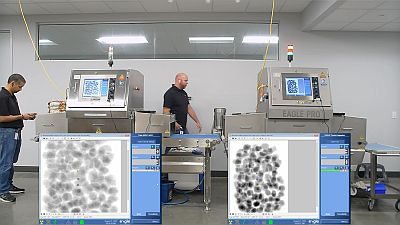
Eagle Product Inspection remote services include options for product analysis and application specifications conducted before a machine is purchased and installed. During the decision-making process, Eagle representatives can discuss applications in a group video conference and conduct virtual pre-testing to demonstrate the machine’s effectiveness based on a manufacturer’s products and specifications. Testing can be live-streamed so customers can watch the process in real time.
In the absence of in-person visits due to the pandemic, remote Factory Acceptance Testing (FAT) is available to ensure that a machine is running properly and in line with a customer’s needs and operations, before it is shipped to its final location.
Following installation, Eagle offers a program called REACH Remote Support Solutions for 24/7/365 off-site support. Those solutions encompass remote monitoring and diagnostics for troubleshooting and for any critical operational issues, enabled via an x-ray machine’s remote access software. Virtual training programs have been extended, too, and include required and regulated safety training and support.