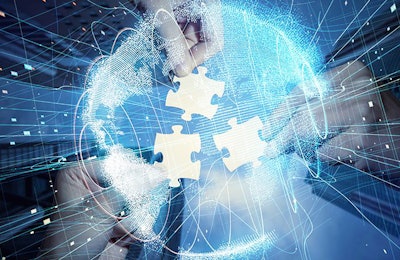
The adaptations made during the COVID-19 pandemic will have a long-term impact on the global industrial sector, including feed manufacturing, animal protein processing and ingredient supply chains.
The short-term crisis adaptations corporations made at the onset of the COVID-19 crisis will play a significant role in shaping the future of manufacturing because it accelerated several industry trends already in play and created new ones.
During market research firm Euromonitor International’s webinar, “5 trends defining the future of manufacturing,” senior consultant Justinas Liuima explored the five ways manufacturing industries and supply chains will forever be changed by the pandemic.
Rethinking supply chains
Companies have been forced to adapt to uncharted global market conditions, which, in turn, have driven them to re-evaluate their operating strategies to prepare for unplanned challenges in the future.
“COVID-19 has exposed how unprepared companies were for supply chain disruptions, and they found they did not have sufficient crisis contingency plans,” Liuima said. “Better planning and risk mitigation would help to improve transparency and flexibility of the supply chains, and this would improve their reaction during the times of any unexpected shocks or crises.”
For example, companies operating in the “new normal” will increasingly seek to regionalize and localize their supply chains to diversify their operating risk.
“Instead of relying on several narrow suppliers, they will aim to create a network of smaller suppliers,” he said.
According to Liuima, companies can better manage their supply chains by assessing potential changes, estimating the available inventory, identifying potential demand for the product, and firmly and realistically evaluating logistical performance.
“Based on these four factors, companies then can optimize production volumes to potential demand and component delivery changes,” he said. “In addition, greater transparency and communication across the supply chain would make it easier to adjust production in a timely manner.”
Top trends shaping the manufacturing sector’s future performance
Based on his observations, Liuima has identified five trends taking hold and changing the landscape of the global industrial sector, including in the agrifood industries.
1. Transition toward demand-driven supply chains
“When we consider a demand-driven supply chain, it is not enough to rely on seeing what your customers need, but also what the end consumers need, and understanding consumer trends will help with cost and inventory management in the long term,” he said.
Greater transparency of the supply chains allow companies to track demand changes and adjust production accordingly.
The food products industry, one of the first to react, started offering direct-to-consumer sales models during the pandemic, skipping the retail industry as an intermediary and approaching the end consumer directly, a move “anticipated to help improve brand loyalty.”
“At the moment, this this is mainly related to the B-to-C market, but it is very likely that this trend will catch up in the B-to-B segment as well,” he said.
2. Embracing digitization and automation
According to a recent Euromonitor survey, 60% of companies plan to reshape their digital strategies and invest more into ecommerce; with more than 30% of respondents also indicating their plans to accelerate investments in automation tools.
“The B-to-B ecommerce market forecast to reach around $15 trillion in 2025, with transport equipment, food and beverages, and transportation industries [slated] to lead the growth,” he said.
In addition, investment in new automation systems will help companies improve production efficiency and output.
“Based on evidence from various industries, new automation tools help to improve production efficiency from 3 to 5% depending on the industrial sector where the company is operating. On the global scale, this would result in total gains valued at around US$1.3 trillion each year,” he said.
Most of the gains will be achieved due to better production planning processes, including the elimination of bottlenecks, smoother product design and product launches.
“COVID-19 showed how digitization tools, which were often overlooked by manufacturing companies, help to improve operational efficiency, make production more flexible and better cope with the new challenges,” he said.
3. Increasing focus on greater flexibility and supply chains
To improve supply chain flexibility, Liuima points to new automation tools and digital technologies to diversify supply chain risks, which range from autonomous robots to 3-D printers, big data analytics and other software tools.
“By combining these factors, manufacturers can actually create a network of smaller factories or sometimes referred to as micro factories, which can operate efficiently and remotely, and this helps increase supply chain and production flexibility,” he said. “Also, by operating closer to the end consumers, the companies can also reduce transportation and logistics cost.”
For example, the success of “micro factories” shows that small and collaborative environments have significant value and can be used to make supply chains more flexible and resilient.
Companies may also invest in semi-independent, regional producers to minimize their supply chain risks. Based on operating cost analysis, companies may relocate portions of their Asian production to regions operating at costs lower than Western Europe or North America, i.e. Eastern Europe and Latin America.
“We anticipate more companies will start diversifying their supply chains and this trend should really accelerate in the following two to three upcoming years.
4. Repurposing manufacturing capabilities
This is an emerging trend where companies can look for new ways to utilize their manufacturing capabilities outside of their primary industry.
“To do this, companies first need to create more flexible supply chains and improve collaboration with existing players in that supply chain,” he said. “By doing that, when the factories find synergies with other industries, they can better utilize the resources and expertise.”
5. Greater collaboration across industries
COVID-19 showed the importance of effective communication channels, with companies aiming to improve internal and external communications.
“Manufacturing industries have really long supply chains and improved communications would bring more benefits to them,” Liuima said. “Overall, better communications would help to speed up information flows across the supply chain and in turn would help to reduce our product development time and response times during emergencies.”
Open communication channels will also help with collaboration efforts between suppliers across the supply, existing supply chain and supporting industries.
“Inter-industry collaboration could help to speed up recovery and better cope with the existing challenges within the industry and the economy,” he said. “Increasing collaboration efforts may also provide new expansion opportunities for contract manufacturers.”
Contract manufacturers typically have an efficient and flexible supply chain — achieving the best compromise between price time and quality — and can fill in the production gaps during the peak times.
As manufacturing companies aim to quickly diversify their supply chains, they may need capacity, which exists in other factories.