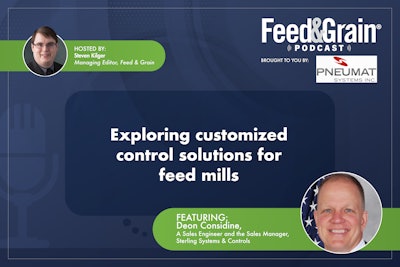
In this episode of the Feed & Grain Podcast, host Steven Kilger dives into the intricacies of feed mill automation with special guest Deon Considine, a sales engineer and the sales manager at Sterling Systems & Controls. This episode explores the importance of customizing control solutions to enhance feed mill efficiency and productivity. Considine shares his extensive 30-year experience in the industry, discussing the benefits of transitioning to automated systems, key considerations for upgrades, and emerging trends in feed mill technology. Learn how tailored automation can transform operations, maximize efficiency, and adapt to the unique needs of each feed mill. Whether you're an industry veteran or new to the field, this episode offers valuable insights into optimizing feed manufacturing processes. Tune in for a comprehensive discussion on enhancing your feed mill's performance.
Transcript has been edited for clarity.
Steven Kilger - 00:00
Hello, my name is Steven Kilger. I'm the managing editor of Feed & Grain Magazine and host of the Feed & Grain Podcast. Thank you so much for listening today as we dive deep into the issues affecting the feed manufacturing, grain handling, and allied industries.
Today's episode is brought to you by the BinWhip from Pneumat Systems. The powerful dual-impact BinWhip removes the toughest buildup and blockages in industrial storage silos without hazardous silo entry. Learn more today at binwhip.com.
Today I'm talking with Deon Considine, Sales engineer at Sterling Systems & Controls. He's here to talk about why feed mills should consider customizing their control solutions to fit their operation, what should be considered before any control solution upgrade, and how best to transition to a new system.
I hope you enjoy the interview. If you want to help out with the podcast and are listening to this in a podcasting app, please rate us and subscribe. If you're listening online, sign up for the Phoenix Grain newsletter industry watch to see when all the new podcasts drop and to stay up to date with all the news from around the industry. Now, On to the show.
Hi, Deon. Thanks so much for joining the podcast today.
Deon Considine - 01:01
No problem, Steven. How are you today?
Kilger - 01:05
I'm doing great. I hope you're doing well. For anyone who might not know you or your work in the industry, can you tell me a little bit about yourself and your experience in the feed industry?
Considine - 01:16
Yeah, so I'm with Sterling Systems & Controls. I've been with Sterling Systems & Controls for 30 years and celebrated that last November. Still coming up on 31 here shortly. Been in sales, I actually degree in electrical engineering technology from Southern Illinois University in Carbondale and then really came into the industry right into sales and I enjoyed it a lot. I get to see a lot of different industries, very interesting, keeps you on your toes and both customers and you know technology and each industry does things a little differently so.
Kilger - 01:50
Yeah well with 30 years you mostly have a lot of experience. I love our industry because it seems like one of the few industries where people really like to stay in it and stay in a company for a really long time which just kind of gives you this perspective you might not see if you jump around a lot.
Considine - 02:06
Right, and I think you know there's some of that people worry about homesteading sometimes it's referred to different entities but sometimes you don't get to see a lot of things outside the box, you know, and you kind of get caught in that pipe from, you know, top to bottom because that's all you've seen. But my experience of having to see different industries all across the board helps to bring some of that thought process back to the feed industry sometimes.
A lot of times the feed industry goes out because from the 30 years of experience, I have a feed mill is probably the most demanding batching system than anything that I've really encountered. Chemicals can be there close, but the feed industry is very, it's so customized for the end user, for the customer, the feed mill customers to where they have to have hundreds of ingredients, thousands of formulas stored just because everybody has their own unique way of doing things.
Kilger - 03:04
Yeah, and it's not like we're a huge, huge industry, right? Especially here in the United States, there are only so many feed mills. And it seems like for them, they're all laid out a little differently. They all take slightly different ingredients. They all do slightly different formulas. So it's the reason we have Jan here to talk today is kind of about getting their automation and control solutions customized for what they need. Can you tell me a little bit more about why a customized solution A list of keywords relevant to topics that may occur during the meeting
Considine - 03:54
So like you know for a customer that already has an existing process and you're trying to retrofit or upgrade or even a new mill that's one thing that we specialize in is you know we really customize it to the way the customer's equipment is and the process is and we've heard that from you know a lot of our customers that they appreciate that we take the time and listen to them and customize it seems like
Kilger - 04:36
The quicker you get someone like you involved in the whole process, seems like the better. What should feed companies kind of start when they want to implement a control solution like this? Where do you start? Where do you call you? Do you take a look? Do they make an inventory of all their equipment? How do they kind of go about this process?
