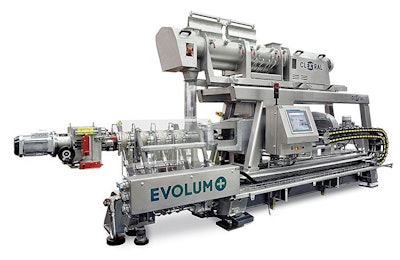
As a continuous processing machine, the twin-screw extruder (TSE) is designed to provide consistent and repeatable production — every shift, every day. As with any machine, maintenance is essential; however, poor or incorrect procedures can cause production losses and costly repairs.
Here are some important steps to help ensure efficient operation:
-
Check machine alignment and gearbox timing
It is critical for a TSE to have the rotating parts perfectly aligned — motor, gearbox, screw-shaft assembly, barrel assembly — in order to avoid problems generated by misalignment, which can cause extra wear or stress on the shafts. Manufacturers will properly align new extruders prior to startup, but it may drift after years of production.
Likewise, proper gearbox timing, i.e. the relative orientation of the two gearbox output shafts, is key to avoid excessive friction in the extruder. Typically, the two gearbox output shafts have identical orientation; however, power failures, blockages in the screw/barrel assembly and improper control of main motor torque can cause excessive torque on the gearbox output shafts, causing one output shaft to move relative to the other. This results in poor output shaft timing which is translated to the screw assembly and can result in friction between the screw pairs and between the screws and barrel assembly.
A full machine checkup (wear monitoring, gearbox timing, etc.) is recommended once a year. If the equipment runs nearly 24/7, then wear monitoring every six months is wise. However, when installing a new machine, quarterly wear monitoring is recommended while the equipment operators are still in the learning curve.
-
Conduct regular wear monitoring, measurements
Extruder wear does not happen overnight. A well-maintained extruder typically wears slowly and consistently over time. Once your machine is mechanically sound (as described in point No. 1), it is key to document how the wear pattern of the screws and barrels develops over time by making regular measurements of the screw element diameters and barrel bore diameters.
First, this will help the processor to order replacement parts in advance and anticipate maintenance needs. Second, it monitors whether the wear is suddenly different, highlighting that something has potentially gone astray. These wear measurements provide good data to decide whether premium metallurgy will be appropriate. Premium metallurgy is more expensive but leads to reduced operating expenses. This analysis will determine where along the screw-barrel profile it may be needed. (It is not always necessary to utilize premium metallurgy everywhere, only in high-stress zones.) Certain premium metallurgies can also be very helpful for corrosion resistance.
As screws and barrels wear, they become less efficient at conveying product through the extruder so the filled zone within the barrel increases. That means more of the total length of the screws and barrel are exposed to higher-stress operation: the parts that would normally wear slowly begin to wear much faster to compensate for parts that are too worn out to perform their function. Understanding this and replacing the worn parts in a timely manner can help to minimize wear on other parts.
-
Ensure proper startup and shutdown procedures
Startup and shut down are two critical moments in extruder operation. They need to be done rapidly but softly to prevent, for instance, running the machine at full speed without any product in it. For each recipe, a specific startup and shutdown can be set. Avoid lengthy screw operation with an empty extruder or with only water in the barrel. To minimize wear, this operation must be brief and conducted with the lowest screw speed possible. In normal operation, a barrel filled with product effectively acts as a bearing for the screws, keeping them centered in the barrel bores; however, in an empty extruder or one only containing water, the screw will rest on the bottom of the barrel bores, causing friction. The higher the operating speed, the more wear occurs.
-
Train, train and re-train
Training shouldn’t be limited to new hires. There is a constant need to train and re-train equipment operators and the maintenance team. Through training and proximity, you can establish the best processes and procedures to keep your extrusion platform in best operating shape.
Training recommendations
As for the training, take a staggered approach:
- Off-site training and testing: Hold training sessions at the manufacturer while the extruder installation is nearing completion at the production facility. This is important for a new customer who is not accustomed to the technology. It is also an opportunity for an off-site test with the product formulations, allowing the client to "play" with a machine without the pressure of production.
- Installation: Conduct training during installation for the maintenance staff and at startup for maintenance, production, etc.
- Supplier machine audits: Ask your supplier if it can provide specific full-training programs on demand, in the pilot plant or at your plant to address specific questions. It is especially beneficial if you have multiple production sites, as it will ensure consistent procedures in each plant. Even if additional training is not organized during the machine audit, it is a great idea to have one or two mechanics work with your supplier’s technician, which can an informal “refresher” for the mechanics.
Processors that focus on maintenance on a continuous basis have the most reliable equipment. Maintenance does not simply mean fixing what is broken. It’s being proactive. Alignment and timing checks, wear monitoring, proper operation and training can significantly reduce operating and maintenance expenses while minimizing unplanned downtime.