvious biological, chemical or physical contamination risks as well as other product quality risks. Product testing for pathogens, mycotoxins or other identified hazards can encompass raw ingredients, packaging materials, in-process materials, rework or finished product.
Raw ingredient and packaging material test results can be used to determine whether those ingredients and/or materials meet contracted supplier specifications and are safe for use in the manufacturing process. The results can be used to support a supplier assurance and approval program.
In-process materials, rework or finished product test results can provide indications that the prerequisite programs are achieving the desired results and that critical limits established for control points have not been exceeded. Test results can be used to:
- Determine appropriate disposition of tested product
- Assess equipment performance critical to feed safety, e.g. adequacy of a mixer to distribute ingredients uniformly within a specified mixing time
FM: How do feed mills benefit from finished feed testing?
Vanier: Finished product test results can provide indications that the prerequisite programs are achieving the desired results and that critical limits established for control points have not been exceeded.
Finished feed testing can validate that the HACCP plan is effectively controlling the identified animal and human hazards and ensure there is no product contamination after a critical kill step (if applicable).
Testing of finished feed can also provide verification of appropriate feed formulation and meet final product specifications, including specific product labeling to ensure the quality and integrity of the feeds supplied to customers.
FM: Does the feed mill environment pose any special challenges?
Vanier: Every food safety and quality control program should include appropriate testing plans.
The challenges can occur in the sampling plans which can vary in their ability to detect a pathogen or identified hazard based on a number of factors related to the feed characteristics and feed mill environment. These factors include:
- Size of batch/product lot
- Distribution of contamination or target hazard within a batch/product lot
- Number of samples collected
- Sampling technique
- Sensitivity, specificity and the time required of the test
Because many feeds or feed ingredients are minimally processed, it can be expected that these will have some level of microbiological and/or chemical (pesticides, herbicides) contamination. But facilities may be limited by the ability to manage a “hold and test protocol” depending on the time required to achieve the test results. If finished feed is released prior to obtaining final test results, it can lead to a product recall if the product does not meet critical limits for contamination.
FM: How would you suggest addressing these challenges?
Vanier: The use of accredited laboratories can address the limitations an individual facility could encounter, including the cost to set up and operate a laboratory.
Using an accredited laboratory for testing services can ensure access to state-of-the-art, specialized and precise analytical equipment and technical competence of laboratory personnel. It also will have the ability to concurrently run multiple analyses and provide quick turnaround of results with robust sample traceability and recordkeeping systems.
All of these factors will help ensure finished feed has been tested and meets the requirements of a finished product.
For more information about NSF International and its technical and auditing expertise, visit www.nsf.org.