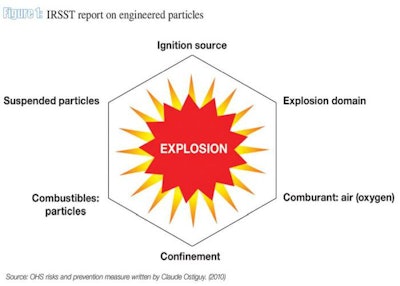
The nature of raw materials and the processes involved in feed manufacturing seem to make feed mills susceptible to dust explosions.
In Europe, dust regulation is dealt with under the ATEX directive, which consists of two EU directives: one for equipment (94/9/EC) and the other for work environment (94/92/EC). Under this directive, employers must classify zones where hazardous explosive atmospheres might occur and improve the company’s ability to decrease its insurance contribution. To help feed manufacturers manage their risks and organize their zones, French technical center Tecaliman performed studies with researchers from the National Center for Scientific Research (CNRS), in Nancy, France, specialized on dust explosions.Dust, particles contribute to risk
An explosion is a very rapid combustion provoked by temperature and increased pressure. Prevention and protection demand specific equipment and actions to reduce the fire risk (elimination of one of the fire triangle elements) and decrease pressure dangers, e.g., an explosion event.
Feed mills use a wide range of raw materials and produce several finished products that must also be assessed for their flammability and explosive potential. Several studies, which have been published by scientists, give data of dust flammability and explosive potential of “ideal” products, generally one by one. But in the industry, products are rarely alone. Humidity level and particle size, as well as chemical specificity of products and mixes, also have their impact on risks. Efficient industry management thus demands tests to be conducted on “real” materials and “real” conditions. Or, for best management, to conduct tests with worst-case scenario characteristics, i.e., testing with the finest dust available. For example, International Organization for Standardization (ISO) normalization demands a sample preparation with a 63-micrometer (µm) sieve. The maximum size of particles that can form an explosive dust cloud is 500 µm while there is no lower limit, explains the Quebec Occupational Health and Safety Research Institute (IRSST) report written by Claude Ostiguy. Generally, as particle size decreases, the risk of explosion and ignition increases.Identifying the ‘explosion hexagon’
To improve feed producers’ knowledge regarding the flammability and the explosivity potential of their products, the French technological center Tecaliman conducted four series of tests with the Laboratory of Chemical Engineering Sciences (LSGC), a specialized research lab that is part of the CRNS, led by Laurent Perrin and Olivier Dufaud.
The explosion hexagon shows the conditions required for an explosion to occur. The basis is the “fire triangle,” the presence of an ignition source being one of the factors, with combustion (oxygen) and combustibles (particles) being the other two. Going from the fire triangle to the explosion hexagon demands three more factors: a dust cloud in suspension; the explosibility domain, i.e., dust concentration must be higher than the minimum level of explosibility, which varies depending on the nature of the dust; and confinement (otherwise the phenomenon will be a “fire bowl”). Any augmentation of dust temperature when it’s mixed with combustion (air) increases its energy. This explains why some ignition might begin spontaneously. Any initial particle combustion will cause ignition of near suspension zones. Thus, the flame naturally contributes to flame propagation in the dust cloud, preceded by a pressure wave of hot gas. One must not underestimate the impact of initial blast wave: The initial explosion will trigger suspension of particles which, in turn, causes secondary explosions throughout the facility, aggravating damages. The most common explosion regimen in feed plants is deflagration, where the blast wave runs in front of the fire at a rate of a several dozen meters per second. The pressure increase will then reach 4 to 12.105 pascals. When deflagration occurs within a close compound, overpressure is usually from seven to eight times the initial pressure. Another type of explosion might occur in pipes or long rooms where the ratio length/diameter is higher than five. Then, flame velocity becomes supersonic and overpressure may exceed 30 times the initial pressure. “Nowadays, it is admit that dust explosion will be possible only if solid combustible is finely divided (particle diameter well under 1 mm), in suspension in the air at a concentration between 0.01 and 1 kg/m3, and if ignition source is placed near or inside this volume of suspended particles,” summarizes Fabrice Putier, Tecaliman director.Ignition triggers
Two items define the ignition and explosion potential of a product: its ignition sensitivity, which understanding is very important for prevention, i.e., maximum temperature of equipment surfaces, fighting against static electricity; and its explosion severity (its behavior in case of explosion), which is used to establish protection, e.g., the size of an explosion event.
The ignition sensitivity of a product will depend on several factors:
- Minimum Ignition Energy (MIE) of dust/air mixture
- Lower Explosion Level (LEL) defines the minimum concentration in the air in which an explosion can occur
- Minimum Ignition Temperature (MIT) might differ if dust is in cloud and in layer
- Lower Explosive Limit (LEL)
Powder explosion severity will be defined by two characteristics:
- Maximum pressure during an explosion (Pmax)
- Maximum velocity of pressure elevation (dP/dt) max, basis for the Kst calculation; Kst being a constant.
Feed products studied for explosivity
Tecaliman’s latest studies on explosion aim at gaining a better physicochemical knowledge of feed plant dusts, collected on the grinder filter, three premixes and five final feeds.
The plant’s contents of premixes were 51 to 53 percent for Premix 1; 2 to 4 percent for Premix 2; and 20 to 22 percent for Premix 3. The three types of products showed very different reactions. The three tested premixes showed nearly no sensitivity to explosion. Complete feeds are more sensitive to explosion, and their explosion severities are higher than premixes but stay at a low level. With no surprise, filter particles are the material with the higher explosion sensitivity in the mill. Some patterns appeared, even if the comparison is difficult. For example, a link seems to exist between mineral content (ash content) and the tests results. Products with the higher ash content (premixes) are less sensitive to ignition and their explosion severity is low, if not zero. Regarding final products, even if their characteristics differ, it seems difficult to link feed formation and feed ignition or explosive characteristics; maybe raw material mixing results in homogenization of those characteristics. With its high ignition sensitivity and ability to create the severest explosions, the dust layer that collects on the grinder filter is the riskiest product in the mill. To improve the industry’s knowledge on feed dust and explosion risks, Tecaliman and the Nancy lab will conduct additional studies. Those first steps show that for all feed products tested the Kst, which is an index of the maximum rate of pressure in a dust explosion, stays between “0 and 105,” values that place those products on the lowest product categories for explosion severity and ignition sensitivity. One must keep in mind that the tests were conducted under the worst case scenario, e.g., lower humidity than encountered in a typical feed plant, lowest granulometry, highest ignition energy. Even if it presents the risk of dust explosion, the feed industry is shown to be less risky than grain storage as raw materials and finish products are not stored onsite for very long.