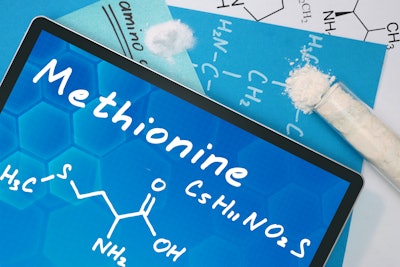
A team of University of Connecticut (UConn) researchers is developing a natural alternative to produce an essential amino acid used in poultry feed with support from a US$500,000 grant from the National Science Foundation’s Future Manufacturing initiative.
The team is led by Mingyu Qiao, assistant professor of innovation and entrepreneurship in the Department of Nutritional Sciences in the College of Agriculture, Health and Natural Resources (CAHNR). The team includes three faculty members from the Department of Chemical and Biomolecular Engineering: Yu Lei, centennial professor, Yongku Cho, associate professor and Burcu Beykal, assistant professor; and two other faculty members within CAHNR: Yangchao Luo, associate professor of nutritional sciences, and Rigoberto Lopez, professor of agricultural and resources economics.
This project is also in collaboration with Patrick Heidkamp, professor of environment, geography and marine sciences at Southern Connecticut State University.
This marks the first time UConn has received this grant and is Qiao’s first grant since joining the UConn faculty this year.
The group will develop a novel biomanufacturing technique to produce an essential amino acid called methionine.
Methionine is an essential amino acid for many animals, including humans. Poultry, which is are the focus of this study, use methionine to grow feathers. Chickens with a methionine deficiency are too skinny for market and produce low-quality eggs. Critically, animals cannot produce methionine themselves, so they need to get it from their diet.
Most methionine supplements are produced using petrochemicals. This means existing methionine supplements cannot be fed to organic chickens. It is the only dietary supplement for poultry which does not yet have an affordable organic alternative, creating the need for a sustainable solution. The only option is to bio-ferment methionine, which costs approximately US$43 per kilogram. The method Qiao’s group is proposing would only cost US$6 per kilogram.
Qiao’s team is using edible microalgae, a nutrient-dense superfood, to produce methionine organically. Using something that is already edible eliminates the need for further modification to turn it into feed for chickens or other animals, making it a cost-effective solution as well.
“It is a carbon neutral, or even carbon negative process for producing methionine,” Qiao said. “Overall, the entire process is very environmentally friendly.”
Like plants, microalgae can use sunlight to produce nutrients, including methionine. However, using photosynthesis alone is a very slow process that produces relatively little methionine. Microorganisms, on the other hand, can grow much more quickly, but this is an expensive and carbon-intensive process. Microalgae combines the best of plants and microorganisms to produce methionine quickly and sustainably.
“Microalgae combines the advantages of being able to grow very fast, but it can also use sunlight without using an organic carbon source or carbon feedstock,” Qiao said.
Scientists have already been able to extract six other amino acids from microalgae for poultry feeds, making it a particularly good candidate.
Qiao’s team will develop a prototype for a photobioreactor which can be implemented in greenhouses across the state. This novel biomanufacturing method will allow the microalgae to use sunlight during the day to produce methionine and carbon sources at night.
“During the day it will kind of act as a plant and at night it will act as a microorganism,” Qiao said.
They will also develop an artificial intelligence (AI) model to determine, essentially, when the algae should act like a plant and when it should act like a microorganism based on the availability of sunlight or other essential nutrients to minimize costs. The AI model will automatically calculate how much of a given resource, like sugar, is needed to optimize methionine production.
This seed grant will allow Qiao and his team to collect preliminary data and develop prototypes of the photobioreactor and AI model, preparing them for future grant applications to advance this work.
The grant will also include workshops for underrepresented high school and community college students to help prepare them to enter the biomanufacturing workforce in collaboration with Southern Connecticut State University.
“In order to develop a future biomanufacturing industry in this area, you need to have workforce,” Qiao said. “Hopefully we can use this opportunity make a more equitable society or community. Because, in the end, it will benefit society as a whole.”