Considine - 04:56
I mean for us, a lot of times it all starts with a flow diagram, a process, or an ingredient flow. So it kind of takes the ingredients through the equipment for the flow diagram. So a lot of times you know on a green site usually is one of the first things we get to see.
For an existing customer a lot of times it's you know they may have that documentation but if they don't a lot of times we'll do a site visit and from there we can kind of look at the equipment talk to the customer and sketch that process. A lot of times we'd like to present the flow diagram to the customer to make sure we truly understand their process and we'll go back and forth with the customer to get that right so that way then when we move forward with the proposal we know that it's correct.
Kilger - 05:41
Yeah, what are the major kinds of factors that would, I guess, need a big change from what you do, like standards? So like, is it the way they receive rain? Is it the amount of formulations they make? Is it a lot of ingredients they use? What are kind of the big things that might change your automated control systems?
Considine - 05:59
Yeah, a lot of times with that is just going to be with a proposal. Everything is driven off of IO or inputs and outputs, all the equipment. So a big piece of it is receiving. Is there one or two receiving legs? A lot of times There's a grinding process in the intermediate between when you receive and with whole corn you'll grind it typically before you get to the ingredient bins. And then when you get to the ingredient bins, you know how many you have, they're VFD controlled or they're just a single speed control. And then of course the number of scales in the batching process is a big driving factor.
Considine - 06:34
You just kind of keep walking through the process, so then you go to pelleting, you know, over there we talk about grinding, there's also flaking potentially.
Then once you're done with the formula through the batching system, you know, you've got your mash, does that go to pelleting or, you know, does a customer just have straight loadout?
And then from the loadout side of it, is there packaging, bagging that you're going to or direct loadout to a truck or potentially to loadout bins? And a lot of that is just how automated a system can be to where you put in the formula, how much you want, and the destination, and the operator at the start, and then they more or less walk away.
The system will produce it route it and take it right to the loadout bin.
And then you have level indicators in there that you can proof things when you do load out. Sometimes you're loading out onto a truck scale. Where that can be verification that what you made and what you produced is actually all in the truck just to verify that you don't have any product left over anywhere.
Kilger - 07:33
Feed facilities really do run the gamut, huh? You have those that produce a hundred different feed varieties and bags and all these things. You know, integrated ones that do one formula basically and put it in the trucks every time. So the idea of kind of getting it off-the-shelf solution becomes really impractical once you think about it, doesn't it?
Considine - 07:52
It does, it's the flexibility of the bashing system that makes their job easier and helps them be the most efficient they can be. And if you've got real rigid, sometimes you just go to like a, what we refer to sometimes as a set point where it's just, you get one through 20 and that's, it can't change the order, which in the industry is not really acceptable on that side because it doesn't give you the flexibility to rotate your ingredients around or things like that.
Kilger - 08:21
Especially since these controls and the solutions can do so much more than they used to be able to now and are so much more, I would argue, needed now than they have been in the past with labor shortages and all these other quality control issues.
Can you give us an example of a feed mill who had a successful implementation of one of your control solutions and the impact it had on their operations?
Considine - 08:45
The biggest piece of that is going to be The transition from a manual feed mill to an automated feed mill is just ultimately the time savings. It's an efficiency thing because the controls will always maximize the use of the equipment, so it'll make the feed as fast as it can mechanically. But at the same time, it's doing that, when you transition to a customer, it frees that operator up to where they don't have to be holding buttons and they're not truly as engaged Need to be engaged as much.
They're more supervising, so it frees. You could say it would be a reduction in labor. What it does is I think it repurposes a lot of times the operators to be able to multitask then, where before they were pretty much dedicated to standing in front of a control panel. Now they can start a formula, start a batch, and actually multitask, and do another thing, so it opens that up for the customer to maximize the labor force.
Kilger - 09:41
Especially because, I mean, making feed eight hours a day every single day is kind of a tedious, monotonous job at the end of it. So I'm sure your employees also appreciate being able to be freed up to do other things, do the things they're best at. Automation takes care of this thing that I don't know. I mean, maybe there are humans that are really great at it, but to me at least, sitting there eight hours a day, making sure each formulation goes through correctly. Are there any big challenges that come when feed mills start transitioning to an automated solution? And how do you normally overcome those?
