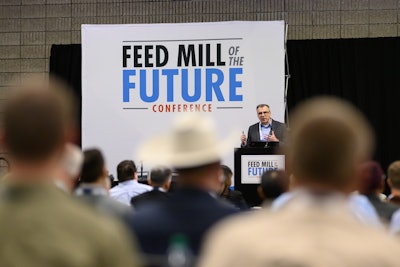
There are many aspects of feed production where improving efficiencies can save time, money and resources, according to eight experts who participated in the 2024 Feed Mill of the Future Conference.
Held during the International Production & Processing Expo (IPPE) in January in Atlanta, Georgia, the conference explored how efficiency, innovation and sustainability will shape the future of the feed industry. The event is produced by Feed Strategy and Feed & Grain, and organized in partnership with the American Feed Industry Association (AFIA).
Reducing emissions
Relying on tools such as life cycle assessments (LCA) and following sustainability guidelines from the Food and Agriculture Organization (FAO) of the United Nations can help feed manufacturers reduce their greenhouse gas (GHG) emissions and contribute to a more sustainable food supply chain, according to Dr. Milan Hruby, vice president of creation design and development for ADM Animal Nutrition.
ADM’s Strive 35 sustainability initiative outlines the reduction of Scope 1, 2 and 3 emissions 25% by 2035, the reduction of water withdrawal 10% by 2035 and the reduction of energy usage 25% by 2035.
Scope 1 refers to a company’s direct emissions from facilities and vehicles; Scope 2 are indirect emissions from purchased energy sources; and Scope 3 are indirect emissions from purchased goods and services, distribution and downstream processing.
ADM’s Scope 3 emissions are its leading source of emissions, and 80% of these emissions come primarily from purchasing commodities from farmers.
“Purchased goods and services is our largest category and where we have the biggest opportunity for influence,” Hruby said. “We introduced programs that focus on no deforestation of raw materials and another on regenerative agriculture.”
Regenerative agriculture uses a systems-based approach to sequester carbon in the soil and intentionally improve soil health, biodiversity, water quality and air quality while ensuring the viability of farm production.
Improving energy efficiency
The pursuit of energy efficiency is a critical objective for feed manufacturers but must be achieved without compromising productivity to remain economically viable, according to Jerry Plessing, industry consultant for Rockwell Automation.
Balancing energy efficiency with production requirements presents a challenge in that strategic decisions must support the broader objectives of profitability and meeting customer demands.
“We talk a lot about ‘WAGES’ – water, air, gas, electric and steam – because of their interdependence,” Plessing said. “Some things we can do to improve energy efficiency may not be the best in terms of production.”
To strike the right balance, Plessing outlined a journey of key phases manufacturers can advance through towards optimal energy efficiency: connect, analyze, optimize, control.
The connect phase emphasizes the importance of measurement and comprehensive data collection on power consumption, material flow and other critical parameters. Comprehensive data sets enable thorough analysis and informed decision-making.
“We start here because we can’t control what we’re not measuring,” he said.
Collecting data from various sources is critical, because Plessing said as manufacturing facilities evolve, energy inputs will be incorporated as raw material alongside traditional inputs — such as grains, feed additives and proteins.
“Many times, we’re collecting steam flow capacity, but doing so just at the boiler,” he said. “I may have multiple pellet mills in my facility and if I’m not taking that steam consumption down to the mill level, how am I going to optimize that particular mill’s operation? Make sure to get granular and detailed enough information for that.”
The analyze phase marks a shift toward proactive engagement with data, moving beyond mere reporting to actionable insights. This involves comparing and identifying patterns and relationships within data sets to contextualize it. Plessing stressed the importance of data organization in this phase to better utilize the information gathered.
Mathematical models, informed by empirical research and operational expertise, play a crucial role in translating data insights into actionable strategies.
Plessing described the optimize phase as “where we make the data useful,” and feed manufacturing operators transition from being reactive to proactive. Facility optimization provides insight and decision support with advanced analytics.
The roadmap finishes at the control phase, where advanced operational technology enables real-time responsiveness and adaptive control mechanisms. Here, manufacturing plants leverage data models on the device level to adjust operational parameters to maximize energy efficiency without sacrificing productivity.
Enabling a circular economy with insects
Insects provide an opportunity to tackle dual challenges for the future food system: increased protein demand and optimized organic waste management.
“Insects eat waste — they live on the waste we generate from different foods,” said Thierry Duvanel, director of innovation for Bühler Group. “If we’re able to set up an industry where we use these losses to feed insects, they can be used for protein content as feed. Then we have a new economy taking place and this is already starting to happen.”
