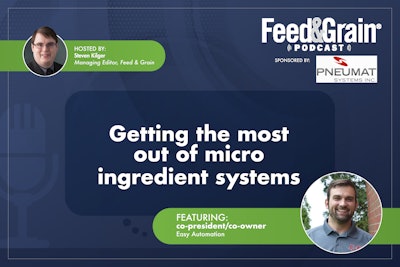
In this episode of the Feed & Grain Podcast, host Steven Kilger, managing editor of Feed & Grain Magazine, talks with Brady Gaalswyk, co-president and 2nd generation owner of Easy Automation. They discuses micro ingredient systems, from how they improve feed mill efficiency, how big they can get, when they aren’t the best option for an ingredient and new technology that can make them more accurate and save employees more time.
Podcast sponsored by Pneumat Systems.
Transcript has been edited for clarity
00:00 - 01:05
Steven Kilger
Hi, everyone. My name is Steven Kilger. I'm the managing editor for Feed & Grain Magazine and the host of the Feed & Grain. Thank you so much for joining me today. As we dive deep into the issues affecting the feed manufacturing, grain handling and allied industries.
Today’s episode is brought to you by The BinWhip from Pneumat Systems. The powerful Dual Impact BinWhip removes the toughest buildup and blockages in industrial storage silos – without hazardous silo entry. Learn more today at binwhip.com.
In today’s episode, my guest is Brady Gaalswyk, co-president and 2nd generation owner of Easy Automation. We’re talking about micro ingredient systems, from how they improve feed mill efficiency, how big they can get when they aren’t the best option for an ingredient and new technology that can make them more accurate and save employees more time.
I hope you enjoy the interview. I enjoyed talking to Brady, and if you want to help out with the podcast and are listening to this in a podcasting app, please rate us and subscribe. If you're listening online, sign up for the Feed & Grain Newsletter Industry Watch. Now on to the show.
Hi, Brady. Thanks for joining me today. Can you tell me a little bit more about yourself and what you do for the industry?
01:05 - 01:31
Brady Gaalswyk
You bet. Well, they still allow us to join. A little bit of background about myself. My name is Brady Gaalswyk, co-president here at Easy Automation as well as part of the second generation. Originally started by my father, so I've been involved in the industry through our family for many years, and our focus is around feed mill and agronomy automation, specifically feed mill equipment.
01:31 - 01:45
Kilger
I always forget that you're a second generation. I feel like I need to get you and some other guys on just for that conversation. What's it like to grow up in this industry? Because it's got to be a unique experience, especially looking at it from someone like me who came into it out of college and never did anything with it.
Well, we're here today to talk about what is a micro-ingredient system and how it works at a typical feed mill.
01:45 - 02:38
Gaalswyk
Yeah. So a micro ingredients system essentially adds those smaller inclusion amounts, which typically focus on the vitamins, the minerals, or potentially the medications as well. They get added as part of the feed mill ration or microsystem, most commonly feed mills add those by hand, So weighing each ingredient by hand.
So implementing a micro-ingredient system, just there are a lot of benefits of having this add-on. But the first one, of course, is not the need for that labor and having to sit there and weigh out each one of those ingredients over and over again.
02:38 - 02:55
Kilger
Yeah, well, it seems like in the old days mixing used to kind of add more feeling to it. Now it's much more of a science, right? Like they are definitive things that you need in, in certain amounts for any recipe you're doing. So how do these systems kind of like ensure accuracy and consistency in a way that even a hand batching system can't?
2:55 - 04:29
Gaalswyk
Yeah. So as you mentioned, it's kind of interesting that in some ways we have so much of the mill automated sometimes this part of the mill isn't as automated, but even though these ingredients of a small inclusion rate it doesn't seem like you're adding very much, those can be some of the most expensive ingredients for the total ration and the most the ones that need to be the most precise for both are pricing or costing standpoint.
