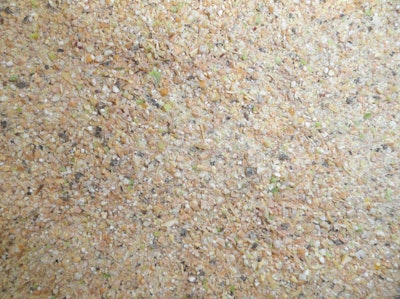
The influence of equipment and settings on particle size and particle distribution during feed processing
Most raw materials used in feed mills must be ground. This process improves the performance of the animal and feed processing, especially mixing homogeneity and pellet quality. Grinding is a key step in the feed production process and offers numerous possibilities for modification and optimization.
Characterization of particle size, influence of the type of mill
The two main parameters that define particle size are particle size distribution and d50value. Particle size distribution defines the proportions of the particles with a specific size in a sample.
Figure 1 shows the cumulative (continuous lines, sum of all proportions) and the density distribution curve (dotted lines, single proportions). The d50value is the average particle size of this particle size distribution. This means that 50% of the particles are finer and 50% are coarser than d50(see figure 1, marked with a red line). Bulk materials with the same d50value can have deviating particle size distributions. This demonstrates the importance of both values for the characterization of particle size.
Figure 1 further demonstrates the impact of different kinds of mills on particle size distribution. The narrowest distribution can be achieved with a roller mill whereas a hammer mill produces wider particle size distributions and, therefore, higher amounts of fine and coarse particles.
A further factor influenced by the mill is the particle shape. On roller mills, the product is ground by shearing forces, therefore the particles are more elongated. On hammer mills, the particles are ground by impact pressure, which produces more round-shaped particles.
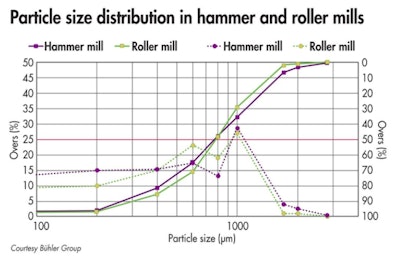
Influence factors on hammer mills
In feed mills, the hammer mill is the most commonly used device, as it enables high capacities, is easy to operate and is suitable for almost all products. Various possibilities for influencing particle size distribution can be found on just one machine. The factors can be divided into machine, process and raw material parameters. The following discussion focuses on the machine and the process-related parameters.
Hammers
In a hammer mill, the hammers constitute the essential grinding element. Particles break when the rapidly moving hammers hit the slowly moving particles. The most obvious influence factor is the number of hammers: the probability that the particles will be hit increases with an increased number of hammers, thus resulting in finer final granulation.
Another parameter is the length of the hammers as this determines the angle at which the particles are deflected from the hammers. This deflection angle can be modified by varying the hammer length. Short hammers with a longer distance to the screen (figure 2, a) deflect the particles vertically to the screen.
The particles can pass through the screen directly as soon as they are small enough to do so. With increasing hammer length and thereby a decreasing distance between the hammer and the screen (figure 2, b and c), the angle of impact of the particles on the screen becomes flatter. The particles bounce off the screen and remain longer in the grinding chamber where they are ground further.
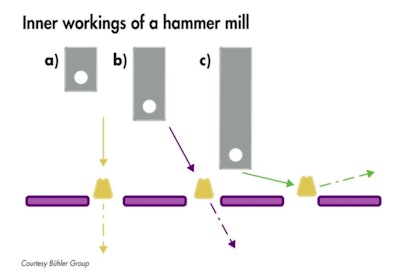
Screens
Granulation can be influenced by the size of the screen hole and the open screen area. The size of the screen hole defines the size of the particle that can pass through the screen: granulation becomes coarser as the size of the screen hole increases. The same effect can be observed as the size of the open screen area increases.
With a larger open screen area, the particles can leave earlier because the probability of hitting a bar between the holes is much smaller. The retention time of the particles inside the grinding chamber further depends on the level of wear of the screens. Worn-out screens have rounded edges, which deflect more particles back inside the grinding chamber. Therefore, worn-out screens lead to finer granulation and wider particle size distribution.
Impact plates and deceleration chamber
The principle of the hammer mill is to create a high velocity difference between hammers and particles. Impact plates and deceleration chambers can help to increase velocity differences by slowing down the particles and leading them back to the rotor. Thereby, the particles are hit more often by the hammers.
The deceleration chamber also causes turbulent conditions and interrupts the circular movement of the product with the rotor and the hammers. This prevents the production of fines due to shearing along the screens. The particles remain inside the grinding chamber for almost the same time, resulting in finer granulation as well as narrower particle size distribution.
Tip speed
By adjusting the tip speed with a frequency converter, particle size distribution can be varied without any mechanical intervention. With increasing rotor and hammer speed, the granulation becomes finer and the particle size distribution becomes wider. Therefore, the grinding process becomes more flexible with a frequency converter, and granulation can be adjusted within a short space of time.
Aspiration
The aspiration of a hammer mill can significantly influence capacity and particle size distribution. With increasing aspiration air flow, the particles get sucked through the screens. Thus, the particles leave the grinding chamber earlier, resulting in less fine particles and narrower particle size distribution. Aspiration and tip speed are factors which can be adjusted without any idle time.
Influencing factors on roller mills
In contrast to the hammer mill, the roller mill is limited in terms of the variety of products that it can process. Fibrous products and coarse products are difficult to grind with this equipment. Furthermore, the process is much less flexible. Particle size can only be influenced by the number and type of corrugations on the rolls and the roll gap. The number and type of corrugations is preset by the selected rolls and cannot be changed easily.
By adjusting the roll gap, the granulation of the product can be modified whereas the distribution curves remain the same. Therefore, the number of fines and coarse particles at a constant d50value cannot be modified.
Influence of step grinding on particle size distribution
Step grinding is the combination of sifting and grinding. The product is sifted before grinding and only the overs —the coarse particles —are ground. Different grinders such as hammer mills and roller mills can be combined in this kind of process.
After each grinding step, the product is sifted again and only the overs continue on to the next grinder until all particles have the desired particle size. This method reduces the production of fines as only the coarse particles are ground, and particle size distribution becomes narrower.
Conclusion
Given all the factors discussed, it is possible to influence particle size and particle size distribution during grinding with existing equipment. However, even when the parameter settings are constant, the process can vary due to changes in the raw material or the level of wear of the hammers and screens.
Early detection of any deviations is essential to achieve the required particle size and distribution. New sensor techniques are able to support feed manufacturers in analyzing particle size distribution in time, enabling immediate modifications to be made if any deviations occur.
Editor’s note: This is the third installment of a five-part series, “All about particle size: the influence of feed particle size on animal performance,” contributed by the Bühler Group. It aims to explain the importance of particle size in pig and broiler feed, and explore the possibilities for modifying and controlling particle size during feed processing.