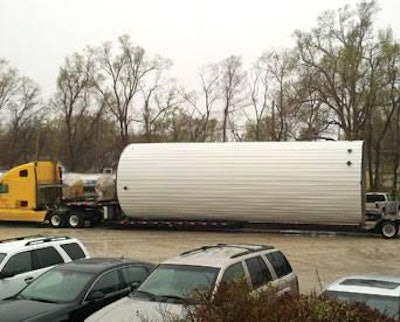
It may seem easier at the time to take the quicker solution, but there is always a consequence down the line, and a liquid feed system is no exception.
Growing up on the farm, my dad would often quote the proverb, “If anything’s worth doing, it’s worth doing right.” And while in the heat of those summer afternoons building fence, the extra crank to tighten the wire didn’t seem worth it, the consequence of chasing cows down once again and repairing the fence didn’t pay off.
Like the fence, with the proper materials and care, the obstacles of liquid feed systems, such as tank corrosion and maintenance costs, can be prevented while increasing your bottom line from the benefits of dietary inclusion of liquid fats and oils.
The right equipment
A regular screwdriver won’t do when you need a Phillips. Starting with the right tools makes every job easier. There is no difference when it comes to tanks and liquid feed systems.
“Clients always ask, ‘What type of tank should I buy?’” says Cal Halstead, Feed Energy director of sales for 18 years. “We always recommend stainless steel, the cone at minimum, and a cone at 45 degrees to go with stainless steel pipes. You are setting yourself up for better results.”
There is no denying that the quality of steel has changed over the years due to a limited supply. Today carbon steel is the standard, cheaper option, but the effect of a cheaper price is that carbon steel will corrode more easily. Yet, higher priced stainless steel has a longer lifespan.
“The 20 percent more for stainless steel is worth it,” says Mike VanWeelden, sales manager for Feed Energy’s tank servicing team. “A stainless steel cone will last for an additional 10 to 15 years preventing downtime and costs in your operation to replace a tank.”
On average, carbon steel tanks are lasting 10 to 15 years while tanks with a stainless steel cone average 25 to 30 years with proper maintenance, according to VanWeelden. This makes the additional years from a stainless steel cone, for just 20 percent more cost, seem very viable.
The cone at the bottom of the tank is typically the first place that issues arise, but starting with the proper equipment can prevent the tank from corroding before it should. A 45-degree cone is a must as anything shallower will allow for product buildup on the bottom of the tank. A 45-degree cone also has enough slope to allow for adequate product flow.
Temperature regulation
Having a heating mechanism for liquid feed tanks is essential, but having any heating mechanism on your tank is no longer good enough. The wrong heating system or one that is not installed correctly are leading causes in tank corrosion.
“Over the last 10 years, several tank failures have occurred due to the way heaters were placed,” notes Van Weelden. “Everyone welded directly to the cone, thus opening up the steel’s pores. Having the heater directly attached to the tank’s cone also provided a place for product buildup, further promoting corrosion.”
Corrosion often begins at the bottom of the tank due to the steel becoming burnt from excessive heat, and the opening of the pores allows a location for the fatty acids in the liquid to corrode.
“Placing the heat source at least 18 inches from the cone — not attached to it — will allow for the heat to be more evenly distributed preventing buildup, and the pores in the steel will remain closed,” says VanWeelden.
The type of heater used can also make a difference when promoting tank longevity. Radiant electric heaters have become the standard as radiant electric heaters are able to maintain a more consistent and even temperature throughout the tank.
Preservation through care
In tank maintenance, buildup is a dirty word — figuratively and literally. Proper tank care will prevent and remove buildup before it can cause corrosion.
Some key points to proper tank care include:
- Annual cleaning While it does cause a few hours of downtime, the cleaning is well worth it to remove any sledge or product fallout, making your system able to operate at full capacity and prevent potential issues. During the cleaning, also be sure to examine insulation on the exterior and make sure it is free of mice or other nesters.
- Make sure your entire system is clear of leaks and debris Nozzles, pumps and the mixer are all key places where minor leaks or debris can lead to larger issues of product buildup and eventually corrosion.
- Check your tank temperature While weather dependent, fat should be kept between 140 to 150 degrees Fahrenheit. You can reduce this to 130 degrees Fahrenheit in the summer for vegetable oils. The best way to maintain a current temperature is by making sure your heat trace thermostat is properly calibrated.
- Monitor the interior of the tank with a bi-annual ultrasound This inside look can show if your tank is getting too hot or if buildup is starting to occur near the cone. This will also allow for you to plan if repairs or replacements will be needed instead of an unexpected shutdown.
- Proper product application and mixing Ensuring the mill is spraying the liquid correctly onto the feed is another important checkpoint in minimizing the impacts of buildup. The liquid feed should be fanned evenly over the feed, making sure to not spray onto the exposed part of the ribbon where it will buildup. Allowing for proper mixing time will also ensure even distribution.
Making sure you have the correct tank, at the correct temperature with a maintenance plan can seem like a large investment of money and time — don’t blame the messenger. However, a job well done extends your dollars and increases your efficiency more than making up for the investment.