And even more importantly, to make sure it matches up with what that formula called for. Why did the nutritionist put that into the formula and ensure that the animals then perform at their peak? Even just little changes in not putting the right amount can have a huge impact as compared to maybe some of those other main ingredients which are more commonly even automated.
That just really emphasizes the importance of automating in a micro ingredient system. So how it does that a little bit is what it's doing is this way now each ingredient. So the benefit of that is that implements the automation where it is weighing out that ingredient, saying how much it called for, the exact precise amount that it was added, and being very precise in the amount that was added.
And then the full traceability is implemented, ways to improve the accuracy and traceability of that as well. But being able to look back and see exactly how much was weighed out really just gives a lot of confidence to the mill and ultimately the producer or the animal owner. That feed was produced in a way that was requested and very accurate.
04:29 - 05:02
Kilger
Yeah, and it gets that consistency in the product, right? You want your customers to be able to know that they're buying the same formula that they bought last time. No differences, no changes. No one guy accidentally does another scoop of calcium by accident messes the whole thing out. If I'm a feed mill manager and I am looking to either invest in a micro ingredient system for my current mill or I'm building a new one, what are some of those factors that they should be considering when selecting a micro ingredient system?
05:02 - 08:00
Gaalswyk
Because they come in all kinds of well, they all look roughly the same, but they come in many different sizes and shapes, right? Microingredient systems can come in all different sizes and shapes. And can I ask why all these different ones? But they each have their specific application or I should say specific range as well as price points.
Some are more economically made for that. In smaller feed mills it could still be important that they have a microsystem, they just don't put as many tonnes through that. So, therefore, they're looking for a little more economical and then medium and then up to very complex, very sophisticated micro-ingredients, systems that the very same equipment and technology could be utilized in human food consumption, or pet food consumption or the like.
So it just has a wide range of types and that kind of finish, the type of hardware that's provided. But first what we do when we look considering a micro ingredient system, is basically to look at what are the ingredients that you're putting that in by a hand edge or that type of inclusion and which ones make the most sense to replace the micro ingredient system is really can depend on the type of the animal that it is.
So like a commercial mill where you maybe have a wide range of species, a wide range of customers. Everybody has a little bit different variation of or different types of ingredients they want to put in adds. Quite frankly, it might never make sense to have a micro bin for absolutely every single type of ingredient they could throw at you.
So what you do there is then maybe look at the most common 80/20 rule. All right, What is going to have the most bang for its buck in the what are those ingredients that get put in almost every matter and a consistency? Identify those and allocate them. It's much more straightforward if you're an integrator or you're producing the same type of feed for a specific species that your choice of hand is.
And those types of ingredients are just going to be much more limited. So therefore it's just going to make you that much more sense and likely not need as many beans from there. We usually look at I have people give me example formulas or we look at what's the most some of the most common formulas where those inclusion rates of those specific ingredients total batch.
How big is your mixer? So how much not only are we putting in each ingredient and calculating the right amount of scales and how to spread over the right amount of scales, that hits your correct matching times, but also from a capacity standpoint, right? Some formulas may only need 20 pounds of this ingredient, and some formulas where if it's a premix, might need 150 parts of this ingredient.
We need to set that microsystem to be able to handle both of those. And so that might look like a different type of micro, a different type of scaling system just really depends on the specific application, and that makes a lot of sense.
08:00- 08:20
Kilger
Some facilities out there have dozens and dozens of formulas with really small, small ingredient needs depending on what stage of the animal they're in. And all that, all that jazz, which is a completely different topic. But there's also your hand-add stations that are you know weigh the product to to make all that more accurate. So even if you're asking to add some of those ingredients yourselves, it's not like the old days when you just kind of guess it's measurement. It's, all that can be automated, even your hand-adding stuff, correct?
08:20 - 12:40
Gaalswyk
I mean, just for some general rules of thumb that we look at, you know, if you're an integrator, if you're on the poultry side of things or commonly you're maybe having that eight bins to 16 bin micro on the swine side of things, maybe more like that, 16 to 20. Then micro again on the commercial side. Just what makes the most sense for your application, how much hand you're trying to eliminate?
