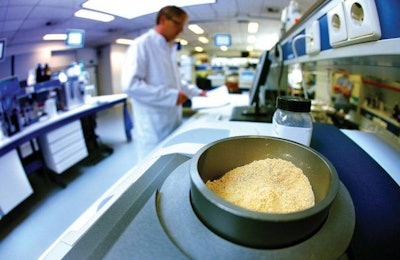
Cargill’s Animal Nutrition Innovation Campus’ lab applications and analytical research facility processes and collects the livestock feed ingredient and nutrition data used to fuel the company’s nutrient management, feed formulation and animal requirement systems.
The Elk River, Minnesota-based lab handles more than 200,000 ingredient samples annually – and that number is growing.
According to Kate Plaisance, Cargill Animal Nutrition (CAN) global analytics director, the department is always looking for “safer, faster, cheaper” technologies to improve its analysis capabilities and ensure the accuracy of the nutrient data.
For this reason, CAN internally utilizes 190 near-infrared (NIR) instruments for ingredient analysis; it also services 240 instruments operated by its feed mill customers and in-field consultants.
However, the analysis team realized more could be done to improve and further expand their ingredient understanding by adopting a method for faster elemental analysis.
“NIR is really great at quantifying organic molecules, but not so great at inorganic molecules or minerals,” Plaisance notes. “We need to measure minerals in our business – those are important nutrients to animal performance.”
To do so, CAN has recently introduced X-ray fluorescence (XRF) analysis instrumentation in its testing lab, “adding another tool to its toolbox” for quickly identifying the mineral composition of its feed ingredients.
Adapting XRF to animal feed formulation
XRF is a highly accurate technique used to conduct elemental analysis on liquids, solids and powders. Unlike traditional wet chemistry methods, XRF analysis produces same-day results, averaging five to six minutes per sample.
Currently, the technology is primarily used in four major industries: petrochemicals, mining, metals and cement.
According to Eric Eden, CAN area analytics manager – North America, Cargill began exploring ways to improve its elemental analysis and the use of XRF technology in an effort to become “more responsive” to its premix business after the company acquired Provimi in 2011.
“[Feed ingredient analysis] requires different types of sample matrices than petroleum or geology so working closely with a vendor on this was critical,” Plaisance explains.
Though it had not previously installed an XRF unit in a feed application, scientific instrument supplier Bruker AXS had the advantage of drawing off the extensive global data points available to Cargill to troubleshoot the validity of the system.
“We were able to cover the range of everything you would expect to see and share it with [Bruker AXS] so they could ensure our data worked with their technology,” Eden adds. “They didn’t have a set method for [feed ingredients] so there was a lot of back and forth communication and showing them what we want to see and defining our accuracy expectations.”
The effort paid off. In May of 2015, the facility implemented the use of a Bruker AXS benchtop S2 Ranger energy dispersive XRF (EDXRF) system. To date, the lab has processed 2,000 samples using the unit. Eden predicts it will run an estimated 12,000 samples annually.
XRF in action
The key to successful NIR and XRF spectrum technology is “a good laboratory program because the wet chemistry ultimately determines the accuracy of the instrument,” reports Eden.
Much like NIR, XRF equipment is calibrated using a set of primary or secondary standards derived through traditional wet chemistry, or other analytical techniques such as Inductively Coupled Plasma (ICP) elemental analysis. The XRF instrument analyzes these standards for elements of interest and develops calibration curves for each element stored in the system’s software.
“Unknown samples are prepared in exactly the same way as the primary standards and are analyzed against the calibration curves to determine the elemental make up of each sample,” Eden explains.
In CAN’s lab, dry, ground ingredient samples are pressed into discs through the application of 20 metric tons of pressure to create a flat surface. CAN’s EDXRF unit has an auto sampler capable of analyzing up to 28 samples – but it typically runs five to six samples at a time. The machine then generates spectral data and applies it against CAN’s models to generate results.
“Samples are hit with X-rays and the electrons move out of their shell and then other electrons fill that space so the machine can pick up on the energy of the element,” he says. “Each element has its own unique signature that can be used to quantify mineral content.”
Plaisance adds, “So when you present the samples to the instrument, it bombards them with X-rays, exciting atoms specific for each element within the sample, and you are able to look at all the different elements in one scan.”
Additional benefits
In addition to rapid mineral analysis, safety ranked high among the unit’s greatest benefits for CAN. Unlike ICP, which requires the use of strong acids, XRF scans are conducted without chemicals.
“Without the use of acids, we are making the procedure safer for the technician and creating much less waste in the environment,” Plaisance says, noting that sample disposal does not require any special conditions.
Also, in comparison to ICP, XRF units produce repeatable results over long periods of time without recalibration. Unit accuracy can be validated daily by running a control sample.
“It’s a plug-and-play instrument,” says Daniel Pecard, Bruker AXS senior applications scientist – XRF. “It fits on a standard lab bench and uses a standard power outlet – no gas. There’s a 20-minute start-up procedure – and as long as the system is turned on – you don’t have to wait much longer.”
Arkady Buman, NA XRF Product Manager, Bruker AXS, adds: “Once you have the instrument installed, your day-to-day cost is basically nonexistent. When you run ICP you have consumables which could run – depending on the usage – up to $30,000 to $40,000 dollars per year.”
According to Buman, the easy-to-use system also requires very little training due to its intuitive, touch-screen interface.
CAN plans to move forward with XRF
Currently, CAN’s sister lab in Spressa, Italy, also operates an XRF unit and the company recently purchased one for a lab in Mexico. It plans to introduce an additional four XRF systems in 2015.
“We’d like to see this deployed in as many locations as necessary,” Plaisance says.
Given its size and scale, CAN has a unique advantage in utilizing both NIR and XRF technology. Eden feels smaller feed operations may have a hard time calibrating an XRF system given their limited access to sample data and may be better off outsourcing their mineral analysis.
Buman agrees, “There’s a lot of potential in the feed industry, but it does need some development.”