Insects embody circularity by recycling nutrients from organic waste and reintegrating them into local feed and food value chains.
“Circularity is not a new concept. It makes a lot of sense to try to extract value from all parts of resources,” said Maye Walraven, North American general manager and chief impact officer, Innovafeed. “But I think it’s becoming more of a trend or more of a priority because we are feeling environmental pressure.”
Insects such as black soldier flies (BSF) and mealworms can be used as a protein source for feed applications, as they convert waste into food while the remaining byproduct, known as frass, serves as fertilizer within the agriculture sector.
While BSF – which thrives on wet feedstock, has a relatively short reproduction cycle and substantial protein content – has emerged as the preferred choice for most feed applications, mealworms offer another worthy option. Mealworms require slightly longer reproduction cycles and live on dry feedstock, which Duvanel said can be an advantage, depending on the application and the environment. They’re used primarily for feed, but also can have food applications.
Once the industry is built up, Duvanel said we can begin to consider using insect protein resources for direct food applications, pointing to crickets as the leading contender. They have much longer production cycles than BSF and mealworms, but account for a lower environmental footprint than animal protein production.
Utilizing artificial intelligence
Feed mills are not taking advantage of the full range of benefits artificial intelligence (AI) can offer to their business, said Ben Allen, CEO of BinSentry.
Ben Allen, CEO of BinSentry, explains how feed mills can utilize artificial intelligence to improve their operations.Paul Ward
He said feed mills operating the “old” way – estimating bin inventory by hitting the bin with a mallet, for example – will be left behind if they don’t embrace new technologies.
“Farmers and field staff hit bins with hammers or rocks to take an inventory reading … and then they send it in to you and you use that as your data point to drive your entire business,” Allen said about this inexact method. “Your average EBITDA is about 4.5% globally, and you’re selling US$550 billion worth of products. And the dataset is coming from a hammer.”
By utilizing AI and sensors such as ones that can measure the exact amount of an ingredient inside a bin, monitor feed consumption, set mill production schedules and order ingredients, and set delivery schedules, mills can run much more efficiently.
On top of having much better data, feed mills can execute their tasks better with AI. Having AI run animal feed supply chains results in 12% lower transportation costs, 95% less time spent tracking inventory and 75% less out-of-feed events, Allen said. And, by lowering the number of out-of-feed events, feed conversion ratio is improved as well.
“Put down the rocks and the hammers, keep your people safe and solve the data issues and let the computers do the simple stuff so that your labor, which is so hard to chase, can do the hard stuff and take care of customers and keep the animals fed and worry about the difficult problems,” he said.
Michaela Braun, senior liquid systems and sales specialist, Novus, agreed that AI can be used to improve efficiency at the feed mill, as well as fill in some of the gaps created by labor shortages.
“Let’s use our automation, let’s use AI, let’s let our computers train themselves to a point that it takes the pressure off of us,” Braun said. “Our workforce is changing, and it’s getting harder to staff feed mills. … The world is changing in a way that it’s trying to help us as far as technology goes.”
Optimizing nutrition in NAE systems
Feed additives can improve digestibility and the nutritive capabilities of feed, according to Dr. Dulmelis “DG” Sandu, poultry technical support services veterinarian for Alltech.
“We need to rely a little bit heavily on these as we proceed into no antibiotics ever (NAE). … One of the things I always tell people is look for products that have multiple modalities,” she said.
This means using products that have direct and indirect effects and may have several different properties such as immunomodulatory, antifungal and anticoccidial.
By utilizing feed enzymes, more nutrients are available from the same feed. Additives such as probiotics, prebiotics and phytogenics can optimize gut health, which is important to overall health and welfare of the animals. Food safety and quality can be improved with mycotoxin binders, and other additives can lower ammonia and methane emissions.
“I cannot think how we would operate today without feed additives,” said Dr. Christos Antipatis, global SMT additives director, Cargill Animal Nutrition. “Nutritional and zootechnical additives are important to meeting nutritional demands. Without them, the animals will have to eat for longer and also will have to produce a lot more waste.”
Nutritional needs for poultry have changed over time, with birds producing more meat and putting more muscle on a better frame.
“We know that that bird is going to require more energy; that’s going to require more feed. Therefore, we must keep those needs in mind in going forward,” Sandu said.
Performance is “the first factor of improving sustainability because if you can feed the animals with less ingredients, you’re ultimately reducing the amount of pressure on the planet,” Walraven said.