We've done several systems. One of the largest was two microsystems, each with 40 bins. So the total of 80 bins on that. And then they had a 12-bin loss and weight system as well. So close to 100 different over 90, but close to 100 different ingredients through some type of microsystem and different ones allocated different systems depending on the inclusion rates and requirements around each.
You mentioned that sometimes depending on what ingredients you need to have in the formulation, might change how you want. The system design is involved like how much they stick and all that kind of stuff. Does all that go into the calculation of what you need going in different types as well a lot of it's based on the total batch size and how much capacity we're going to need once specific differences are when we're looking at those very, very expensive or precise ingredients, such as medications, we're not only just have to be very precise in how much they put in, but also we're going to want to reconcile that inventory at the end of the runs and want to have the weight of the individual bin. That's a great fit for our loss-weight type system because it's able to dispense it out, be able to be very accurate, and uses multiple bins simultaneously, and a great application for that is dispensing directly into a mixer or gaining weight. What happens is comes out of the micro bin into some type of scale.
Then that gets dropped into a conveyor to the mixer. So that's very common and it's most economical for most ingredients. But, you know, there are some transfer points along that way for the potential for contamination, for medication in or a loss in weight system. We can put them just directly over the mixer and truly into the same hole that the hand would be getting dropped into.
So there's no chance of contamination between batches. So what are the common challenges you find people having when they are thinking about kind of adding one to either an existing mill or even a building around it? What are some of the challenges you find people run into when they're implementing this kind of system into their feed processing? Well, no doubt with an existing mill, the hardest challenge is space constraints because everybody thinks they build their mill big enough and just like a house or garage, right, you fill up that space.
So finding the space for a micro ingredients system is just one of the biggest challenges. You have to have the space for the micro itself. Then you have to also think about how is the forklift going to access it or access the platform to get close enough to drop those bags off, to then dump into the microsystem as well as then from a conveyance standpoint.
So from the micro system to the mixer, how is the conveyor going to be through there? The more horizontal and the shorter the distance that is transferred, the better that just decreases the risk of contamination. Now, in saying that we've designed systems to be very flexible to give us the most amount of different variations to fix it in.
So maybe that's putting all the bins on one side. We have also the ability to have either very large bins, medium-sized bins, or very small bins where you can fit two bins essentially in the same footprint in just one. The benefit of that is maybe you don't have a lot of space, and even though it'd be nice to have more storage, you only can fit in the space so we can custom design the system to fit in that space as well as work with the millwright or in customer and coming on site, doing the measurements, laying that out, helping to figure out how to roll out the conveyor.
And sometimes just an outside perspective is great. It's a little bit like sometimes you kind of get used to looking at your house a certain way and think would be good to have it one way or were able to come on-site, work with the customer, maybe bring a couple of different opinions or options to them, how would you do it and then come back, dried up and be able to see those in a 3D format to get a handle of how this would fit, how this would flow.
12:40 - 13:01
Kilger
And that's good to hear because I always hate when new technology to implemented it. People need to build a whole new mill because that's just not realistic for most people. And all feed mills should be able to benefit from the newest improvements in these things if they can. So it's nice to see you being able to come out because you're knowledgeable on to you so you know what will fit.
13:01 - 00:15:05
Gaalswyk
Know. Another kind of common thing that we're seeing these days is the concept of going from no microsystem to a microsystem. We also see variations from there. So there's also maybe we have an older microsystem where they just have all their bins, all their ingredients, say 20, 24, 30, all on one scale. Well, the problem is that if it's on one scale, if it's a gain weight system, it can only weigh up one ingredient at a time.
