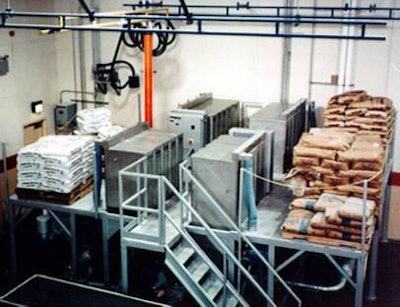
The emphasis on feed safety and a stringent regulatory environment has spurred increasing interest in micro ingredient systems (MIS) in feed mills. According to equipment suppliers, investments in the machinery are split between upgrades of existing systems and first-time buyers looking to transition from hand-add weighing methods for their micro ingredients, such as drugs, vitamins and trace minerals. MIS are split into two categories based on functionality: weight loss and weight gain systems. Traditional weight gain systems continue to be popular due to their price point; however, feed mills focused on traceability, accuracy and batching speed invest in weight loss units. While weight loss systems cost more than traditional units, according to equipment suppliers, the technology is user-friendly, increasingly more economical and pays off in the long run. “If you’re running one bin at a time on a traditional system with only one scale, your batch time is limited,” says Brend King, Intersystems director of sales. “In a weight loss system, you can have all the feeders running at the same time and dramatically decrease your batching time, which ultimately increases your capacity with very little capital expenditure.” This article explores the pros and cons of investing in a weight loss MIS.Weight loss vs. weight gain systems
With weight gain micro systems, each bin discharges individually into a common scale. The load cell takes the weight added to the system and determines when to shut off the bin off. In a weight loss unit, each bin is an individual scale and it can run simultaneously, which allows the user to increase their batch time. It also tracks the weight of each ingredient — what’s been added and what remains — and measures the weight of the product “lost” in the mixer.
With weight loss units, the number of bins can be infinite so long as the facility has the room in its footprint. This makes for flexible installations. Traditional weight gain MIS, in contrast, are limited to no more than 30 bins.
“The bins commonly range from eight to 24 units, but I would say 20-bin systems are the most common,” says Sudenga Industries’ Dale Winter. “The number of bins is typically driven by the species the mill is feeding as some species require more micros than others.” Another advantage of a weight-loss unit is that it provides an on-going inventory at all times and aids in generating accurate records. Both systems have a long product life, with many units lasting over 20 years.Five benefits of weight loss micro ingredient systems 1) Accuracy Both weight gain and weight loss systems remove the “human factor” in terms of ensuring accuracy in feed formulation. However, weight loss units also eliminate a tremendous amount of waste and shrink. “If, for example, the product doesn’t stop flowing, the system will know right away,” explains Dustin Van Cleve, product engineering manager, Intersystems. “In a weight gain system, the operators won’t find out immediately, they end up discovering the malfunction when they do inventory.” Beta Raven’s sales manager Dan Harder agrees, noting that even the best workers may not hit the mark every time: “In addition to the safety implications, the cost of the human element of inaccuracy — either over or under the mark — will cost you money.”2) Traceability and feed safety Weight loss MIS allow feed mills to track and trace everything that enters the mixer with accurate dosages as the weight per ingredient is documented in the database.
“Feed mills are inspected by the FDA annually. Since these visits are unannounced, it is very important to have your records up-to-date and accurate,” Tim Bierman, international and regional sales manager, Easy Automation. Weight gain MIS also offer the residual benefit of workforce accountability.
“Micro systems strengthen ingredient traceability by recording how much of each ingredient is discharged into the mixer — that’s especially true on the weight loss units,” Van Cleve states, pointing to benefits of maintaining an on-going inventory. “If someone were to dump some materials on the floor while trying to load the bins or the 50 pound bag isn’t truly 50 pounds, the unit records how much is added to the bin — which provides a perfect audit trail.”
As a side note, King mentions an increase trend of companies installing scan systems with barcodes on the ingredient bags and their corresponding bins which allow “only the correct bins to open for the correct materials.”3) Worker safety Both weight loss and weight gain systems increase worker safety by limiting their exposure to the ingredients. Feed mills without microsystems require employees to handle every ingredient before it is added to each batch; in contrast, mills with microsystem only require the bins be loaded once or twice a shift. In addition, MIS limits how often ingredient bags require lifting, which reduces injury. “We suggest installing the equipment in a location where it is easy to deliver bags via forklift to the micro skid, creating less labor,” Winter says, further suggesting floor installations to eliminate the risk of employees falling off platforms when bringing the bags up to the hoppers. Production value aside, Harder feels MIS are simply more practical from an ergonomic standpoint. He also suggests companies install dust collection units over the units to further improve worker safety.4) Labor savings All MIS allow the companies to get away from the handling the material two or three times in multiple layouts and multiple batches, which ultimately result in higher labor costs. As feed mills aim to be more efficient and cost-effective, automated systems deliver the reliability and labor saving they are trying to achieve.
“The machine is reliable,” Van Cleve says. “It has one job and one job only to do, and that’s putting ingredients into that mixer, and that’s it. There are many variables that come into play to guarantee the outcome with a human labor force.”
Harder says companies can also free up revenue by getting those guys away from loading the mixer.
5) Easy to maintain
New systems are easy to maintain and the component parts are much simpler to replace.
“Most of the control stuff is handled by a batch controller,” Van Cleve says. “Micro system company controllers are typically intelligent motor starters. They’re storing high-low speeds and so there isn’t a whole lot to troubleshoot on that side.”
Winter suggests the user periodically check oil levels, grease it and inspect for material build up as part of a preventive maintenance program.
Installation considerations
MIS suppliers suggest the feed mills determine the best location for the weight loss MIS while keeping the potential for future additions in mind.
“The big questions are where’s it going to go in the mill, are they going to expand and so on,” King says. “Our systems are very scalable, but only if you plan for expansion upfront.”
Custom MIS configurations can be adapted to fit the space, specifically using conveyors or a blower, Winter says, noting that the amount of bins may determine the equipment’s location within the mill. Harder suggests setting the MIS in the warehouse, near where the plant’s ingredients are stored.
“It’s easier to run a conveyor to the mixer than to try to install the scale next to it,” Harder says.
To install the system, a millwright sets the frame in its designated location, placing vibration isolation pads underneath it. Bins are then placed on the frame. Modern batch control systems make integration as easy as connecting an Ethernet port with an Ethernet cable, Van Cleve says.
“I hope customers take the time to investigate the differences between the two systems, put a pencil to it and realize the ROI of a weight-loss system is on-going,” King says.
The typical return on investment of weight loss micro ingredient systems runs between one and three years.