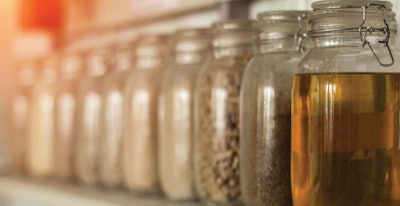
In animal feed quality management, sample preparation often can be improved.
Feed manufacturers require grain and feed analysis and testing to comply with regulations and to abide by their voluntary testing programs. Research and development departments use testing results to identify the best nutritional criteria and requirements, to study the relationships between nutritional requirements and production efficiency, but also to assess new raw materials. In formulation, nutritionists use them to learn about raw material variability and to control quality when they physically enter the factory. Analysis is also quite useful at the process level and, of course, more widely to control biosecurity.
Analysis is one of the cornerstones of assuring feed quality. But even if feed manufacturers make huge investments to maintain their own lab and/or arrange for analysis by an accredited laboratory, how do they ensure the lab is utilizing the right representative selection of their production?
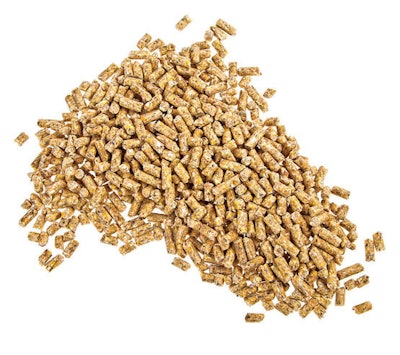
Conducting feed analysis
Some samples are poor even if sampling mustn’t bear all responsibility for measurement uncertainty. As a mean, French feed factories spend a lot on analysis — around EUR0.35/ton (US$0.39/ton) — when some years, they gain no more than EUR4 to EUR5 per ton (US$4.50-US$5.60). In other words, reducing analysis costs without degrading their relevance is of strong economic interest.
Raw material management is one of the main areas of interest. A 120,000-ton plant will buy for EUR3 millions of raw materials and every optimization through accurate formulation might represent its annual profitability, explained Etienne Laffitte, Wisium technical director.
“The definition of formulation is simple even if the job is complex — assembly of raw materials, at the best of their nutritional values to achieve predetermined values at the lowest cost,” Laffitte said. “Accurate analysis plan to know raw material qualities and to adjust may even represent feed plant profitability as our sector economic equilibrium is very narrow.”
Raw material variability is real and may be very important from one year to another, and from one batch to another, depending a lot on diverse factors, i.e., wheat or corn variety, soil, cultural practices, field localization, storage conditions, etc. Formulators need very accurate data and are, then, able to reduce feed costs.
On the contrary, and apart from economical hazards, results in accuracy might also result in some regulatory problems. For example, when on analysis reports, the feed is said to contain more than an authorized level of contaminants.
Ensuring feed testing accuracy
To level down uncertainty, one thinks first of lab technical efficiency. Ring tests and official controls are some effective levers, but a lab can only analyze what it receives. Thus, it’s the feed manufacturer’s responsibility to send representative samples.
“Sampling is not as easy a technique as it appears,” said Fabrice Putier, head of French technical center Tecaliman. “The sample aims to provide information, and sampling quality is the basis of final quality of information itself. Anyway, sampling is a science, which induces its own bias.”
Sampling presents the material necessary for measurement so that the average value of the batch can be evaluated and estimated based on the x-value obtained by the measurement. Beyond the theory, this definition shows the reality of the uncertainty between the actual, unknown, content of a component in a batch and two other values: the actual content of the component in the sample and the final measurement of the component.
The actual total sampling error is the sum of systematic errors and random errors (bias) during each step, from batch to final measurement.
In the case of particles and grains, warned Putier, basic heterogeneity induces an inevitable error in sampling called Fundamental Relative Error: “Indeed, the existence of a form of heterogeneity in feed is inevitable because of the variability in the size of the constituent elements of a batch (granulometry), the heterogeneity of constitution, the possibility of agglomerates of particles, often underestimated, and the heterogeneity of distribution, often more visible. Heterogeneity depends on the substance being sought, on how it is distributed in the particles and on the sample size (or the number of particles). The fundamental error is, therefore, the minimum incompressible sampling error.”
Official sampling rules admit empirical rules. The advice is to use the fundamental error as a basis for determining the tolerable error and the total weight to be taken; to ensure sufficient correction so that the bias (sum of the other errors) is less than the fundamental error; and, excluding extreme cases, to assume that the deviation will be at least twice the fundamental error.
Collective self-checking shares costs, improves efficiency
French feed manufacturers have been actively involved in the collective improvement of feed safety for farm animals. As early as 1978, feed manufacturers in France’s Brittany region created Qualimat Association to control imported raw materials.
The association widened its actions, developing, for example, guidelines for quality management and certification on transportation, e.g., lorries. Since the “hygiene package” in 2006, European regulations demand that every feed manufacturer implements a self-checking plan. It is difficult to build a plan at an individual level, so another association, Oqualim, was created by the three professional trade unions to support both the certification system for the good manufacturing practices guide for feed and premix plants and a collective self-checking plan. The latter allows participating companies to contribute, through higher verification, to the safety of feeds.
It didn’t take the individual self-checking obligation away, but increased the relevance of analysis and decreased the “pen mesh size.”
“Oqualim self-checking feed section proposes a collective analytical plan on chemical and biological contaminants in feed, mainly through feed materials,” explained Celine Ravel, Oqualim director. “This plan’s purpose is to ensure, at a collective level, sufficient control by carrying out analyses at the most relevant point in the production chain. Beyond a collective response to regulatory obligation, Oqualim offers a tool that contributes to the safety of all chains by monitoring quality in real-time.”
In France, 197 factories produce 86% of the country’s feed and are part of the collective self-checking plan for feed; 52 plants producing 97% of complementary feed are part of the specific components of the self-checking plan. Oqualim has also developed three others dedicated self-checking plans for milk replacers (which cover 89% of French production); GMO-free (153 members) and organic feed (20 plants, which equals 85% of French organic feed production).