So they said, hey, we increased our mixer size or we've sped up our capacity. We need to weigh up these micro ingredients faster. So I've done actually in several mills, I've taken that same footprint that that old their style and the microsystem was then split that up into two different scales. So half of the bins were on one scale, half around another, and potentially again, because they're utilizing more ingredients, they're pushing more through the mill, also implementing a total system.
We can unload bulk bags as part of it as well, so they can even split what was one scale over to really three, two micro ingredient scales in a total system. So therefore you're essentially triple the speed of that way up as well as on the total system for those very highest inclusion rates, not having to handle all those £50 bags, but instead do it with a forklift and full £2,000 bags.
I've seen Mills where that was the choke point enough that by doing that increased their production of their entire mill between 20 and 30% because it was just waiting on those micros. And if you can use kind of a bulk bag system, why not Can't be fun hauling over those £50 eggs and unloading them in. Absolutely. I mean, we see benefits on the tote system between handling the bags, getting them from the supplier, and any potential liability issues of lifting those bags and stuff.
It is just much smoother and does not have to. I mean, each bulk bag is a 40, 50-pound bag, right? So it's a significant, significant saving as well and when you talk about those larger inclusion rates, it is a good fit because they can algorithm out or feed them out at a faster rate with larger augers than a microsystem would have.
15:05 - 15:24
Kilger
Yeah, and you don't have to do it so often, which would be very nice. It's a complicated bunch of smaller bins that go out into one thing. What is the maintenance like on a system like this? Is it how often do people have to maintain it? How do you make sure it's functioning properly?
15:24 - 15:48
Gaalswyk
In a lot of ways, they are very low maintenance. There are moving parts on them, but it is relatively low maintenance, just generally checking it out, visually, inspecting it again, depending on the type of scaling system, gaining weight scale system, it can be good to open those access covers every once in a while and visually inspect to make sure you're not getting any build-up or carryover contamination.
These ingredients that go through those microsystems are so often the hardest to handle ingredients in a mill. So they're the sticky ingredients for the dusty ingredients and they can build up with not. So it's good to have a little bit of maintenance to ensure that that tub is getting cleaned out properly or that any final scale is leaking out properly.
Any butterfly valves are closing properly and just the overall also on the exterior side of things, right? If you're not taking care of it and the exterior is getting dusty or dirty, it could begin to contaminate and just not last as long. We also even can help prevent that on the front end by having systems that have a vacuum system on the lid so that when you open the lid and dump the bag in there and it is sucking or vacuuming any of that dust and debris out of there.
So not only is it better for the individual dropping the bag in, but it's just better from a general maintenance point of view. And the other big thing is around the calibration and load cells. Read again. These ingredients are very specific. Inclusion rates in the microsystem can only be as accurate as the load cells and calibration allow it to be.
So having your scales regularly calibrated, and regularly checked is important to ensure that you can truly gain accuracy. That can happen.
17:00 - 17:20
Kilger
And well, these always seem like a very they're very labor intensive and they take a lot of time, you know, to hand add ingredients like this right? To change a formulation and be able to automate all that, it seems like it would be a really big boost to me in how quickly you could get the feed made.
17:20 - 18:44
Gaalswyk
I mean, you mentioned earlier, you know, upwards of 30% more efficiency just from this bottleneck. That seems huge to me. How can these systems contribute to efficient feed production, especially in a day and age where labor is tight, fewer people, and you're trying to get more done with less in general? So when I go in a mill, most labor-intensive areas would be around the bagging system as well as the feeling of the finished product and on the back end.
The other one is hand ads or, you know, weighing out these micro ingredients. As you mentioned, labor is such a difficult thing to come by these days, bringing out these ingredients one after another, day after day is a very labor-intensive job with, as I said, potentially some dusty type cereals that you're working with. Not only that, well, it's very repetitive.
It's been a long day weighing these out over and over again. You have to be very careful in what you're doing because these would be so precise and so accurate that it's hard to find that individual who wants to do this day in and day out and does a really good job of it and stays at it. A microsystem doesn't need to take the breaks.
