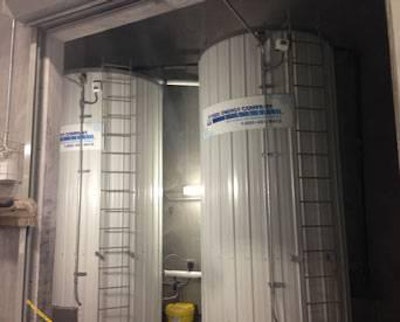
I hate buying cars. That is probably why I am driving an old truck with close to 200,000 miles. I went into a local dealer recently to consider purchasing a new vehicle. The frustrated dealer tried me to get me to choose whether I wanted a vehicle that has good gas mileage or one that is roomier. I kept telling him I wanted both. He finally told me, “You can’t have both. You have to make a choice about what is more important to you.”
Why? Why do we always have to make choices between two seemingly important variables? Why can’t we have it all? Feed managers, nutritionists and animal producers are always making these choices. Do we want more protein and less energy, more energy and fewer carbohydrates or even better handling and fewer nutrients?
This trade-off becomes more apparent during the winter time, when feed manufacturers have to make the decision between maintaining feed handling and efficiency by reducing liquid feed usage or to maintain energy and nutrient levels by keeping formulas the same.
Liquid products present benefits, challenges
The advantages of liquid feed are apparent — improved pellet quality, reduced dust and waste and the higher concentrations of energy and nutrients in the diet. However, often times these advantages are outweighed by the poor handling of liquid feed, especially animal fats, during winter months. The high saturated fats in animal by-products have a higher melting point, which means they thicken in colder temperatures. This thickening causes major headaches for feed manufacturers in the form of broken equipment, clogging and decreased pelleting. Liquid feed can also stick to the distribution tubes in the mill and can even cause feed to hang up in the bins.
I was at a local mill late this fall on one of those dark, dreary days that quickly wipes away any memories of summer. Suddenly an alarm sounded in the control panel of the mill, and the manager went to investigate. Before long, he returned with a ball of feed in his hands. Acting ignorant, I asked him what had happened. Of course, he blamed it on the liquid feed, not the miserable weather. It takes two to tango.
The trade-off becomes as seasonal as the holidays, rolling around each year as the weather turns cold. In the name of optimum mill performance, feed manufacturers typically reduce their fat inclusion rates from 8 percent down to 6 percent or below; increase their use of corn and soybean meal; and suffer lower energy levels and higher feed costs. The overall financial numbers may pencil out, but once you factor in feed conversion given up by the reduction in concentrated energy, it is less than ideal.
Blends offer cold weather relief
Some feed manufacturers have found a solution by switching to a more unsaturated liquid feed during winter months. Vegetable-based oils contain the same levels of energy as animal fats but have a higher saturation, thus a lower melting point.
All fats and oils in nature are a mixture of saturated, monounsaturated and polyunsaturated fatty acids. The only difference is the amount of each type of fatty acid. Whether the fat is saturated or unsaturated determines not only the fat’s melting point but also its stability in the feed diet. The higher the level of saturation, the more likely it will become rancid. This is similar to some types of margarine that must be kept refrigerated, yet coconut oil can be kept at room temperature for over a year without going bad.
Unfortunately, feed manufacturers who simply replace animal fats with vegetable oils during winter months in an attempt to lower the melting point and prevent mill issues may be increasing the likelihood of spoiled or rancid feeds.
What is the solution to have both good feed and efficient production during the winter months? The answer is sourcing a blended fat and oil, which has the optimum unsaturated to saturated fatty acid profile that remains both flowable and stable during winter months.
Heating elements keep fats flowing
Another important element of minimizing the impacts of liquid feed during winter months is to verify and monitor your tank heating element, line and tank insulation and heat trace. According to my colleague, Mike Van Weelden, customer service manager for Feed Energy, using the correct heat trace wattage per foot is important to heat the entire distance of the line.
“The correct setting for heating both the tank and the heat trace, along with routine maintenance will add to easier flow of the material,” commented Van Weelden. “General maintenance of these systems is relatively inexpensive and can alleviate significant headaches down the road.”
Don’t underestimate general maintenance
Ensuring the mill is spraying the liquid correctly onto the feed is another important checkpoint in minimizing the impacts of winter conditions. The liquid feed should be evenly fanned over the feed, making sure to not spray onto exposed parts of the ribbon where it will build up. Allowing for proper mixing time will also ensure even distribution.
This winter, instead of becoming frustrated with liquid feed and removing it from your formulas, consider the impacts and options you have to continue its use. Don’t let the salesman make you decide between the benefits of an efficient feed mill and an efficient diet. Choose the model of liquid feed that gives you both benefits through optimized fatty acid levels. And make sure you have the right garage to protect the car all season long. In the end, you will find you are going faster and lasting longer even when the conditions are less than favorable.