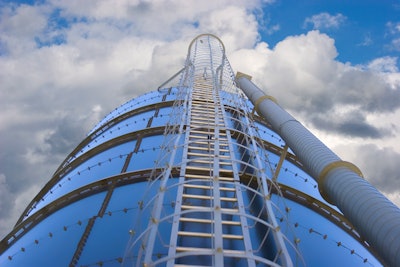
Many people use artificial intelligence (AI) in some way every day, but a lot of feed mills are not taking advantage of the benefits AI can offer to their business, said Ben Allen, CEO of BinSentry.
Allen spoke January 30 at the Feed Mill of the Future Conference during the International Production & Processing Expo (IPPE) in Atlanta.
Ben Allen, CEO of BinSentry, spoke January 30 at the Feed Mill of the Future Conference during the International Production & Processing Expo (IPPE) in Atlanta.Photo by Paul Ward
Smartphones and smart things in homes are almost ubiquitous, but some executives say they are worried about how AI will change how they work.
But, Allen tells them, “you’re talking to these things already. That’s artificial intelligence. You’re using it in your house. It’s coming for your business.”
He said feed mills operating the “old” way – estimating bin inventory by hitting the bin with a mallet, for example – will be left behind if they don’t embrace new technologies.
“Farmers and field staff hit bins with hammers or rocks to take an inventory reading … and then they send it in to you and you use that as your data point to drive your entire business,” Allen said about this inexact method. “That’s what you make your milling decisions on, your trucking decisions on, your labor decisions on, your ingredient ordering decisions. It’s driven off of horrible business. Your average EBITDA is about 4.5% globally, and you’re selling US$550 billion worth of products. And the dataset is coming from a hammer.”
By utilizing AI and sensors such as ones that can measure the exact amount of an ingredient inside a bin, monitor feed consumption, set mill production schedules and order ingredients, and set delivery schedules, mills can run much more efficiently.
“When you can see inside of metal containers and then the AI can take that data and streamline it for you … your costs can drop anywhere from 100 to 300 basis points – 1% to 3%. … That’s anywhere from 25% to 75% profit increase,” Allen said. “All of a sudden, your people at your order desk have the best data in the industry.”
On top of having much better data, feed mills can execute their tasks better with AI.
“You’re running too many trucks and you’re stopping in too many places, I guarantee it. It’s a biosecurity problem. It’s a fuel problem. It’s a driver problem,” he said.
Having AI run animal feed supply chains results in 12% lower transportation costs, 95% less time spent tracking inventory and 75% less out-of-feed events, Allen said.
And, by lowering the number of out-of-feed events, feed conversion ratio is improved as well.
“This type of data – feed conversion rate – is part of the outcome. It’s a key performance indicator,” Allen said. “It’s about waste. It’s about animal health. It’s about trucking. It’s about labor. It’s about quality of protein production. And it’s about the technology that is available today.”
To Allen, the question of whether to implement AI in your feed mill operations answers itself, and for many reasons.
“Put down the rocks and the hammers, keep your people safe and solve the data issues and let the computers do the simple stuff so that your labor, which is so hard to chase, can do the hard stuff and take care of customers and keep the animals fed and worry about the difficult problems,” he said.