It doesn't show up for work. It doesn't try to get in a rush on Friday. It's just that dependability. It's one of the most common areas. If they don't have one to either get on or add more micro bins to help decrease the labor in this area and allow those people to focus on more of a value-added area in the mill, especially because, unlike humans, it doesn't make mistakes.
18:44 - 19:06
Kilger
I don't care who you are weighing out ingredients all day, every day, you're going to eventually get distracted or you're going to make some mistakes. It's just human nature, right? It's those are the tasks that we're good at. That's why automation exists. So there's the concept of getting it right on the front end. But the huge value is also just the data collection and the recording of what happened in the back end.
19:06 - 19:29
Gaalswyk
So from a liability standpoint, right? So if a feed mill gets a call from a customer that plants that their feeds are made right, or they had a problem with the health of their animals, they're able to go back and truly say this is what the automation said, here's how accurate is here is record time after time. Nope, it did the job it said it was going to do as compared to trusting that somebody measured it outright.
That lack of clarity creates more questions, creates less trust in the whole process, right? So automation and specifically a microsystem helps build that level of trust for that customer that they truly are getting what they want Everyone hates to hear it, but we are entering a day and age where you need more and more backups, you need records, you need paperwork showing everything you've done.
19:50 - 20:11
Kilger
And any time you can take that paperwork away from an individual to have to do and have it automatically filled in in the back end, that's all the better. Right? Are there any emerging trends or developments in ingredient systems? What's what's on the cutting edge? What are you looking forward to?
20:11 - 21:55
Gaalswyk
So I would say it's on emerging trends and developments of micro-ingredients systems is okay. Now we've taken the hand ad aspect away from the individual so we have a more accurate as well as they're not having to weigh out these ingredients all day, every day. However, there are still a couple of opportunities where there is a potential for human error. And so we as manufacturers are trying to take those out. You have all these micro bins and they all have labels and whatnot.
But the concept of a new person would open the wrong bin and dump the wrong ingredient in the wrong bin. The system thinks it has the correct ingredient and keeps away that ingredient. So what we've implemented now is magnetic locking lids. So the actual lids in the microsystem are magnetically locked and each ingredient is given a barcode where it scans the bag to say, this is the correct ingredient, this is X ingredient.
Then you can, then you're going to put it and release it and open it up. Like kind of like if you go to an area where it opens the proper door, allows it to put it in so it only can put it in proper bin for that ingredient. So that's a big area of trend. Another one is we're seeing more and more of what we call our dust-free lid or our vacuum lid.
As I touched on earlier, another model labor that's been needed is just to dump the bag into the bin. So how can we take away that dust, take away that mess, and just overall help with the cleanliness and appearance of the mail as well as any potential for cross-contamination? Again, especially when you're thinking of drugs or some type of ingredient that would kill one species for it's good for another and how to prevent that.
So those are two areas that we're doing the most development. The other ones are just continuing to further refine how accurate these systems can get and how precise they can get.
21:55- 22:15
Kilger
I imagine that's got to be an uncomfortable conversation if you accidentally have an ingredient in the species that ends up killing some, that's not a fun lawsuit to eventually deal with. So I imagine those must be nice. Well, thank you so much for sitting down to talk with me today. I appreciate it.
00:22:07 - 00:22:40
Gaalswyk
Yeah, I appreciate the opportunity that's based on this. As I mentioned, Microsystems is just one main area of opportunity for automation and new equipment to decrease the amount of labor, increase the efficiency of the mill, and increase the level of tracking and traceability. So, I mean, these are the key things that Mills is trying to do these days. And micro-ingredient system is usually at the top of that list if don't already have one.
22:40 - 22:57
Kilger
And I'm sure if any listeners out there have questions, you would be happy to answer them at Easy Automation, where we'll have all your website and everything linked in the description of this podcast.
So go check them out and thank everyone out there for listening. Have a great rest of your week and stay safe out there.