Considine - 10:26
I don't know if there's any huge transition. It's going to be more of just training, really. I mean, making that transition as smooth as possible. A lot of times, That transition to an automated system, kind of starts in the beginning when we do the process flow, we do a proposal, we come to an agreement with the customer. And then from there, we have our internal kickoff meetings and project management meetings. And then when the system's completed, go through all the approvals of the, you know, electrical approvals, sequence of operation approvals.
Considine - 11:00
So we have a factory acceptance test. And that's where we offer the customer to come in and actually put formulas in and simulate running a batch through the system. That's something we offer here at Sterling free of cost to customers. And with what we learned from COVID, we actually can do that remotely now over the different forms and that.
We try to make that transition as smooth as possible, going through actually hands-on operation here before it ever gets in the mill so that way When you're actually in the feed mill and you're already familiar with it, it makes them a lot more comfortable. And then the training even continues on site. Even when you're at a startup and there's downtime where they're working on equipment or the electricians are doing things, you're training operators in that downtime. Make that transition smooth.
Kilger - 11:45
Definitely. And it sounds like you guys do a great job of that. I mean, everyone needs training or you can't expect it to go over smoothly without a bump, without telling people how to do it. Right. So, it's great that you guys do that. And especially the like testing method, I've never heard of that. That sounds amazing.
Kilger - 12:01
And I'm sure a lot of facilities really appreciate that.
Considine - 12:05
It takes that edge off of the transition so that, you know, a lot of times operators in the process of Automating a system, the operators are just running the feed mill so it's typically the plant manager or others start the ball rolling and then at the end it's kind of they get operator input through the process of that but ultimately, in the end, it's getting the operator to see it before they're ever standing in front of it in the feed mill with that deer in the headlights look what do I do?
Kilger - 12:32
Especially when you've been doing it the other way for 20-25 years and then like here you go. I mean, I have to ask you this question. I feel like I'd lose my podcasting license if I didn't. Are there any emerging trends in feed mill automation and controls that the industry professional should be aware of? Especially with you working in so many other industries, you might have some real insight into what's going to be coming into ours in the next couple of years.
Considine - 12:59
A lot of it is just people being mobile, being able to operate, you know, old school is you're in a control room and that's where you run in the mill from. So I think a lot of that, based on technology changes, kind of giving the operators the capability to be moving so that a lot of times they can have the applications running on tablets, phones, things like that. So I think that's part of evolving. I think we're right in the middle of that. And it'd be interesting with the emerging trend of AIs becoming, you know, very relevant in the world, but how that fits into the feed mill piece of it, we're still kind of evaluating that may be more Helpful on being proactive on maintenance and AI I think probably could also help with the analytics of the feed mill.
Kilger - 13:45
You get all that data it's really hard to break down on your own and make improvements on your own so you think AI would really help with things like that.
Considine - 13:52
Because it all comes down to again for the feed mill it's all about tons per hour, tons per day, tons per week so for every if you've got a bottleneck somewhere sometimes you don't see it where I think with the all the data collected and with the upcoming AI that can help maximize the efficiency of the mills.
Kilger - 14:10
So how important is it to work with someone like yourself when implementing a control system like this? Because it seems like you're in a position to kind of really help the process along.
Considine - 14:25
It all goes back to having the experience in 30 years in the industry. It definitely is a help because it's kind of one of those things where you've been there, done that. So you know the questions to ask and sometimes you even challenge a customer, well, why are you doing it this way?
If there are certain areas in which you see potential improvements, you can always kind of talk through that with the customer. And sometimes it's even, on my part, it's good, like I mentioned earlier, not to challenge the customer, but to ask them why. Because again, even with 30 years, I'm learning something every day. But the biggest part is to experience the right questions to ask and just to avoid any headaches in the end.
Kilger - 15:05
Yeah, definitely. Well, if people are interested after listening to this, where can they find out more information about Sterling Systems and you yourself?
Considine - 15:15
Definitely visit our website, just launched a new website about a month ago. So it’s sterlingcontrols.com and then feel free to call our office direct at 815-281-3587 and just ask for Deon. If I'm not available, there's definitely someone who can step in and take your call.
Kilger - 15:36
Excellent.
Well, thank you so much for talking to me, Deon. I hope to have you on again soon.
Considine - 15:41
Thank you, Steven. It's been a pleasure.
Kilger - 15:43
All right, and thank you everyone out there for listening. Until next time, stay safe.